Let’s make some assumptions about sales volumes and problems getting supplies of an item in constant demand which is obtained from a supplier.
Supposing that:
- The unit price is known, constant over time and unaffected by the quantity purchased.
- The order is always delivered in the same manner.
- Any quantity can be ordered.
- Reorder time (interval between issuing order and delivery of goods) is known and constant.
- Demand is constant (d) over time and the sale price is constant over time.
- We want to meet all customer demand promptly remembering that the cost of running out of stock is very high.
- The item in question is not perishable.
- Holding costs are proportional only to the value of the items and the storage period.
These assumptions, being the basis of the so-called “Wilson model” have the following consequences:
- The quantity to be purchased in each order is constant.
- The interval between two successive orders is constant.
- It is advisable to place an order so that when each batch arrives there is no stock remaining.
- The only costs affecting the decision about the quantity to purchase and the interval between orders are the costs related to ordering and holding.
The only problem you will have to face when managing this situation is deciding whether to place fewer orders of large quantities or more orders of small quantities. The solution depends entirely on the costs related to holding and ordering.
If you want to reduce storage costs to a minimum, you need to look at automated storage solutions which are designed to make the most of available vertical space, such as automated vertical warehouses.
This is because this type of warehouse will allow you to reduce to practically zero the cost of moving the products around, maintaining enough space as if in a traditional warehouse and keeping the products in good condition.
Economic order, rotation time, order point
The question is: “Do I order larger quantities in a small number of orders or small quantities in many orders?“.
The Wilson model states that the only thing that matters here is the cost of ordering (which increases along with the number of orders) and the cost of holding (which increases along with the number of delivered lots and decreasing number of orders). This is therefore about expressing an objective function and understanding at what value per lot the total cost of ordering and holding is minimised.
Once this quantity has been established, you can also automatically determine rotation time and how many orders to place throughout the year. The last thing to ascertain is the right moment to issue the various orders and therefore the order point.
In the Wilson model, since you don’t want to have any stock left when a new batch arrives from the supplier, the order point is equal to the amount used during the lead time required by the supplier to replenish the stock.
Variants to the Wilson model
Moving away from the assumptions contained in the Wilson model, let’s no longer assume that demand is constant over time and instead accept that there is some random variability. This means that some demand figures are known along with how likely they are to occur, respectively.
In these scenarios, we can no longer think about managing supply by issuing orders for constant quantities at constant intervals, but we have to choose between:
- Management by order point which means reordering constant quantities each time available stocks reach the order point.
- Management by periodic reordering which means reordering variable quantities at fixed intervals.
In both these cases it is no longer possible to be certain of meeting all levels of demand, but it is possible to imagine meeting demand with a certain degree of probability. How? Supposing that this random variability in demand, and in particular in demand during reorder time (supplier lead time) is a “Gaussian” distribution.
The “Gaussian” (or “normal”) distribution is where a normal random variable has a high probability of convergence with values close to the variable’s mean value and this probability is reduced slowly as it moves away from this value. The “Gaussian” distribution is suited to describing many random phenomena of definite interest such as is the case with sales of a certain product within a certain period.
40 Warehouse KPIs to monitor and measure performance
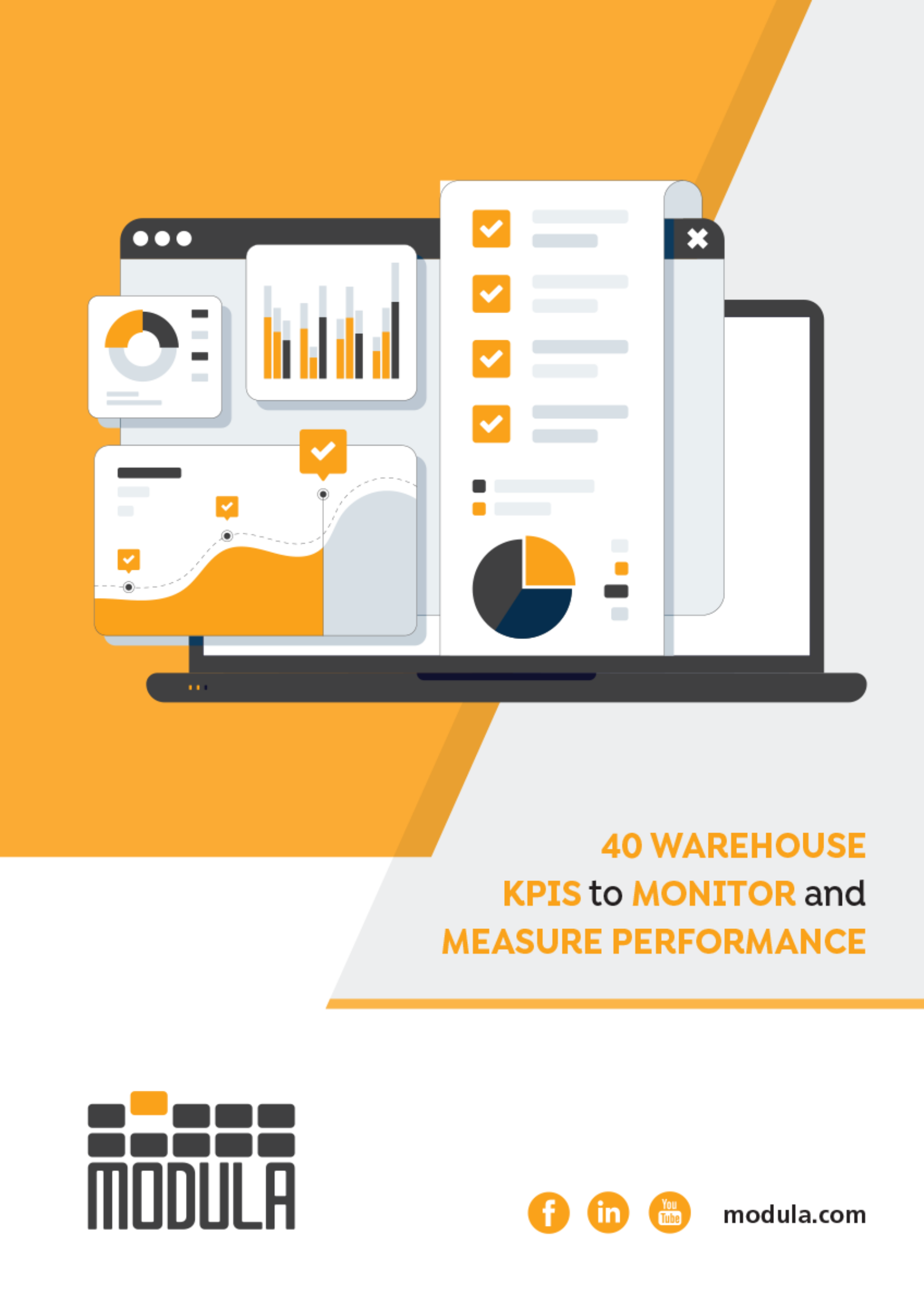