As part of modern warehouse management, the adoption of automatic solutions such as Modula vertical lift modules has become essential to improve operational efficiency, optimise available space, speed up picking, eliminate errors and work in a more ergonomic manner.
To ensure successful investments, it is essential for us at Modula to guarantee access to specialist advice, not only during the use of the product, but most of all during the purchasing process.
This article explains how an attentive and prepared consulting service, from the pre-sales phase onwards, can be crucial in the planning of warehouse reorganisation.
The everyday experience of our salespeople – who work closely with a wide range of clients and partners – has enabled us to gather knowledge and insights to guide you towards the most informed and suitable choice for your requirements.
Modula’s roadmap for customised warehouse solutions
Exploring the path that leads to the adoption of Modula automation solutions, we highlight the key steps: from the detailed analysis of the client’s specific needs to the creation of tailor-made solutions that radically transform warehouse management.
1. Understanding client requirements
The core of our consulting is based on attentive analysis of the specific characteristics of each client. We realise that every company is distinctive for its storage requirements, speed of access to products and order management. In-depth interviews and meticulous investigation of business processes enable us to trace a path to the inclusion of the Modula solutions that best meet the requirements identified.
The versatility of Modula warehouses goes far beyond conventional use in areas dedicated to warehousing, shipping or logistics. The applications extend to production contexts such as:
- production buffers: solution chosen by Florim, a manufacturer of porcelain stoneware tiles
- innovative solutions for transporting surgical instruments in hospital environments, as illustrated in the case of Xi’an Hospital;
- efficient archiving systems for companies, such as Netseals, with a high volume of documentation.
The flexibility and ease of use of our systems are manifested in every scenario, demonstrating how a Modula automated warehouse can be a valuable ally in different areas of a company.
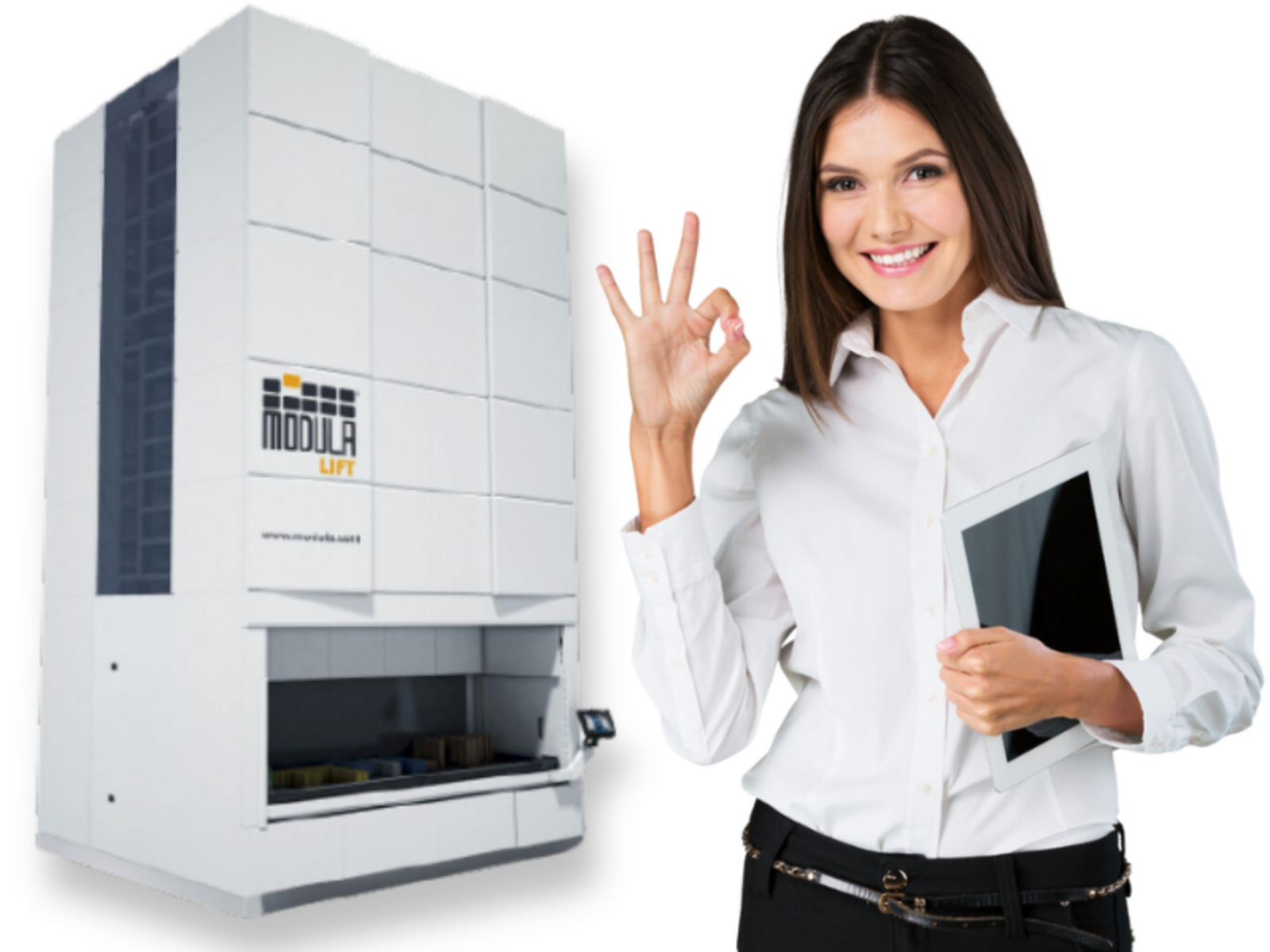
Want to find out more about other Modula success stories?
Discover the companies that have decided to put their trust in Modula solutions to optimise their warehouse management.
2. Custom Modula automatic warehouse design
The tailor-made design of a Modula vertical lift module is the result of a continuous and in-depth dialogue with the client. Close collaboration is one of our priorities to ensure that all aspects from optimal arrangement and tray configuration to their mapping and the most intricate customisations contribute to creating a smooth workflow and to maximising the available space.
At this stage, support from a consultant is important to understand which warehouse model to choose: whether to adopt an extremely compact and shallow Modula Slim compared to a Modula Lift, which ranges from 1500 to 4100 mm in width and reaches 16 metres in height, depends on differing situations and management approaches.
Special solutions are also available, such as temperature-controlled warehouses – Modula Climate Control and Modula Clean Room – or controlled access warehouses such as Modula Next. Integration with AMR-type automatic handling systems, picking solutions or cobots are also possible.
Our experience translates into advice to help navigate these options, offering a fully tailor-made solution. It is the ability to predict that sets us apart: strategic positioning of the first Modula to make the most of every available centimetre, already bearing in mind future developments and increases in capacity.
Our solutions can even be used to face up to the toughest challenges, such as outdoor installations in insulated environments, made possible by special panels that provide exterior protection without sacrificing internal space. This flexibility of application, guided by attentive and targeted consulting, has proved decisive in multiple sectors, ensuring that every Modula project is not only a solution, but a transformation of the way of working.
3. Implementation & training
Modula’s consulting does not end with the custom design of an automated warehouse. We also deal with the implementation and in-depth staff training, ensuring that each component of the Modula automatic storage system integrates perfectly with the company’s existing operational processes.
4. Constant monitoring & updates
Constant monitoring services to ensure the system is up and running are only the beginning of a long-term commitment to the client. We are ready to take prompt action to resolve any issues and keep your system up to date at all times with the latest software, through regular updates of the Modula WMS. This cycle of support and constant improvement testifies to our commitment not only to solving current challenges, but also to preparing you for future opportunities.
Transforming warehouse management to gain a competitive advantage
To consolidate the statements above, it is useful to summarise the crucial phases through certain key points that mark the path to efficiency and warehouse optimisation with Modula.
- Start with a comparative analysis: contact the main players in the industry for a direct comparison of the technologies available, to set a benchmark to guide your choice.
- Request an initial inspection: request a visit from a Modula sales representative for an initial consideration of your specific needs and requirements.
- Schedule a strategic meeting: arrange a meeting at the potential warehouse location to discuss the size, the space available and an optimal layout.
- Decide on storage requirements: work with the Modula sales representative to map the specific storage requirements in the various trays, as well as the desired picking frequency.
- Take advice on choice of system: get advice from the sales representative on the choice of the most suitable model, on the options to be added according to requirements and jointly plan tray layout to decide on the compartments and spaces.
- Anticipate the future: once the project has been outlined, consider future developments and potential changes to position the Modula system in the most advantageous way, while maintaining flexibility for any relocations or adjustments.
- Set up logistics and training: decide on the system delivery and installation times, ensuring you organise adequate staff training in the effective use of the Modula, in terms of both hardware and software.
To sum up, opting for our consulting service means deciding to elevate the efficiency of your warehouse. The synergy between Modula and advanced technologies, such as anthropomorphic robots, AGVs and stacker cranes, testifies to our ability not only to respond but to anticipate the needs of the market, by offering innovative solutions.
The example of the Italian company GAI, a leader in the production of bottling lines, perfectly embodies this philosophy. In this case, over 20 Modula units operate in harmony with stacker cranes and AGV robots, masterfully integrated through the company’s management system and Modula WMS software. The result of thorough customisation that responds to the client’s specific requests, from the use of external stainless-steel bays to prevent contamination to the adaptation of Modula Lift with DD trays for the storage of large sheets and plexiglass, this integration reflects the very essence of our commitment: to turn every challenge into an opportunity for growth and innovation.
For us at Modula, all our clients can rely on a range of solutions designed to anticipate future needs, ensuring that every investment is not only safe but also a driver of progress and success.
Want to know more?
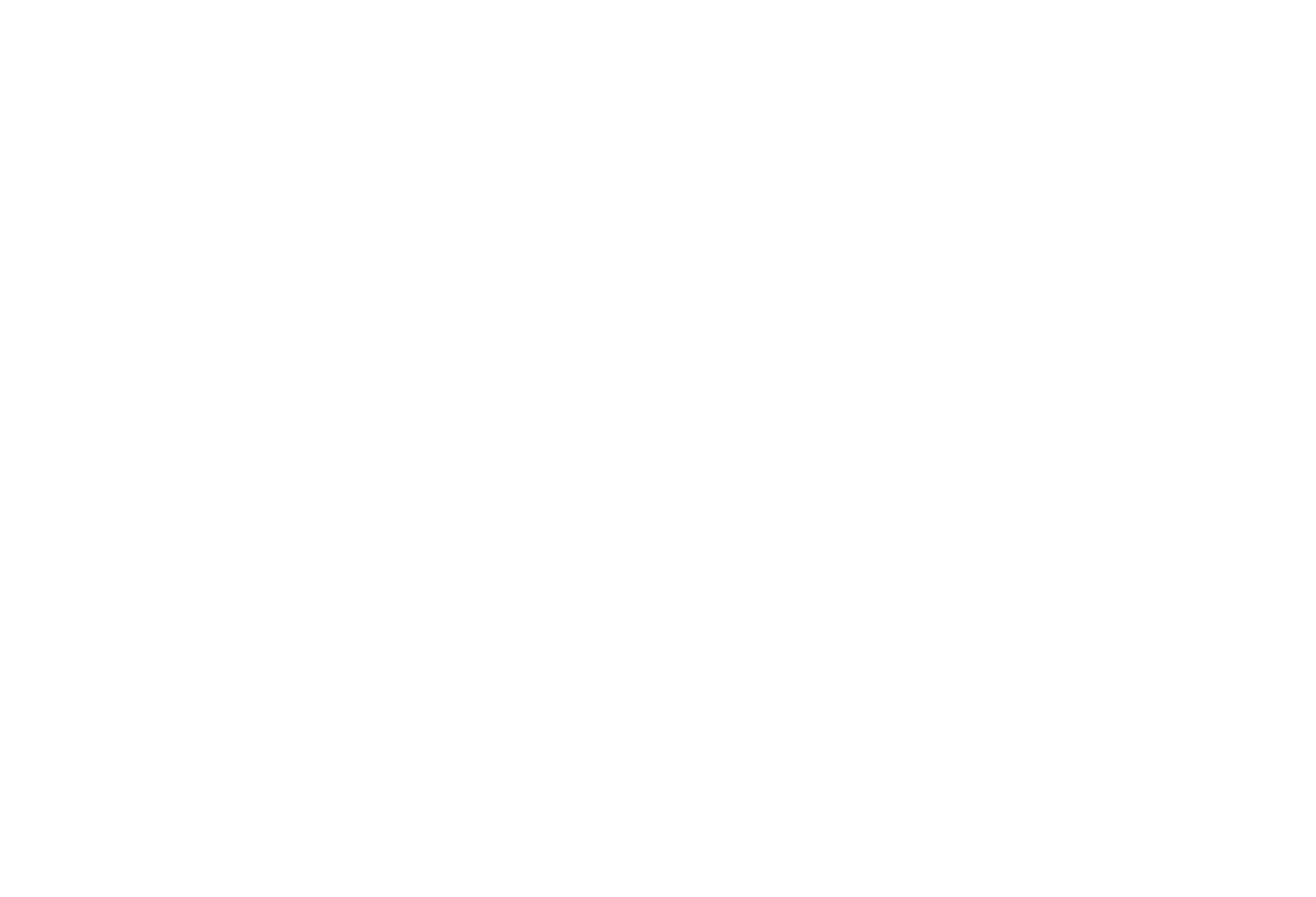