Just In Time is a production management methodology which consists of producing only those quantities of each item requested in a short period of time. If adopting this approach, stocks no longer exist or consist of only small reserves for ensuring supply between one production centre and the next. Just In Time has rightly been defined as a philosophy which involves a company’s entire organisation and has consequences such as the drastic reduction in stocks. A categorical imperative is therefore to eliminate “superfluous” stocks, highlighting and eliminating all inefficiencies and dysfunctional aspects.
How do you go from the “philosophy” of Just In Time to the practice?
Let’s start with an observation that may seem obvious, but which constitutes the fundamental basis of this entire methodology: a manufacturing system without stock can be stopped or adjusted.
But how do you manufacture things with zero or minimal stocks? The main routes are as follows:
- Manufacture only what is required by the market in a very short timeframe and therefore in nearly identical batches.
- Balance production rates across different production lines.
- Implement a perfect information transmission system.
- Provide suitably laid-out production facilities.
Just In Time: a “pull” system
With a “pull system”, your chances of being able to produce only what is demanded by your clients and therefore reach near-zero stock levels are of course very good.
Manufacturing on the basis of orders received, materials are fed (raw or semi-finished materials) into the production process based on a predetermined production schedule, with particular attention being paid to the needs of the production line using them. The production rate is always determined by the downstream line (production centre) which requests availability of the necessary materials from the upstream line.
But how does this work in practice? This is done by performing the following 4 steps in sequence:
- Determine a final assembly schedule;
- Smooth out the final assembly schedule;
- Develop a master production schedule;
- Set detailed production schedules for all production centres.
The final assembly schedule is drawn up a few months in advance, but is adjusted bit-by-bit as the actual production dates approach. At the start this is a plan based on predictions but in the end becomes a plan based mainly on already received client orders and generally has a timeframe which is not too long-term.
Smoothing out the final assembly schedule is intended to balance as far as possible production rates and therefore all production resources. Smoothing out is guided by the market and can be carried out thanks to the ability to produce very small batches.
The master production schedule is nothing more than a daily summary of the quantities to be produced of each item. Detailed production schedules are obtained by exploding the bills of materials contained in the master production schedule.
The critical point in the pull logic is this “smoothing out”. This means that it must be possible and economical to produce single batches because balanced production in short or very short timescales requires a little bit of everything to be produced each day in batches to be assembled into a whole product.
How do you transmit information quickly and efficiently? Using the Kanban system
For a Pull system to operate correctly, you need perfect information transmission: each operation to be performed inside a production facility must be properly documented so it is performed at the right moment and in the correct manner.
One very simple and, at the same time, quick and efficient information transmission method is the so-called Kanban system. This system is based on the circulation of cards between the various production and storage facilities within a factory. The delivery of a card authorises a particular operation to be performed.
The Kanban system is activated by the final assembly line which retrieves items from its own incoming storage unit and the cards then move upwards to the storage point for the preceding production centre and so on. In this way, each production centre knows exactly what to produce and at what rate to produce it. This means they will only produce exclusively what the downstream facility can use.
Physical layout of a Pull system
Implementing a Just In Time system requires work to be carried out on a range of different areas in order to improve the efficiency of the production process. One of these concerns the layout of the buildings housing the production equipment.
In order to create a layout suitable for a Pull system, you need to:
- Organise production into production centres: each of these centres must have incoming and outgoing storage points. Stocks of materials being used in the manufacturing process or part components shall be located exclusively in these areas.
- There shall be only one resupply point for each material within the factory.
- The exact routes each material will take through the production centres and related storage points shall be defined and specified.
In a traditional factory, production equipment is generally kept completely separate from the various warehouses used to store raw materials, semi-finished products and finished products.
In a factory using a Pull system, however, warehouses containing raw materials and finished products have practically disappeared, whilst those containing semi-finished products are replaced with small buffer areas containing enough stock to cover consumption of a few hours (or maximum a few days) and which are necessarily located within the production area close to the production lines in question. In this way, the produced materials, or those awaiting production, are visible to production staff who can therefore immediately detect excessive accumulation or depletion of these components and take the necessary immediate action.
In these buffer areas, the automatic vertical warehouse represents the best solution for mixed storage of raw materials, semi-finished products or finished products.
First of all, they allow you to reduce the floor space occupied by stocks of materials by 90% and further reduce buffer areas by concentrating all picking operations in a small space, thereby speeding up and simplifying the work of your operators.
Secondly, they make picking errors practically impossible. In a Pull system, errors represent a significant risk because, if you are using this model, everything must be aligned and work perfectly in order not to create delays or stoppages in the subsequent manufacturing phase.
Having the right piece or the necessary material in the right place at the right time becomes fundamental to the efficiency of the entire production line for which the crucial functioning of the warehouse is pivotal.
For an example of how the automatic vertical warehouse can actually become the engine of a move to the Just In Time philosophy, please see here: MT Marchetti & Modula: how to store 1,750 m2 of material in 100 m2.
7+1 Deadly Sins of the Warehouse
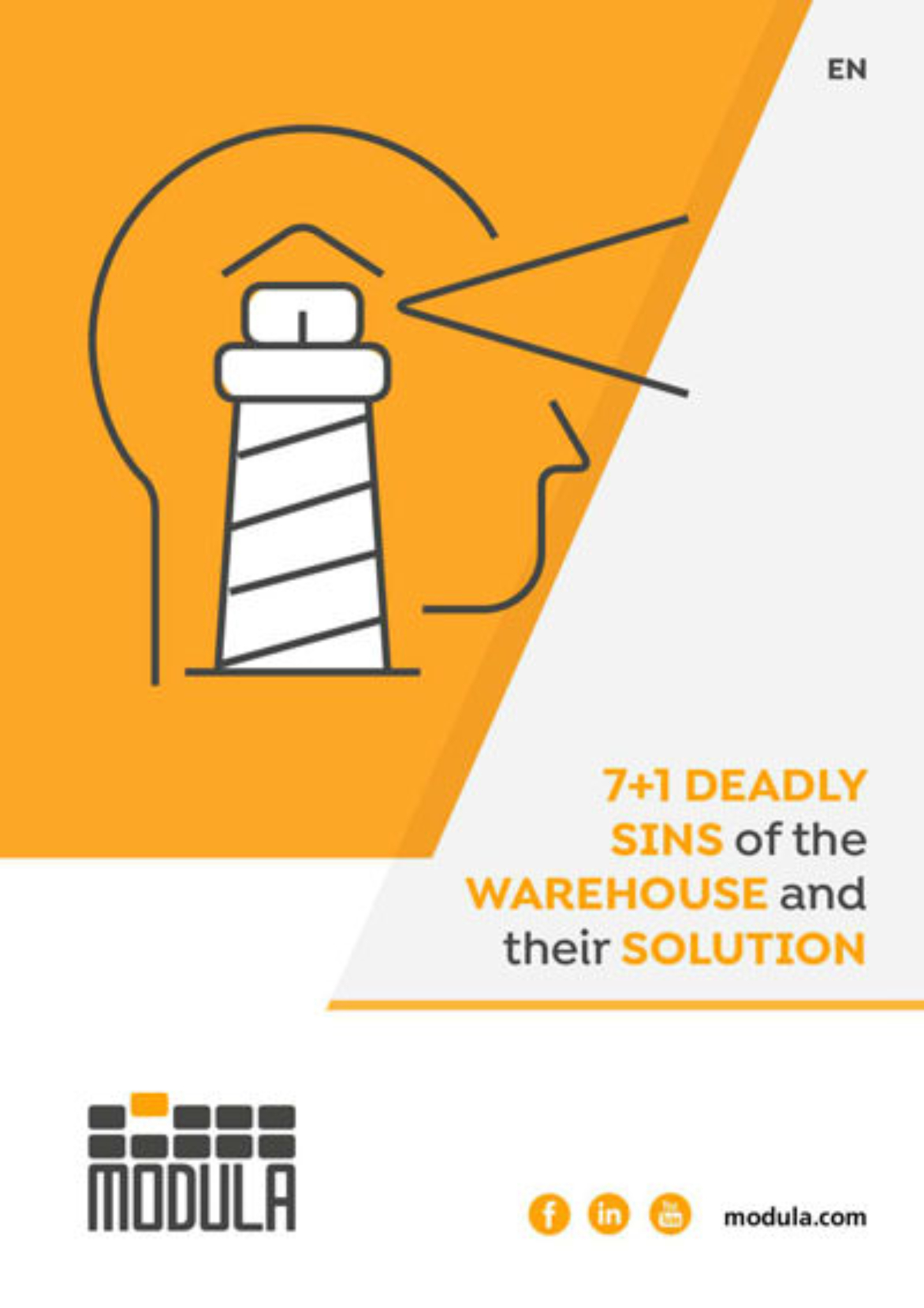