When the decision is taken to open an online portal, it is important not only to focus on online factors, such as having a responsive site, the user experience or users’ reviews: the quality of the product and the speed with which it is delivered are key elements in any successful e-commerce business. But how can e-commerce picking operations be speeded up?
Online customers expect to receive products within a very short time, so an e-commerce business must be supported by a well organised, efficient warehouse, in order to respond promptly to every request, while storing a vast assortment of products. There are two methods of picking goods: “man to goods” and “goods to man”.
“Man to goods” picking method
The “man to goods” picking method is the most widely used: the operator moves around the warehouse in search of the material. It is still the most widely used today due to its low implementation cost, but it has considerable shortcomings: a high execution time and the risk that the operator may make mistakes in the picking phase. In terms of performance, especially for online businesses, it is the poorest overall. It is estimated that the operator spends about 50% of the total time taken to prepare an order simply moving from one point in the warehouse to another.
This picking method includes different types of procedures:
- Batch picking: the operator moves around the warehouse with several boxes, one for each order to be prepared. However, this is only efficient if there are not many orders to be expedited and the warehouse is not too large.
- Wave picking: a procedure in which a maximum number of products are picked and only sorted at the end of the picking operation. In this case, the individual products should be identified with the aid of codes (e.g. with a barcode scanner).
- Zone picking: each operator is only responsible for one zone of the warehouse and only performs picking procedures in his zone. The products picked are placed in a bin which is moved around the zones. This system is suitable for large warehouses with a vast range of articles, and usually envisages a different number of operators in what is known as the “golden zone”.
“Goods to man” picking method
The “goods to man” picking model overturns the traditional concept of the warehouse, allowing e-commerce picking operations to become much faster: the product is moved towards the operator by an intuitive, automatic system, so the worker no longer has to move away from his workstation. It is more expensive and is less flexible if the warehouse’s layout is revised in the future, but it has one obvious strong point: a reduction in picking errors, better performances than the man to goods model and a shorter order preparation time.
Vertical warehouses mean that operators do not have to carry goods around to the same extent, since the loading unit is delivered to the picking bay itself. Picking operators also enjoy an ergonomic working posture, and manipulators, robots or zero balancers can sometimes be added for handling heavy or bulky loads.
Vertical warehouses with trays to facilitate picking operations
Automatic solutions, such as automatic vertical warehouses, provide more efficient stock management and a significant reduction in errors, especially if combined with a WMS software. In this case, the warehouse is able to keep track of all incoming and outgoing goods, providing constant control over your stock situation and improving inventory management.
With this technology, you can have real-time information about stock levels, very useful for optimising reorders and the logistics of your production process. Moreover, each time goods are stored or retrieved, the operator is given clear indications about theoretical stock levels and can compare these with real levels and facilitate their alignment in the event of an inventory.
To further increase precision in stock management within your warehouse and reduce errors, simple and intuitive visual aids are available. Any operator can use these devices to easily identify products that are to be picked from or refilled into the automatic warehouse, even without any special training.
Automation: the way forward to manage e-commerce logistics
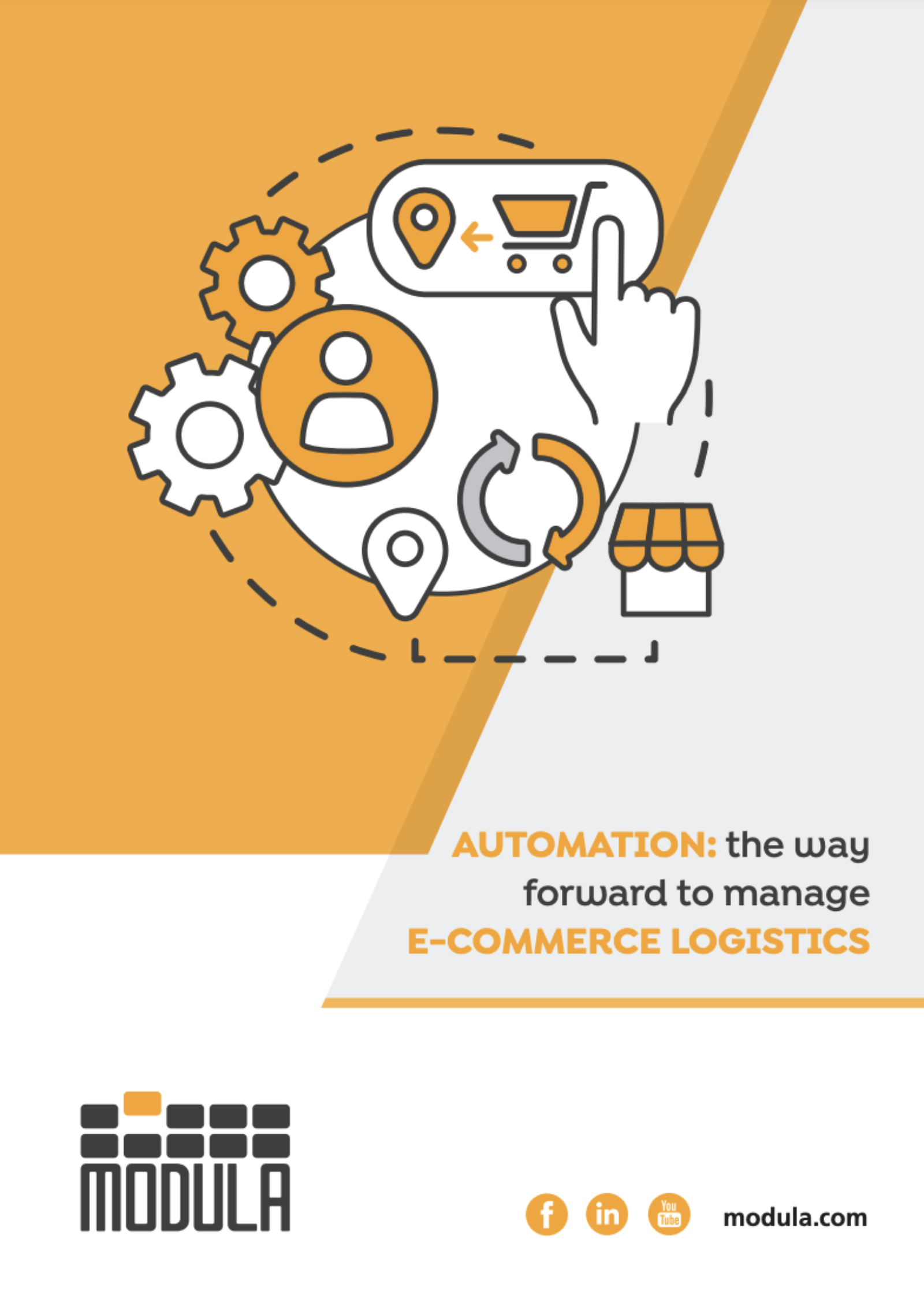