When we talk about cold supply chain logistics, we mean a temperature-controlled supply chain that includes the following systems:
- Production
- Storage
- Distribution
Each of these systems must be supported by equipment suited to keep a constant temperature within the required range so that the materials or products processed and distributed do not undergo contamination or deterioration.
The cold chain is therefore one of the most complex – and expensive – logistics management processes and is used in sectors dealing with heat sensitive products, such as the food, pharmaceuticals, electronics, floriculture, and leather sectors.
Due to the nature of the products, the specific criticalities in the management of the cold chain logistics make it different from the traditional supply chain. One example is vaccines, as they often require a very narrow temperature range throughout the supply chain, that is, from production to the final user. Failure to maintain the temperature within these narrow ranges even for a short time along the chain means affecting safety and efficiency and therefore making the vaccines unusable.
1) High costs for temperature control
Some sectors in which cold supply chain logistics is used have a direct impact on people’s health (for example, the agri-food and pharmaceuticals sectors), and for this reason temperature control requirements are stringent and regulated for all phases of the cold chain.
The reference framework in Europe is EC Regulation 37/2005, which requires temperatures to be measured and recorded at regular intervals on means of transport and storage sites. This means that both the means of transport and the warehouses must have suitable instruments and equipment to guarantee the required temperature as well as measure it over time.
Examples of the specific equipment and significant investments – up to 5 times higher than those required for transporting and storing dry products – needed for cold logistics are cold rooms, building insulation, temperature control sensors, reefer transport. The energy costs related to the refrigeration systems must also be considered.
2) Risk of contamination and deterioration
The contamination or deterioration of products that require a controlled temperature has enormous economic implications for a company. A case in point is the food sector, where the cold chain is increasingly adopted due to the massive presence of large-scale retailing and e-commerce. Foodstuffs are highly perishable and fungi, bacteria and microbial growth can easily develop if they are not properly managed and handled. Logistics must also comply with the HACCP (Hazard Analysis and Critical Control Points) rules.
The costs related to the deterioration of materials are both direct and indirect and can be generated throughout the supply chain. These costs are higher in the storage phase, the only link in the logistics chain where temperature is reduced.
When products are contaminated or perish, the consequences are:
- Waste management costs
- Higher quality control costs
- Replenishment costs
Indirect costs, instead, are related to:
- Loss of reputation and trust
- Loss of market share
- Possible disputes due to claims for damages
To reduce the risk of contamination and degradation of products – and thus avoid the associated costs mentioned above – it is critical to implement all temperature control measures and use suitable technological solutions capable of maintaining the cold chain.
3) Picking Times
Strictly related to the safety risks illustrated above, picking times in cold logistics must be reduced to a minimum to ensure the integrity of the products being handled. Picking is indeed a key process as the product or goods are left out of the temperature-controlled environment and this lapse of time must be minimized to ensure safety and integrity.
When designing a warehouse management system for the storage of perishable products, it is essential to implement picking strategies and to use automation tools, so that the products remain outside the refrigerated environment for the shortest possible time.
Solutions to limit the costs of the cool chain
If the costs related to cold logistics and to its improper management are very high, it is also true that it is possible to adopt processes and technological solutions suited to significantly limit them as well as all related risks while at the same time optimizing organization.
These solutions can be used in the following phases of the supply chain:
- Production
- Storage
- Loading of goods
- Transport
- Unloading at distribution hubs or Points of Sale
The last phase, that is, picking, storage, and transport to the final consumer, remains outside the company’s control, unless it is e-commerce.
Automated picking
In addition to being a critical phase for safety, picking is also a process in which operators cannot always be involved (as is the case, for example, of frozen product storage, with temperatures as low as -30 degrees Celsius).
In order to prevent thermal shocks and degradation, modern cold logistics centers use anthropomorphic robots to automate picking. The goods-to-person method is therefore adopted, also taking advantage of the more recent voice picking technology which allows operators to communicate with the supply chain equipment and systems using a headset.
Faster picking and the ability of anthropomorphic robots to automatically detect product conditions translate into significant economic savings.
Automatic vertical temperature-controlled storage systems
Cooling a warehouse is expensive, even in terms of energy. For this reason, it is good practice to take advantage of the available surface area as much as possible in order to reduce energy costs.
The solution to this problem is represented by vertical storage systems, with which it is possible to save up to 90% of the available warehouse space. Modula Lift Climate Control automatic storage systems also ensure temperature control in a range of +2 to +25 degrees Celsius, combining the benefits of a vertical storage system with engineering that guarantees the temperatures and humidity levels necessary for the safe storage of products.
An automatic storage system also reduces the costs associated with temperature dispersion, thanks to the automation of picking and placing operations.
Automatic handling solutions in deep freezer cells
In temperature-controlled storage systems, where storage temperatures are low, automatic handling systems which reduce the time spent by operators in these areas are ever more common. One example are pallet stacker cranes and pallet shuttles, which are automatically and remotely controlled. The result is improved operational efficiency and speed.
AMR vehicles, robots and all handling systems operating in temperature-controlled warehouses or deep freezers have different characteristics. The special temperature and humidity conditions can actually affect operation and combine in such a way as to become dangerous.
The lower costs, in this case, are always due to reduced dispersion of energy, decreased exposure of stored products to possible contaminants, and protection of the health of operators.
Cold chain monitoring with sensors and IoT solutions
All the aforementioned solutions are based on the most modern sensor systems for the determination of temperature, position and size, as well as on IoT solutions for analyzing and assessing the data collected. Therefore, the Internet of Things and the sensors help to ensure a constant temperature along the cold chain and to prevent energy wastes.
Thus, with demand for this kind of service currently growing on the market, it is possible to take full advantage of these technological opportunities to maintain the cold chain and improve its management. Think of e-grocery or the pharmaceutical sector, where the demand for products that need controlled temperatures increases from year to year.
The companies operating in these sectors must therefore reorganize their warehouses, both to meet the new requirements for the proper management of goods and to reduce costs while at the same time improving the efficiency of their logistics system.
8 types of waste that Vertical Lift Modules can eliminate
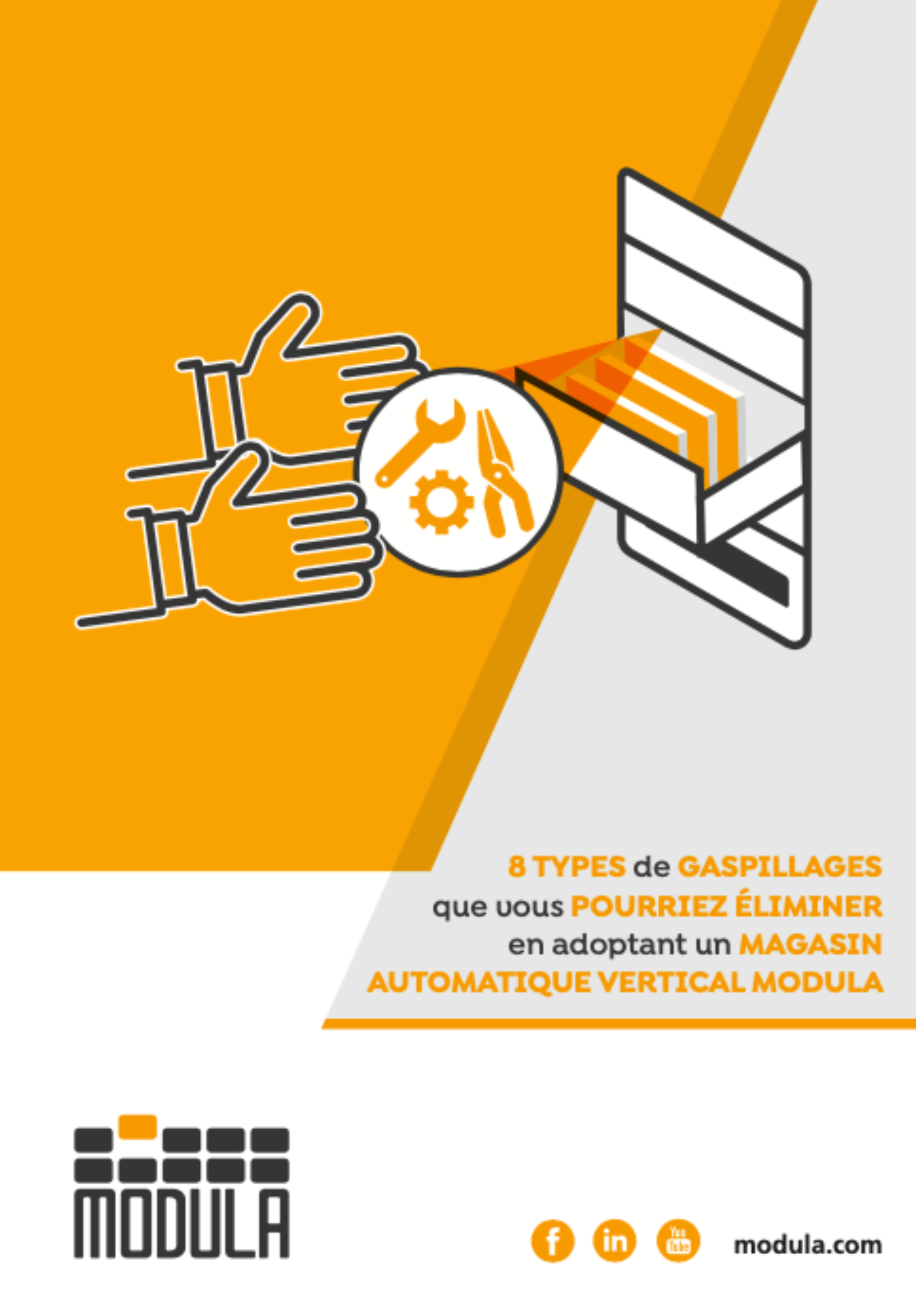