The success stories of Cippone & Di Bitetto, Plub, Perufarma, and Farmaenlace
In the distribution sector, operational efficiency is essential to staying competitive. One of the key factors for achieving this is warehouse automation. But what are the common logistical challenges faced by distribution companies? How has the sector evolved in recent years, and what are the future projections? What strategies can be implemented to optimise warehouse management?
Common challenges faced by distribution warehouses
Distribution companies play a crucial role in moving products from manufacturers to retailers or directly to end customers. Their primary objective is to manage the entire logistics flow efficiently, ensuring that products are available at the right time, in the right place, and in the right quantities. Their ultimate goal is their clients’ satisfaction, which is achieved by balancing cost management, meeting delivery deadlines, and prioritising sustainability.
One of the main challenges in distribution is space and inventory management. A disorganised warehouse can significantly slow down operations, while poor stock planning can lead to various inefficiencies, from capital being tied up and wasted space, to stock shortages and inadequate inventory management.
Another major challenge is ensuring fast deliveries. Customers expect swift order processing with maximum precision. When order picking is managed manually, the risk of mistakes increases, leading to costly returns and reverse logistics expenses.
Warehouse safety is also a critical concern, especially in strictly regulated industries like the pharmaceutical and food sectors, where rigorous storage and transportation standards must be respected. Moreover, the risks associated with manual product handling and warehouse management can also increase the likelihood of workplace accidents.
To address these challenges, many companies are investing in advanced storage solutions such as automated vertical warehouses and warehouse management systems (WMS), which provide for real-time stock monitoring.
Growth and future outlook of the distribution sector
The distribution sector has experienced remarkable growth in recent years. The industrial distribution market is projected to reach USD 10.95 trillion by 2030, with a compound annual growth rate (CAGR) of 4.56% from 2025 to 2030.
Notably, the e-commerce logistics market in Latin America is undergoing rapid expansion. It is expected to grow from USD 6.28 billion in 2025 to USD 10.25 billion by 2030, reflecting a CAGR of 10.30% over the same period.
In order to better understand the actual impact of automation in distribution logistics, we will examine the experiences of several companies that have chosen Modula solutions to enhance their warehouse operations. Companies like Cippone & Di Bitetto, Plub, Perufarma, and Farmaenlace have successfully tackled industry challenges, from space optimisation and efficient picking, to accelerating operations, all while maintaining elevated safety standards. By implementing automatic vertical warehouses, these companies have significantly improved their productivity and accuracy, while optimising their processes.
How did these companies optimise their operations? How did they overcome their supply chain challenges?
Perufarma
Founded in 1971, Perufarma is now one of Peru’s leading distributors of consumer goods, alcohol, and pharmaceuticals. Its distribution centre serves a complex network, including national warehouses, supermarkets, and e-commerce channels, requiring highly intricate logistics.
More than 50% of the company’s orders involve unit picking, a traditionally labour-intensive and time-consuming process. To streamline its operations, Perufarma opted for Modula’s warehouse automation solutions. The company installed 3 Modula Lift ML50D units, each 8,100 mm high, equipped with options such as the Put to Light system with 48 locations and an alphanumeric LED bar, which guide operators through the picking process, improving both accuracy and efficiency. The installation of vertical warehouses has revolutionised the company’s logistics management. Picking operations are now three times faster than traditional methods, and can be handled by a single operator, reducing travel time and significantly increasing efficiency. The workflow has become smoother and more productive thanks to the intelligent arrangement of products and the reduction in errors.
The automation solutions have not only increased the operational speed, but have also optimised the available space and improved ergonomics, making the work safer and more comfortable for the operators.
Cippone & Di Bitetto
Cippone & Di Bitetto, a leading company in food and beverage distribution for the HORECA sector in southern Italy, has made logistics the cornerstone of its operational efficiency. With a rapid delivery model (orders placed by 8 p.m. are delivered the next morning) the company required a warehouse capable of sustaining an intense and continuous workflow, particularly for night-time picking operations.
The solution came with the adoption of 4 Modula Lift ML75D units, each equipped with a laser pointer, allowing for the recovery of over 400 metres of storage space. Thanks to this technology, class B and C products, which have lower sales volumes, are stored efficiently, enabling operators to precisely pick individual items or entire packages as needed. Integration with the WMS, connected to the Bollicine ERP, has fully automated the process.
Operators receive clear instructions for their tasks, while the Modula laser pointer guides them through the picking process, significantly reducing errors.
Farmaenlace
Farmaenlace is an Ecuadorian company specialising in the nationwide distribution of pharmaceutical products. Its distribution centre operates on a single shift from 7 a.m. to 7 p.m., Monday through Friday. The process begins with the reception of the goods, followed by warehouse storage and allocation to different areas to prepare the orders for the retail outlets. With over 200 employees in its logistics centre, Farmaenlace opted to implement Modula vertical warehouses to optimise its space management and improve its operational efficiency. To achieve this, the company installed two Modula Lift ML25D units, each 7,100 mm high, along with a Put to Light system, which assists operators during the picking process, improving both speed and accuracy.
This solution has streamlined picking times, optimised product organisation, and improved ergonomics for the operators, ensuring a faster and safer workflow.
Plub
Launched in 2020 amidst a period of rapid transformation driven by the pandemic, Plub is Paraguay’s first fully digital supermarket. From the outset, the company’s mission was clear: to simplify the shopping process and save customers time through an innovative experience accessible via a smartphone app. Since its inception, Plub has prioritised customer feedback, continuously refining its range of products and introducing new, technology-based purchasing methods. Today, digitalisation is at the heart of the company, which sees technology not merely as a tool, but as a strategic ally in making everyday shopping more convenient and efficient.
This vision led the company to turn to Modula for warehouse automation, installing 3 Modula Lift ML75D units.
Warehouse automation offers an effective solution to the daily challenges faced by distribution companies. By integrating advanced technologies and optimising operational processes, businesses can enhance their efficiency, lower their costs, and better meet their customers’ demands, thus obtaining a competitive edge on an ever-expanding market.
How to optimize picking operations?
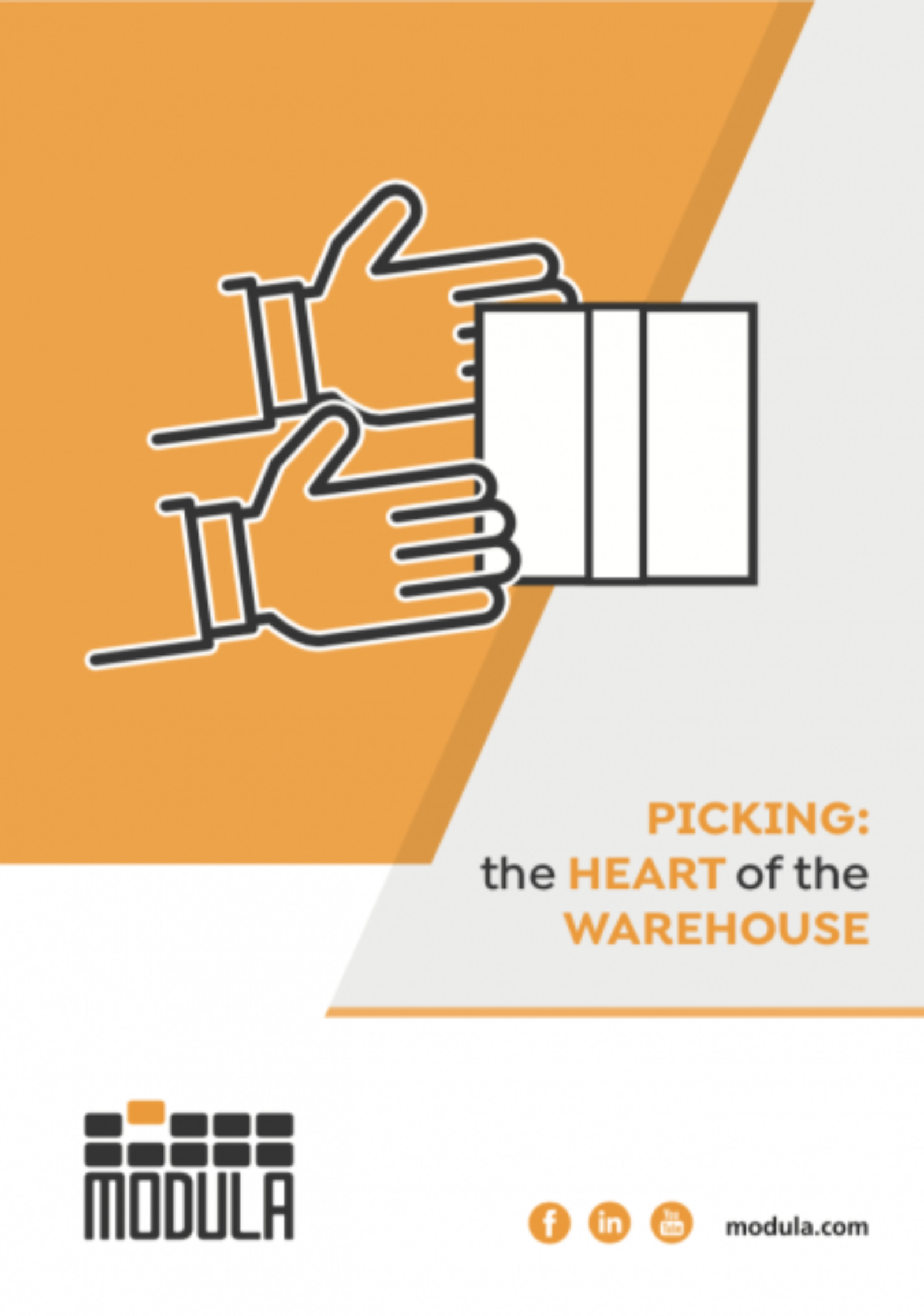