Interview with Alberto Hausmann – Modula Spa Supply Chain Manager
Logistics is a broad and multi-faceted topic which has been expanding in recent years and increasingly incorporates automated solutions that are changing the scenario in which companies are moving and will have to move.
Many terms are used every day and often taken for granted: among these, the expression “Supply Chain” is sometimes confused with or mistakenly used in place of other terms.
For this article, we went to interview Alberto Hausmann, Modula Spa Supply Chain Manager, not only to talk about what the Supply Chain actually is but also to learn how it is managed at Modula, a company that has made logistics its core business.
1. What is a Supply Chain and what is the difference between Supply Chain and Logistics?
Corporate Logistics means the management of the flows of goods (and the related information) within a company; Supply Chain Management means the management of flows throughout the supply chain (supplier – manufacturer – distributor) or at least between manufacturer and distributor. They are very different things, although the second is an extension of the first.
It should also be said that today the term Supply Chain Management is widely used to refer to Company Logistics or, at most, Integrated Logistics, while the term Logistics is once again being used with its original meaning of “warehouses and transport”, which is the reason why transport companies are referred to as Logistics companies.
The very concept of “Logistics” has changed over time.
In fact, the word “Logistics”, which was once identified with “Distributive Logistics”, thus something purely physical, now encompasses a wider concept, similar to that of “Supply Chain”.
There are, of course, various topics on which operators focus their attention.
In the 1980s the emphasis was mainly on optimizing transport costs and occupying less space, as well as on the inevitable improvement of physical flows.
In the 1990s the importance of the flow of information began to be understood and therefore, while the first information systems dedicated to logistics and warehousing were slowly making their appearance, the interest in issues such as the organization of processes, the strategic role of logistics choices, and the importance of customer care grew significantly.
Thus today we speak of “Logistics” as a “Chain”, more specifically, the “Supply Chain”.
The hot topics currently include:
- integration upstream and downstream in the supply chain
- the segmentation of customers according to logistics management principles
- flexibility
- the logistics price list differentiated according to the services promised to the customer.
All very important issues which Modula tries to address in its ongoing effort toward improvement.
2. What is Supply Chain Management and what departments does it involve?
Supply Chain Management is the single channel management that is created by organizing the flow resulting from sales and centralizing inventory management. For example, sales outlets pass information to the distribution centers regarding sales, the distribution centers pass it on to the manufacturers and consequently replenish their supplies with batches intended to last for a few days, based on what has been sold or is expected to be sold.
The logic behind Supply Chain Management is that the market must condition production and not vice versa: that is, you buy or produce what you expect to sell rather than having to sell what you bought or produced.
3. What competitive advantage does this lead to?
It puts the customer at the center, with the goal of providing quality services.
4. Who is the Supply Chain Manager and what do they do?
Success requires great determination on the part of the companies in the supply chain as well as a supply chain manager at the managerial level, with a unified vision of the entire process.
The supply chain manager is the conductor of an orchestra where:
- procurement is the brass instruments
- logistics is the woodwind instruments
- customers are the percussion instruments
- and production is the bowed string instruments.
5. What are the objectives of the Supply Chain?
My favorite is the “8 R” definition, which reads:
- Right material
- Right quantity
- Right quality
- Right place
- Right time
- Right method
- Right cost
- Right impression
6. What equipment does a Supply Chain require?
Software and hardware. Intelligence and electromechanics
Depending on the complexity of the chain, the following could be useful or sometimes even indispensable:
- Demand management or planning software
- WMS for warehouse management
- transport management software
- procurement software.
Investments in equipment can also be more or less complex:
- automatic storage systems
- robotic picking systems
- automated guided vehicles to move pallets.
7. What are the elements that characterize the supply chain and its potential advantages?
As noted, there are some factors that deserve particular attention and which are often critical for a good Supply Chain these days.
Supply Chain Management operators must aim at integrating processes and all the parties involved while putting the customer at the center. In this way, all waste and any inefficiencies are limited.
8. How is the supply chain organized at Modula?
The pandemic led us to upgrade our supply chain. We went from “just in time” production to a “just in case” paradigm.
Starting from the assumption that we produce on a two/three-week schedule, we freeze production weeks and establish ahead of time what machines, and for what customers, will be produced in those slots.
We know that on day X at Y time a specific Modula model will be produced with a specific serial number for a specific customer. It is true that while our product is standard, it has thousands of possible configurations in terms of height, tray width, depth, capacity and number of trays.
Our production system is 99% in-house, except for the electrical panels and lifts. In order to prevent production downtime, we have developed and optimized contracts with our main suppliers to ensure that the material we need is always available. To achieve this, we guarantee our suppliers a large number of orders.
Our suppliers, in addition to guaranteeing deliveries, also operate as logistics hubs, delivering the material when necessary for production. This also protects us from contextual problems such as those we experienced in recent years, one of them being Covid.
Our supply chain is based on four steps to be implemented in sequence: SELL – PRODUCE – SHIP – INSTALL.
All this is possible thanks to highly digitized systems and software applications that allow us to remotely monitor every production step. This minimizes errors in real time, preventing non-compliances and any need for disposal.
Want to know more?
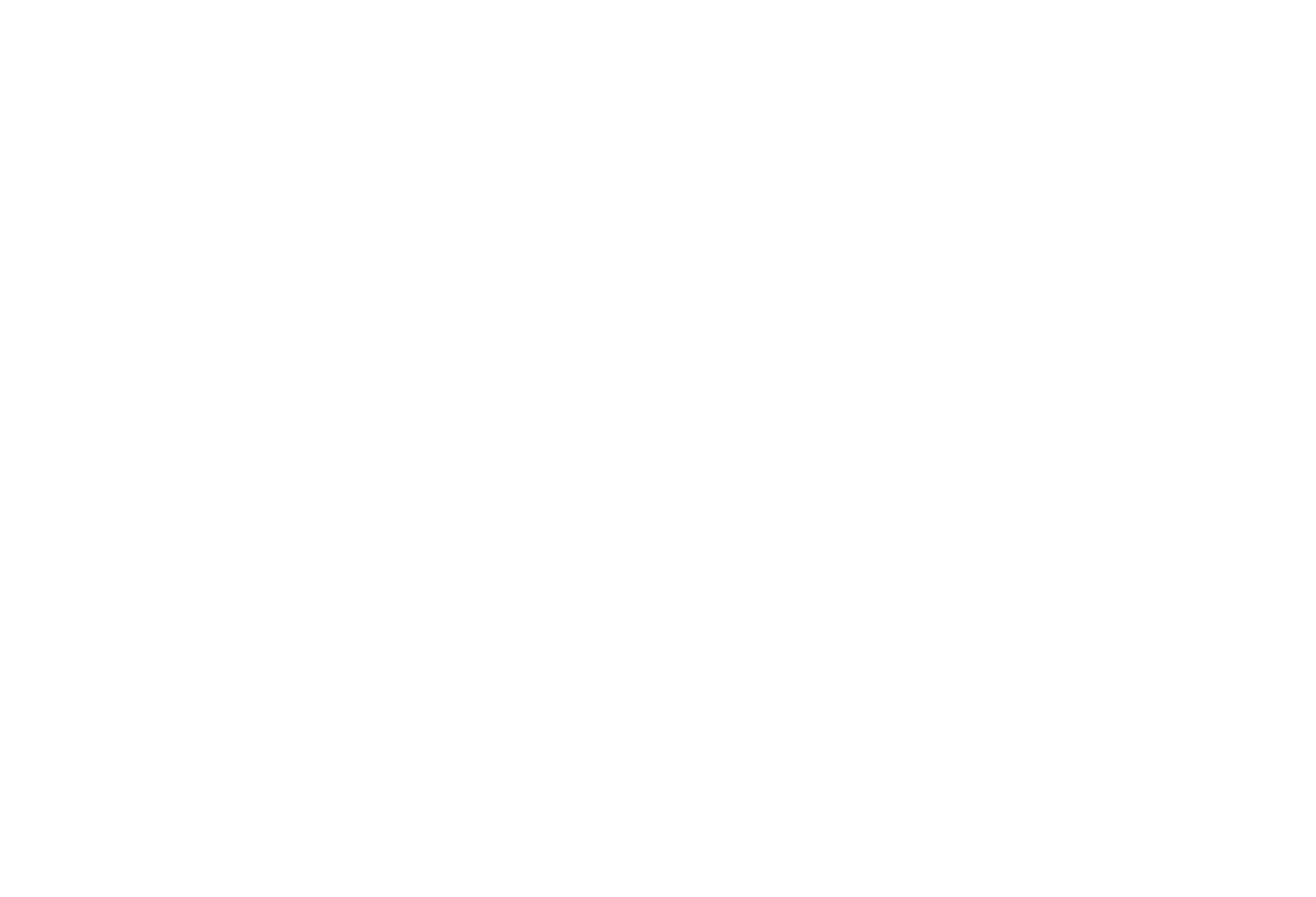