We are experiencing a phase of digitalization that affects all company departments. In the production field, the advent of Industry 4.0 has robotized most of the processes, reducing the physical effort for workers and resulting in safer working conditions.
Offices are undergoing a drastic change, too. Regardless of the size of the company, we are increasingly interfacing with remote work.
As for warehouses, the decision to switch to automated storage solutions is almost expected. In fact, automatic tray-based storage systems have become indispensable for many companies. The only doubt is the following: how to choose between vertical and horizontal solutions?
How do vertical and horizontal automatic storage systems work?
Let’s start from a common principle at the base of both solutions: “goods to person”. The operator is no longer forced to move in the warehouse to pick goods but rather waits for the requested item or order in a fixed and ergonomic position. Both carousels are composed of trays which rotate inside the machine, bringing the stored goods directly to the picking station.
The main difference lies in the configuration of the supporting structure. Vertical storage systems take advantage of the premises’ height, thereby reducing the floor space needed, while horizontal carousels are suitable for those premises with a low ceiling but where the footprint is less of a problem.
In another article we have already extensively discussed the numerous advantages of Modula automatic vertical storage systems.
Now, why choose an automatic horizontal carousel?
Automatic horizontal carousel: The advantages
The automatic horizontal carousel is the high-performance choice for all those industrial activities involving intensive picking operations, not only for distribution purposes but also for production.
As noted, unlike a vertical automatic storage system, a horizontal carousel does not use much vertical space; in fact, it is composed of a series of bins that rotate horizontally on a stainless steel track to convey the products requested directly to the operator in the picking station.
What are the benefits?
- Increased productivity
Since this is an automatic system, which allows operators to reduce their movements, it is easy to understand how much this solution saves in terms of time and gains in terms of productivity. Furthermore, horizontal carousels can be used in groups called pods when placed side by side: while an operator collects the material from one carousel in the pod, the other carousels rotate and prepare the material for subsequent picking operations. This minimizes operator downtime, exponentially increasing performance, and therefore productivity. - Less risks for operators
Operators work safely in an ergonomic workstation. The safety systems prevent all contact with the moving parts of the machine.
In addition, warehouse employees are not forced to climb stairs or other means to pick goods, which ensures a safer working environment. - Optimized space
Products are stored and organized in a compact, high-density storage area. - Goods controlled
All picking operations are monitored and documented, allowing complete traceability of orders and stock levels. - Storage flexibility
The management of the carousel pods as well as the distance between the shelves in the containers can be easily adjusted to adapt to changing product mixes or to cope with seasonal peaks in orders. The distance between the carousels can be adjusted to avoid any obstacles such as support columns or the like. In addition, the position of the electrical control panel can be chosen with a high degree of freedom and the perimeter fence is normally designed to adapt to the installation site.
Modula: The new HC horizontal carousel
Modula has been developing warehouse automation products for many years and has recently launched the new HC horizontal carousel on the market precisely to meet the need for automated storage systems even in premises with low ceilings.
Like the Modula vertical storage solutions, the automatic carousel system also provides a 6 to 18 month return on investment (ROI), depending on the size and characteristics of the project.
Want to know more?
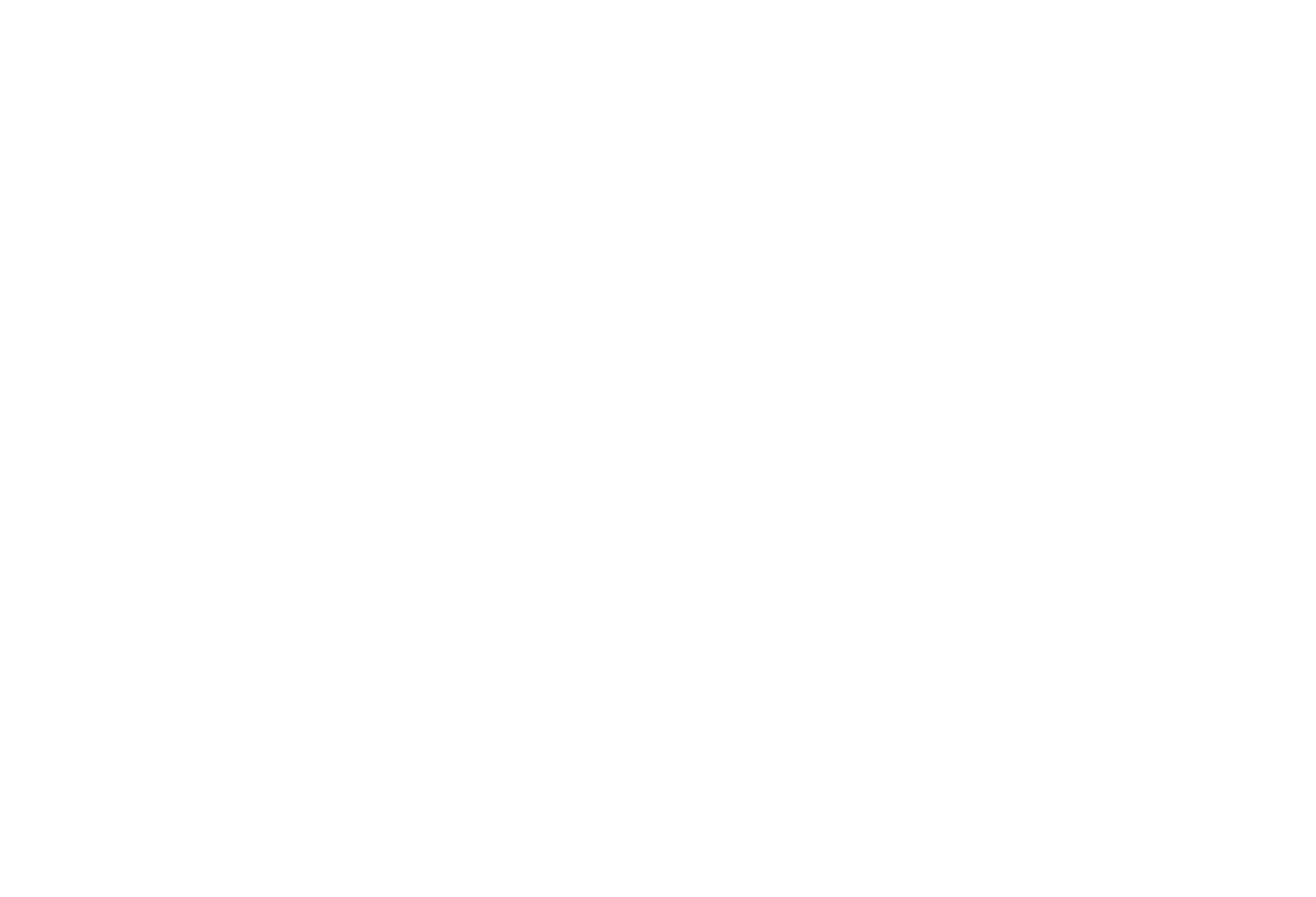