Choosing to invest in an automatic warehouse is generally motivated by the desire to improve your warehouse’s organisation and management, increase its performance and how it serves you, by minimising errors and optimising costs.
The automatic vertical tray warehouse is the automated solution which has really taken hold in the last few years in the world of intra-logistics. As opposed to automated plant systems, these can be classified as machines that you can include in your logistics process without requiring radical changes to your organisational planning, but which bring substantial advantages in terms of efficiency and effectiveness.
Despite being widespread, when people talk about automatic vertical warehouses an aura of doubt and uncertainty persists which is hindering their integration into production processes. This leads business owners and supply chain managers to prefer traditional, static solutions of warehouse organisation. Let’s dispel some of these myths together.
1. Installing an automatic vertical warehouse is very complex and requires production to be stopped for a prolonged period
One condition of successful business is guaranteeing a constant production throughput able to satisfy customer requirements. Reorganising a part of the production process and supply chain as important as the warehouse therefore causes a great deal of worry. However, the time needed to install an automatic vertical warehouse is absolutely not any more than that required to install traditional static solutions.
The further advantage is the ease of use and the small amount of space required for its installation. An automatic vertical warehouse actually requires only a small amount of space for its installation, leaving the rest of the warehouse to continue working as it is not affected by the installation. Loading of merchandise into the machine can also be concluded in a short space of time thanks to the simplicity afforded by the tray loading system. It is therefore quite clear that reorganising a static warehouse requires more time and space than the introduction of automatic vertical warehouses. This means that these are obviously the better solution.
Risulta evidente dunque che riorganizzare un magazzino statico richiede un dispendio di tempo e spazio maggiore rispetto all’introduzione di magazzini verticali automatici e che questi ultimi risultano di conseguenza la soluzione migliore.
2. An automatic vertical warehouse is not flexible enough and cannot be used to store merchandise of different sizes
A second and frequently repeated myth is that you can really only store merchandise of similar sizes. As opposed to automatic warehouses which use stacker cranes, the use of automatic vertical tray warehouses does not require goods to be organised into specific Storage Units (usually second-level SUs, like pallets). The vertical warehouse’s trays alone can be used to store goods. The software allows you to keep track of which products are in which trays, their quantities and the weight of the entire tray. Flexibility is further guaranteed by the automatic warehouse’s ability to manage height clearances between trays completely autonomously, so that products of different sizes and weights can be stored. This is commonly known in the jargon as Dynamic Tray Height Storage, and guarantees that all available vertical space is optimised. All of this makes automatic vertical tray warehouses the most flexible storage solutions currently on the market.
3. Automatic vertical tray warehouses are not reliable as they break down regularly and this makes retrieving stored products very difficult
This is perhaps the most common myth discouraging investment in automatic vertical tray warehouses. This stems from the fear that a machine can actually slow production down due to stoppages, and that this investment may only bring further problems rather than simplifying work.
Few actually realise that an automatic tray warehouse can also be operated manually and so, in the event of a breakdown, the elevator can be raised or lowered to reveal the required tray. This means that picking of products can continue through direct manipulation of the mechanical components. These machines are therefore very reliable. If however you still don’t feel confident making this investment, choose a supplier who provides effective telephone support to help you solve small problems without needing an engineer to attend your site. They should also provide an extensive support network and if possible also periodic preventive assistance to reduce the probability of faults to a minimum.
4. Automatic vertical warehouses are not compatible with our existing management software
This is myth number 4. Nowadays you can request a solution which interfaces fully with existing business management or WMS software and therefore continue to keep track of all picking and loading operations.
5. Automatic vertical warehouses require a high level of investment and provide a Return On Investment (ROI) only in the long term
Many people are surprised to learn how affordable an investment an automatic vertical warehouse actually is. In most cases, when people think of storage and picking automation systems, they imagine warehouses full of stacker cranes or Miniloads. These solutions require large-scale investments of both time and money. This is not the case with automatic vertical tray warehouses. Each machine can be acquired individually which means that you don’t have to completely remodel how your warehouse is organised. You can bring in automation in small steps. Moreover, as we’ve said before, these systems are quick to install and reduce losses from production downtime to almost nil. The price of a single machine depends on its size, however on average a machine comes in at around €30,000. This makes automatic vertical warehouses the best solution for virtually any business or product as it can guarantee a ROI even in the short term.
Furthermore, as announced in the current Italian State Budget for 2017, you can claim Ultra Depreciation of 250% for the hardware and Super Depreciation of 140% for the software as this is technology which fully meets the updated criteria announced in the budget. This is also equipment which relates to business digitisation and development projects envisaged in the so-called Industria 4.0 industrial strategy.
6. You need qualified staff to manage an automatic vertical warehouse
Besides being very flexible, this type of warehouse is extremely simple to use. Only minimal skill levels are required of personnel using the machine. In terms of the time it takes to learn how to use it, this is less than the time it would take a new member of staff to mentally map out the precise location of all the products stored in the warehouse. This type of automatic warehouse also allows you to guarantee a much higher degree of safety compared to traditional solutions which require your labour force to perform dangerous movements and operations in order to retrieve products in the warehouse. Choosing an automatic vertical warehouse becomes an advantage for the entire business and for its staff.
An automatic vertical warehouse represents an advanced solution compared to traditional types, but this doesn’t mean it is difficult to use. On the contrary, it will prove itself to be flexible, easy to acquire both financially and in terms of time, and guarantees an obvious ROI even in the short term.
8 types of waste that Vertical Lift Modules can eliminate
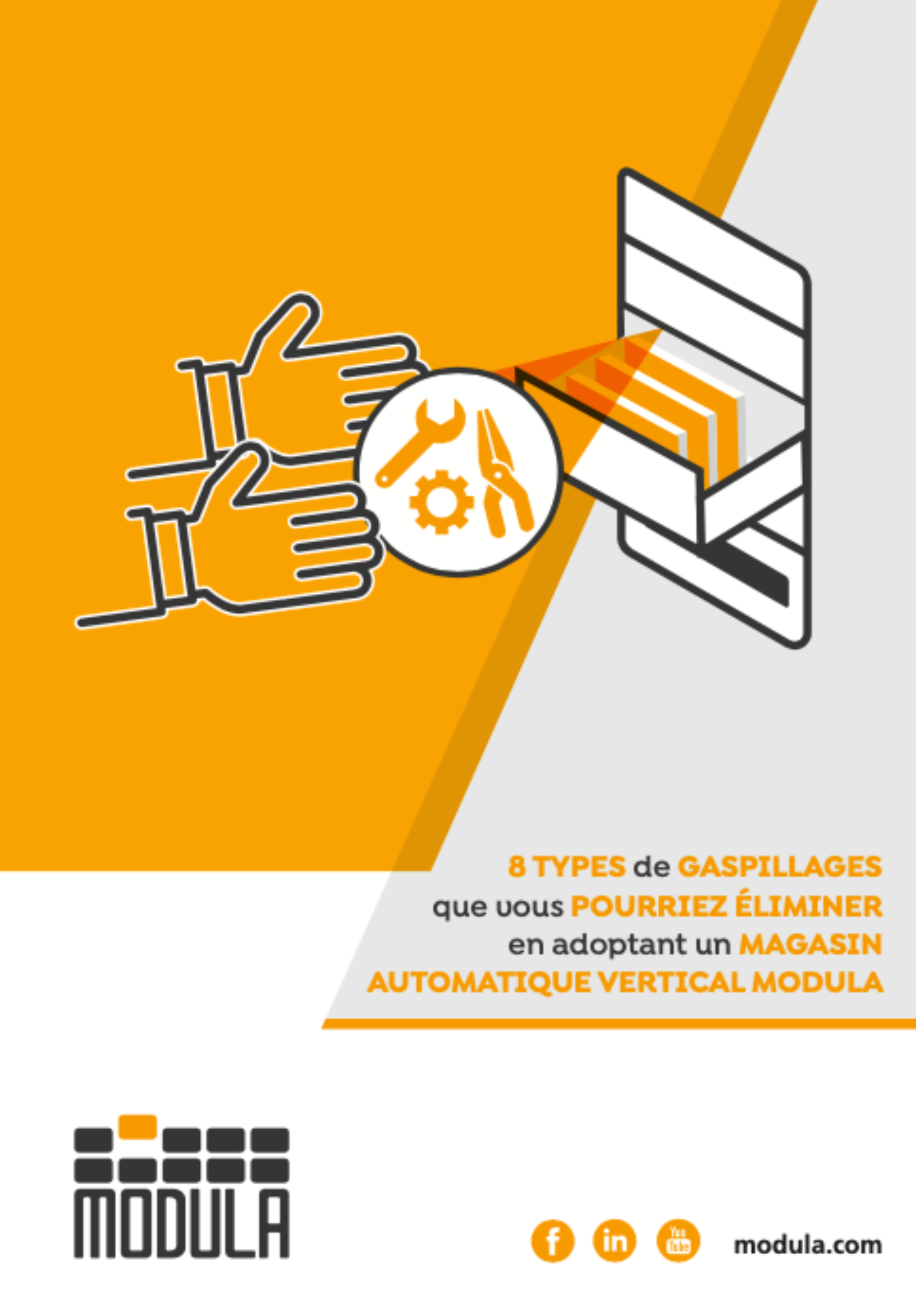