Very often, when talking about Modula WMS, it is difficult to have a clear and accurate idea about how it works, how it is implemented within the logistics flow and, above all, about how many of its functions can be advantageously used in the daily life of a warehouse.
If you’ve never used it before, it’s not easy to identify and quantify the benefits of this powerful yet simple tool.
What exactly is a WMS software application?
Many classify the Warehouse Management System (WMS) as a system for managing placing and picking activities in a warehouse but, as you will see, this definition is too limited.
A WMS can be considered the thinking part of a warehouse, the supervision and control system that facilitates the management and coordination of the various operations taking place within the entire storage area.
In fact, one of the main strengths of a WMS lies in that it is able to interface with other business management systems, on multiple levels of complexity, to respond to requests for action or control over what takes place along the supply chain.
Given this premise, if we think about Modula’s WMS application, initially developed for the management of automatic vertical storage systems, we can instinctively see that it cannot be classified simply as placing and picking management software.
What is Modula WMS used for?
The immediate logistical advantage seen upon installation lies in the possibility of managing each single SKU or product code with great accuracy by connecting it to a specific compartment of the Modula storage system.
A compartment is understood to be a physical space in a given tray, delimited by separators and dividers and intended to contain the materials to be stored.
Thanks to its simple integration, from each of these compartments, the WMS application can manage and retrieve various information related to warehouse inquires such as:
- Ripening/aging date (ripening stage / ready)
- Expiration date
- Information regarding the status of individual SKUs
- Storage status (archived, to be archived)
- Validation status (validated / to be validated)
- Product status (new / used)
Thanks to the WMS system, data management is much more efficient. Each handling event, even of a single item, from a single compartment, is always logged: management status, picking and placing operations, etc.
For anyone working in this sector, having such information seamlessly available through the Warehouse Management System (WMS) is certainly an interesting prospect.
This is possible because the communication between the WMS and the ERP takes place in real time; once the status of an item changes, the information is immediately shared between said systems, thereby updating the status of the relevant SKUs and making such information available to all relevant parties.
The WMS is particularly effective also in the case of structured and complex operations such as inventory or order consolidation.
This tool, combined with different robotic peripherals or accessories, offers the possibility of streamlining operations which, very often, require significant time and human resources.
For example, order consolidation organized by the WMS can also take place on the fly thanks to picking solutions such as the Picking Cart: the items in an order are consolidated while the order itself is being prepared, without intermediate phases.
Myths that need to be debunked about Modula’s WMS: Let’s take a look
To ensure correct and adequate information for those operating in the world of logistics, it is necessary to dispel the main “false myths” related to the Modula WMS software.
- With a single Modula WMS license, it is not possible to manage an entire storage facility.
- The WMS does not allow full control over multiple storage systems located in different company areas.
- WMSs are difficult to integrate with some ERP systems.
- It is not possible to return the infrastructure to the state prior to the installation of the WMS.
- The WMS is not able to manage individual items/SKUs in an accurate and timely manner.
- The WMS is unable to manage inventory as a whole.
- It takes an IT expert or engineer to properly integrate and use the WMS as expected.
With a single Modula WMS license it is not possible to manage an entire storage facility
The first “myth to dispel” concerns the need to obtain a WMS license for each automatic storage system/unit installed.
If and when you decide to have multiple Modula units installed in the same facility, or in the same company but in different locations – for example in the storage area, in the production area, at the point of sale – it is absolutely not necessary to purchase a license for each product.
A single license enables the management of all active Modula storage systems, regardless of their model, size, capacity or individual functions.
In addition, the activation of the WMS can also be very helpful to manage existing traditional manual storage systems.
Modula has taken advantage of all the know-how acquired during the ongoing development of its automatic vertical storage systems to facilitate the management of “traditional” storage systems not equipped with automated solutions.
Of course, traditional storage systems need more manual operations, even when connected to a WMS application.
For example, during picking and placing activities, the logging of relevant data does not take place automatically and this could lead to input errors. In this hybrid case, the operator picking or placing an item must record the event. The Modula WMS will then ensure the proper processing of that information combining it with that coming from the automated Vertical Lift Modules (VLM).
This shows that it is possible to integrate the management of mixed storage systems within a company.
Modula’s automatic vertical storage systems and manual storage systems can become complementary solutions to be used for different functions and located in different parts of the company.
WMSs are difficult to integrate with some ERP systems
Integrating warehouse management software such as Modula WMS into your management systems is much easier than you might imagine.
One of the topics of greatest interest, for those interested in management systems, concerns the methods of implementation and integration of new software with the existing management infrastructure. This is a very relevant aspect because any issue related to the management of operational flows and to any difficulties in the integration phase are always a cause for concern for the IT department of a company.
The good news is that the Modula WMS application, developed over 20 years ago by Modula, has been continuously improved and upgraded over the years.
The team in charge with the WMS has developed solutions that can be seamlessly integrated with basically any management system and ERP.
Regarding the integration and data exchange between Modula automated storage systems and the relevant ERPs, three methods are used, according to the following protocols:
- Data exchange through Web service (Rest API)
- File exchange (xml, csv, text files)
- Data exchange via ODBC (intermediate database)
The choice of the data exchange method may depend on several factors: first of all, on the company’s directives, the pre-existing warehouse management system, familiarity with protocols, as well as on the subjective preferences of the IT staff.
The WMS was developed to have the flexibility to comply with the technical constraints imposed by pre-existing management systems; however, it can be configured with its own logic without any constraints. In the latter case, the exchange of data through web services based on REST API is recommended, as this is a programming interface that can be easily integrated with all modern management systems, even those operating purely online.
It is not possible to return the infrastructure to the state prior to the installation of the WMS
Modula WMS is particularly flexible and adaptable in terms of modifications to its main configuration, even during operation.
For example, regardless of how data exchange occurs – via ODBC, Web service, or through file exchange -, it is always possible to change one’s mind and reset the configuration and exchange interface. There are no constraints, the interface type can be changed at any time. It is really simple to change the communication interface or re-establish the previous modalities. In addition, even in the case of changes to the software settings, no data in the storage system managed by Modula WMS is lost, no activities are deleted, the WMS can be reconfigured by simply changing the protocol type. This safety feature, together with the flexibility of the system itself, makes Modula WMS an extremely reliable and practical solution even in view of future developments. Therefore, it is possible to adapt the exchange protocols or to restore the previous protocol at any time.
The WMS is not able to manage individual items/SKUs in an accurate and timely manner
Another aspect to discuss concerns the management of individual items/SKUs.
The alleged lack of adaptability on the part of the WMS software in the management of batches or in the creation of customized management protocols is absolutely unfounded.
A Modula storage system can manage each item with absolute flexibility as it communicates with the software application that enables the simultaneous management of thousands of SKUs. Each SKU can be managed with different FIFO processes, according to the quantities and with customized units of measurement. For example, an item can be handled in packs of 6 or 12 pieces or more and counted in different units of measurement depending on the specific needs. In this way, it is also possible to efficiently control and manage products such as water or food, which can be counted as pallet units or individual pieces or packages depending on the area of the storage system or stock and picking needs.
The WMS is unable to manage inventory as a whole
Speaking of storage system management, it is impossible to overlook the importance of having reliable information about inventory, a critical task that must be performed with accuracy. As seen in the previous paragraphs, the integration of the WMS software application is the best solution to keep stock under control and have a good cataloguing system.
With the Modula WMS application, the company can be certain of having accurate and up to date inventory available in real time; in fact, it is possible to know the position, status and quantity of any of the material in the storage system at any moment. In addition, all operations as well as all picking and placing data can be consulted in a few simple steps. In a nutshell, the Modula WMS can provide an accurate and organized report, based on individual SKUs or entire groups of locations, required by the ERP with a list of SKUs to be inventoried. Even if the operator wants to carry out a manual check, all they have to do is make the request for information through the console. Everything happens instantly: the Modula storage system interprets the request for information as if it were a simple order. The operator will receive the requested tray at the bay and will be able to physically count the items contained in it, in order to compare the quantities with those resulting in the system. In summary, the Modula WMS application can provide an instant view of the contents of automatic storage systems upon request: in this way it is always possible to know the conditions and quantities of a given material together with the data concerning what was picked or placed (when and by whom).
It takes an IT expert or engineer to properly integrate and use the WMS as expected
The Modula WMS was developed to ensure simple deployment, operation and user experience: you do not need special computer skills to consult it or understand how it works.
The user interface was designed to ensure ease of use and, as a result, the learning process is very fast. After importing the item master data and configuring the locations, the WMS interface panel provides instant and up to date information on all relevant storage systems in real time. In fact, in addition to the standard WMS reporting, operators can have extra detailed information from all the Modula machines under its control, having for example an up-to-date idea of how much space could be further optimized, how much volume is actually used, how many operations have been carried out, how many errors have been recorded, and much more.
As explained above, another great advantage of using this software application is the possibility of setting the degree and depth of interaction with corporate IT structures. The integration with the ERP system would allow, for example, the automation of the entire process of order flows together with all relevant and related logging information. In conclusion, the Modula WMS application is a highly efficient and reliable system for the management of warehousing activities, which has proven to adapt to the needs of the most diverse companies. As we have seen, some “false myths” that circulate around this software application are based on mistaken or incomplete information that does not take into account its elevated capacity for customization and integration. Among the many Modula WMS features, the real-time monitoring of logistics processes and the automated inventory management, in particular, certainly add value to any company. Ultimately, the Modula WMS significantly improves the efficiency, productivity, and competitiveness of any warehouse, overcoming any misconceptions and “false myths.”
Want to know more?
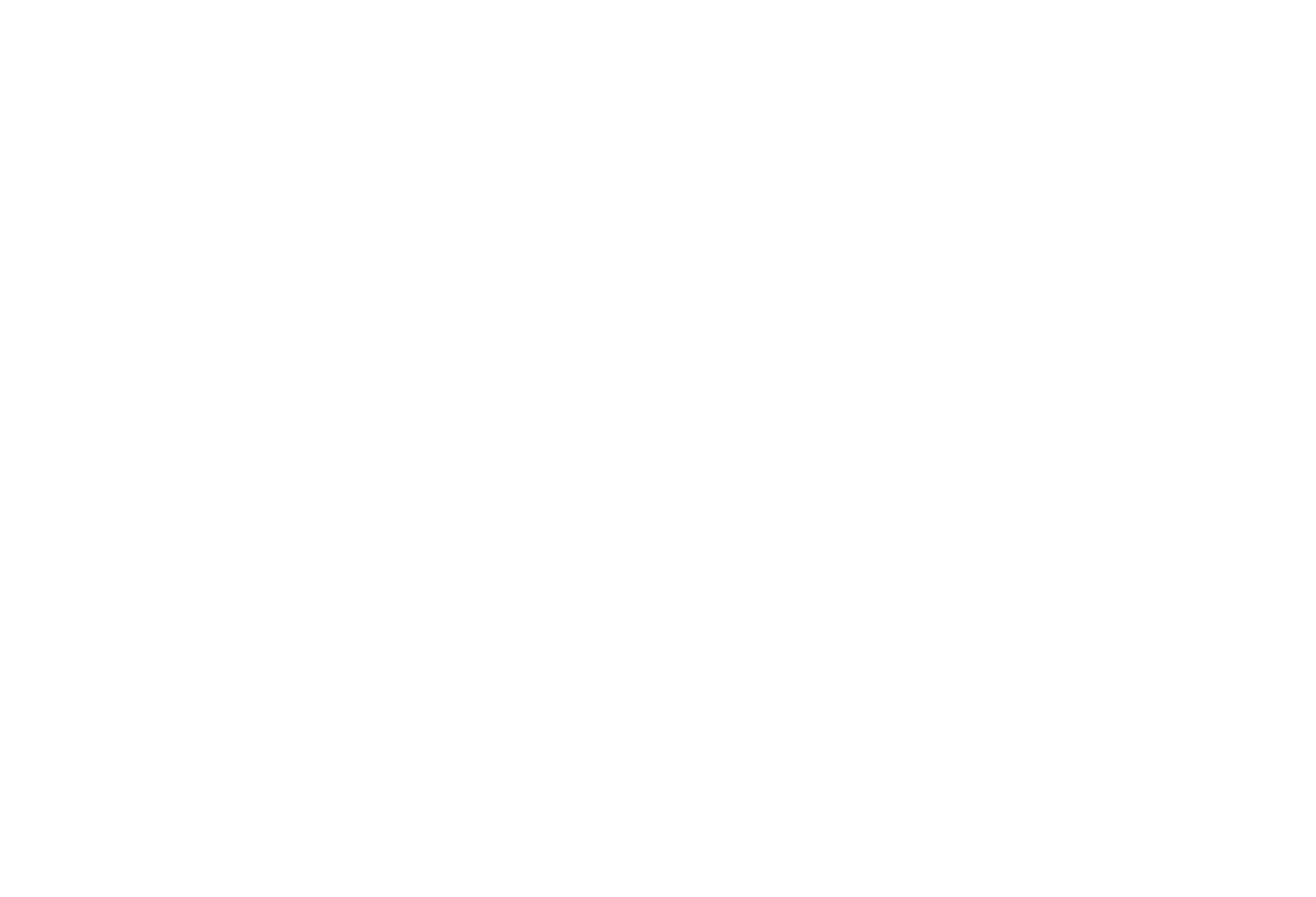