Warehouse picking is one of the most important phases in order preparation: it involves picking the specific items of an order and then preparing them for shipment.
It is a process that requires both high-tech equipment and optimal organization of the manual work to ensure accuracy in the preparation and fulfillment of orders. Indeed, any inefficiency in this phase translates into a slowdown of the entire order preparation process.
For this reason, technologies and picking solutions aimed at increasing warehouse productivity have developed over time. The choice of the order preparation method is, in fact, strategic both for proper warehouse management and for company performance.
Among the systems developed for the picking phase, batch picking is one of the most efficient. Let’s take a look at this picking strategy, exploring the technologies and sectors in which this method is more successful.
What is batch picking and how does it work?
Batch picking is one of the person-to-goods methods by which items are picked for order preparation. In this method, the operator picks multiple items of the same type at the same time (batches) and then sorts them into the different orders.
Once finished, the batch of orders moves to another storage area where additional items will be picked, until the orders are complete.
The goal of batch picking is to reduce the number of trips personnel must make to the picking areas, thus increasing operational efficiency.
What are the main characteristics of batch picking?
The batch picking method can be implemented with different levels of automation, depending on the type of warehouse. In general, the more the warehouse is managed automatically, the more efficient batch picking will be, with a margin of error close to zero.
Batch picking can generally be divided into 4 phases:
- A picking list is generated, that is, a document with the items to be shipped, the quantities for each item, and their storage position in the warehouse. The picking list may be on paper, in smaller warehouses, but more often this operation is managed digitally.
- Orders are grouped – automatically and in the most efficient way if there is an order management system or WMS – so as to include the same items for each batch of orders.
- The picking lists, ordered according to the batch picking route suggested by the WMS, are assigned to the picking personnel. If the warehouse does not have an automatic management system, it is also necessary to determine the recommended route.
- The warehouse operator, following the picking list, picks the items according to the batch picking route, until completing the batch of orders assigned to them, and at that point, the order is passed to the personnel in charge of packing.
Thus, adopting automatic warehouse management systems and implementing cutting-edge technologies exponentially enhances the efficiency of batch picking.
What technologies are needed to implement the batch picking method?
To efficiently implement batch picking, ad hoc software can be used to reduce the distances to be covered and the repetition of movements. Warehouse management systems (WMS) are modular solutions for managing flows in warehouses which, by interfacing with other devices, can also simplify batch picking functions.
Modula picking aids for order preparation are:
- Put to Light – The system with a display that guides the operator to the positions in which to put the items of each order. For each item, the display visually indicates the container and quantity of each SKU to be inserted. Thanks to the WMS, the Put to Light system can also be implemented for the batch picking method.
- Picking Station – Steel structures with shelves for containers, which can be integrated in traditional warehouses with manual transport or in modern warehouses with automated transport. These are the structures on which the Put to Light device works best.
- Picking Carts – Unlike fixed Picking Stations, Picking Carts are maneuverable carts with pivoting wheels. They are equipped with shelves for containers and Put to Light displays for the easy identification of the container in which the picked item must be placed. Picking Carts for batch picking may be used in warehouses with traditional shelving as well as in automatic vertical storage systems.
When it is advantageous to implement the batch picking method?
The batch picking method is particularly effective and optimized when:
- The items to be picked are homogeneous and small in size – In this way the operator can easily prepare batches of orders by placing them in the picking cart.
- The company has many orders to process – Order preparation and retrieval times for the items involved are reduced, which results in less warehouse congestion.
- Orders have just a few and homogeneous SKUs – In this way the picking and sorting process can be carried out together and simultaneously, with a further reduction of picking errors.
The advantages of batch picking in order preparation are therefore:
- Reduction of the number of trips
- Reduction of labor and related costs
- Reduction of fatigue
- Increased productivity
In addition, with the Mobile Picking APP, compatible with Android systems, it is possible to communicate directly with the Modula WMS which guides the picker, thus increasing efficiency.
Which sectors use batch picking the most?
Batch picking, as seen above, offers undisputable advantages for the management of warehouses where the number of items is not excessively large and the orders are rather homogeneous. This makes it the preferred picking strategy for e-commerce – regardless of the sector – where order preparation speed and accuracy must be at the highest levels.
To learn more about how to optimize warehouse picking operations, download our Manual, a useful free guide to maximize the efficiency of one of the most strategic phases in order management and fulfillment.
The advantages of a Modula automatic vertical storage system
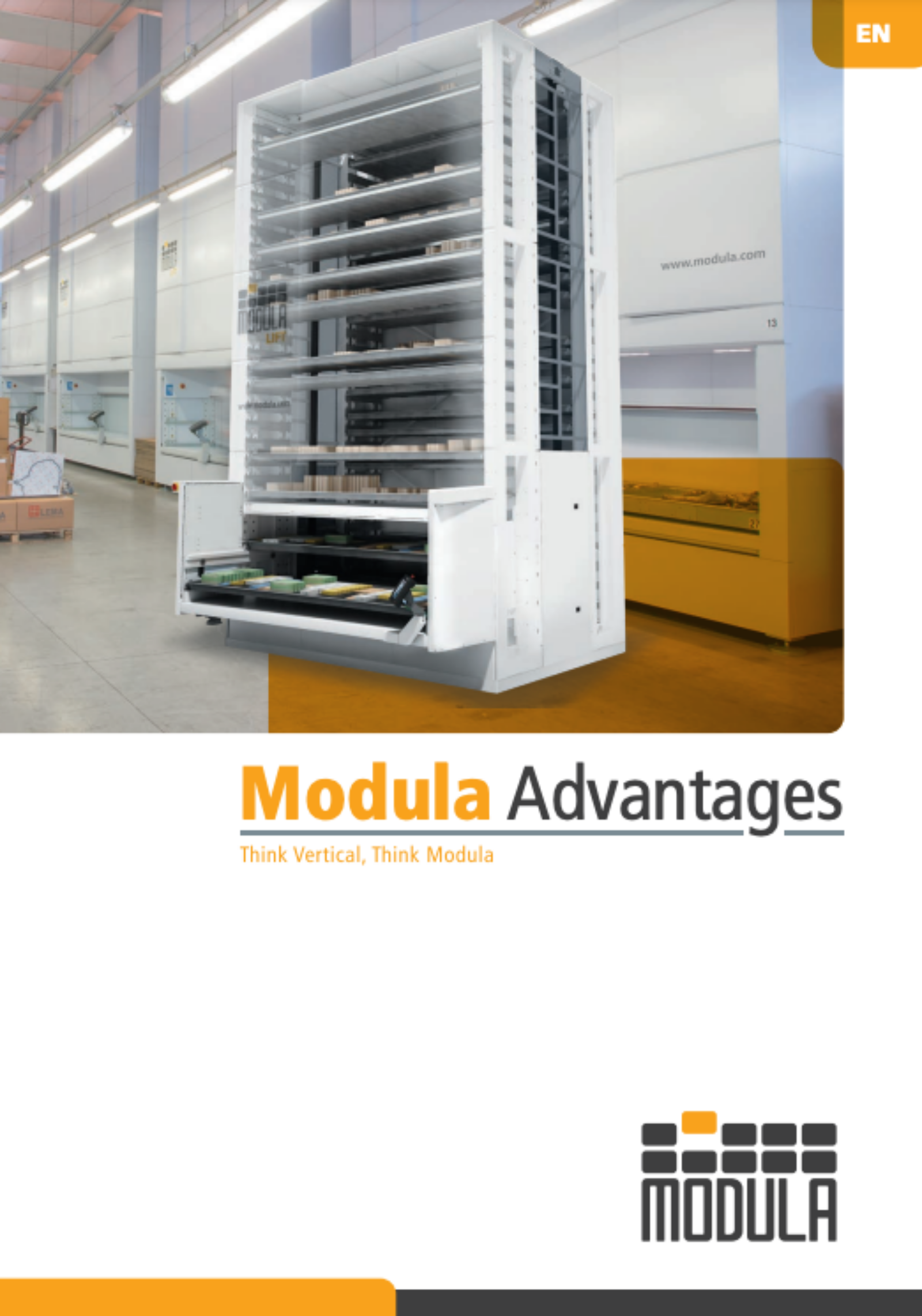