Wenn wir von Kühlkette (auf Englisch Cold Supply Chain) sprechen, meinen wir eine temperaturkontrollierte Lieferkette, die folgende Systeme umfasst:
- Herstellung
- Einlagerung
- Vertrieb
Jedes dieser Systeme muss mit Geräten ausgestattet sein, die es ermöglichen, die Temperatur konstant und im erforderlichen Bereich zu halten, damit das verarbeitete und vertriebene Material oder Produkt nicht verunreinigt wird oder verdirbt.
Die Kühlkette ist daher einer der komplexesten – und somit auch teuersten – Managementprozesse der Logistik und spielt in temperatursensiblen Bereichen wie Lebensmittel, Pharmazeutika, Elektronik, Gartenbau und Leder eine wichtige Rolle.
Aufgrund der Beschaffenheit der Produkte ergeben sich im Management der Kühlkette besondere Probleme, die sie von der traditionellen Lieferkette unterscheiden. Als Beispiel können Impfstoffe herangezogen werden, die während der gesamten Lieferkette von der Herstellung bis zur Anwendung eine möglichst konstante Temperatur erfordern. Wird der exakte Bereich entlang der Kette auch nur für kurze Zeit nicht eingehalten, bedeutet dies eine Beeinträchtigung der Sicherheit und Effizienz und macht den Impfstoff unbrauchbar.
Die 3 Hauptprobleme der Kühlkette
Die Hauptprobleme der Kühlkette ergeben sich aus der Notwendigkeit, eine konstante Temperatur während der Vorbereitungs-, Lagerungs- und Transportprozesse aufrechtzuerhalten, um die Qualität und Sicherheit von verderblichen und temperaturempfindlichen Produkten zu gewährleisten. Dies sind die 3 Hauptprobleme, die sich aus dem Faktor Temperatur ergeben und wirtschaftliche Auswirkungen haben:
1) Hohe Kosten für die Temperaturkontrolle
Einige Sektoren, in denen die Kühlkette zum Einsatz kommt, haben direkte Auswirkungen auf die Gesundheit der Menschen (man denke nur an die Lebensmittel- und Pharmaindustrie), und aus diesem Grund sind die Anforderungen an die Temperaturkontrolle streng und für alle Stufen der Kühlkette standardisiert.
Die Referenz in Europa ist die EG-Verordnung 37/2005, welche die Messung und Aufzeichnung der Temperatur in regelmäßigen Abständen sowohl in den Transportmitteln als auch an den Lagerorten vorschreibt. Dies bedeutet, dass sowohl die Transportmittel als auch die Lager mit geeigneten Instrumenten ausgestattet sein müssen, um die sichere Temperatur für das Produkt zu gewährleisten und sie über die Zeit zu messen.
Beispiele für diese für die Kühllogistik spezifischen Instrumente und die erforderlichen hohen wirtschaftlichen Investitionen – die sogar fünfmal höher sind als für den Transport und die Lagerung von Trockengütern -, sind Kühlzellen, Gebäudedämmung, Temperatursensoren und Kühlcontainer für den Transport. Die Kosten steigen auch durch den Strombedarf der Kühlanlage.
2) Risiko von Verunreinigung und Verderb
Die Verunreinigung oder der Verderb von Produkten, die eine kontrollierte Temperatur erfordern, hat enorme wirtschaftliche Auswirkungen für ein Unternehmen. Ein Beispiel dafür ist der Lebensmittelsektor, in dem aufgrund der massiven Ausbreitung der Supermärkte und des Online-Handels die Kühlkette zunehmend genutzt wird. Lebensmittel sind leicht verderblich und neigen zur Ausbreitung von Pilzen, Bakterien und mikrobiellem Wachstum, wenn sie nicht ordnungsgemäß behandelt und gehandhabt werden. Auch in der Logistik sind darüber hinaus die Regeln gemäß HACCP zu beachten.
Im Zusammenhang mit dem Verderb der Materialien gibt es sowohl direkte als auch indirekte Kosten, die in der gesamten Lieferkette anfallen und insbesondere in der Lagerphase, dem einzigen Glied in der Logistikkette, in dem die Temperatur gesenkt wird, sehr hoch sein können.
Sollten die Produkte verunreinigt werden oder verderben, hätte dies mehrere direkte Folgen:
- Entsorgungskosten für nicht verwendbare Produkte
- Qualitätsprüfungskosten
- Nachschubkosten
Indirekte Kosten können stattdessen identifiziert werden in:
- Verlust von Ansehen und Vertrauen
- Verlust von Marktanteilen
- Etwaige Rechtsstreitigkeiten aufgrund von Schäden, die durch die Waren verursacht wurden
Um das Risiko von Produktverunreinigung und -verderb zu verringern – und die damit verbundenen Kosten zu vermeiden – ist es sehr wichtig, alle Temperaturkontroll-maßnahmen umzusetzen und Technologielösungen zu verwenden, welche die Kühlkette unterstützen.
3) Kommissionierzeiten
In engem Zusammenhang mit dem oben genannten Sicherheitsrisiko müssen die Kommissionierzeiten in der Kühlkette minimiert werden, um die Unversehrtheit der gehandelten Produkte zu gewährleisten. Die Kommissionierung stellt nämlich einen kritischen Vorgang dar, da das Produkt oder die Ware außerhalb der klimatisierten Umgebung verbleibt, und diese Zeit muss verkürzt werden, um Sicherheit und Unversehrtheit zu gewährleisten.
Bei der Konzeption eines Lagerverwaltungssystems für verderbliche Produkte ist es unablässlich, Kommissionierungsstrategien und Automatisierungswerkzeuge einzusetzen, welche die Verweildauer außerhalb des Kühlbereichs minimieren.
Lösungen zur Begrenzung der Kühlkettenkosten
Zwar sind die mit der Kühlkette und ihrem fehlerhaften Management verbundenen Kosten sehr hoch, doch kann ein Unternehmen durch den Einsatz technologischer Verfahren und Lösungen die Kosten erheblich begrenzen, die Organisation optimieren und die Risiken verringern.
Diese Lösungen können in den folgenden Phasen der Lieferkette umgesetzt werden:
- Herstellung
- Einlagerung
- Verladung von Waren
- Transport
- Entladung bei Vertriebszentren oder Verkaufsstellen
Der letzte Schritt, d. h. die Abholung, Lagerung und der Transport zum Endverbraucher, liegt außerhalb der Kontrolle des Unternehmens, es sei denn, es handelt sich um Online-Handel.
Automatisierung der Kommissionierphase
Bei der Kommissionierung handelt es sich nicht nur um eine sicherheitskritische Phase, sondern auch um einen Vorgang, in dem die Mitwirkung des Bedienpersonals nicht immer möglich ist (man denke nur an Tiefkühllager, in denen Temperaturen von bis zu -30 Grad herrschen können).
Um Thermoschocks für die Produkte zu vermeiden, die Zeit zu verkürzen und Verderb zu verhindern, setzen moderne Kühlkettenzentren anthropomorphe Roboter ein, um die Kommissionierung zu automatisieren. Die umgesetzte Logik ist also die der Ware-zu- Mann, wobei auch die neueste Technologie zur Spracherkennung genutzt wird, die es dem Bedienpersonal ermöglicht, Befehle über den Kopfhörer zu erteilen und zu empfangen.
Die Kosteneinsparungen ergeben sich aus einer schnelleren Kommissionierung und aus der Fähigkeit der anthropomorphen Roboter, den Zustand der Produkte automatisch zu erkennen und kritische Punkte zu identifizieren.
Verwendung von automatischen und vertikalen Lagern mit kontrollierter Temperatur
Die Kühlung eines Lagers kostet Geld, auch in Bezug auf die benötigte Energie. Aus diesem Grund ist es wünschenswert, die verfügbare Fläche so weit wie möglich auszunutzen, um die Energiekosten zu senken.
Die Lösung für dieses Problem sind Vertikallager, die es möglich machen, bis zu 90 % der verfügbaren Lagerfläche einzusparen. Die automatischen Lager Modula Lift Climate Control ermöglichen darüber hinaus die Temperaturkontrolle in einem Bereich von +2 bis +25 Grad und kombinieren die Vorteile der vertikalen Lagerung mit einer Technik, die die für eine sichere Lagerung erforderlichen Temperatur und Feuchtigkeit garantiert.
Ein automatisches Lager ermöglicht es auch, die Kosten im Zusammenhang mit dem Temperaturverlust durch automatische Kommissionierung und Lagerung zu reduzieren.
Einführung von Lösungen für das automatische Handling in den Tiefkühlzellen
In Lagern mit geregelter Temperatur, wo die Lagertemperaturen niedrig sind, werden zunehmend automatische Waren-Handlingssysteme eingesetzt, die den Zeitaufwand des Personals in diesen Bereichen verringern. Ein Beispiel sind Palettenregalbediengeräte und Paletten-Shuttles, die durch eine Fernsoftware gesteuert werden und die Lagerung automatisch durchführen. Das Ergebnis ist eine verbesserte betriebliche Effizienz und Geschwindigkeit.
AMR-Fahrzeuge, Roboter und alle Handling-Systeme, die in temperaturgeregelten Lagern oder Tiefkühlzellen eingesetzt werden, weisen unterschiedliche strukturelle Merkmale auf. Die besonderen Bedingungen von Temperatur und Luftfeuchtigkeit können nämlich den Betrieb beeinträchtigen und so kombinieren, dass sie sogar gefährlich sein können.
Die niedrigeren Kosten hängen in diesem Fall immer mit dem geringeren Energieverlust, der geringeren Exposition gegenüber möglichen Verunreinigungen der gelagerten Produkte und dem Schutz der Gesundheit des Bedienpersonals zusammen.
Überwachung der Kühlkette mit Sensoren und IdD-Lösungen
Alle oben genannten Lösungen basieren auf modernsten Sensorsystemen zur Erfassung von Temperatur, Position und Größe sowie auf IdD-Lösungen zur Analyse und Auswertung der erfassten Daten. Das Internet der Dinge und die Sensoren helfen so, eine konstante Temperatur entlang der Kühlkette zu gewährleisten und Energieverschwendung zu vermeiden.
Daher ist es möglich, die technologischen Möglichkeiten zur Verbesserung des Managements und zur Sicherung der Kühlkette in vollem Umfang zu nutzen, und das zu einer Zeit, in der sie eine starke Expansion erlebt. Man denke nur an den Online-Lebensmittelhandel oder den Pharmasektor, wo die Nachfrage nach Produkten, die eine kontrollierte Temperatur erfordern, von Jahr zu Jahr steigt.
Die in diesen Sektoren tätigen Unternehmen müssen daher ihre Lager umorganisieren, um sowohl die neuen Standards im Hinblick auf die ordnungsgemäße Behandlung der Waren zu gewährleisten als auch die Kosten zu senken und die Effizienz ihres Logistiksystems zu verbessern.
8 Arten von Verschwendung, die durch Modula Vertikallager vermieden werden können
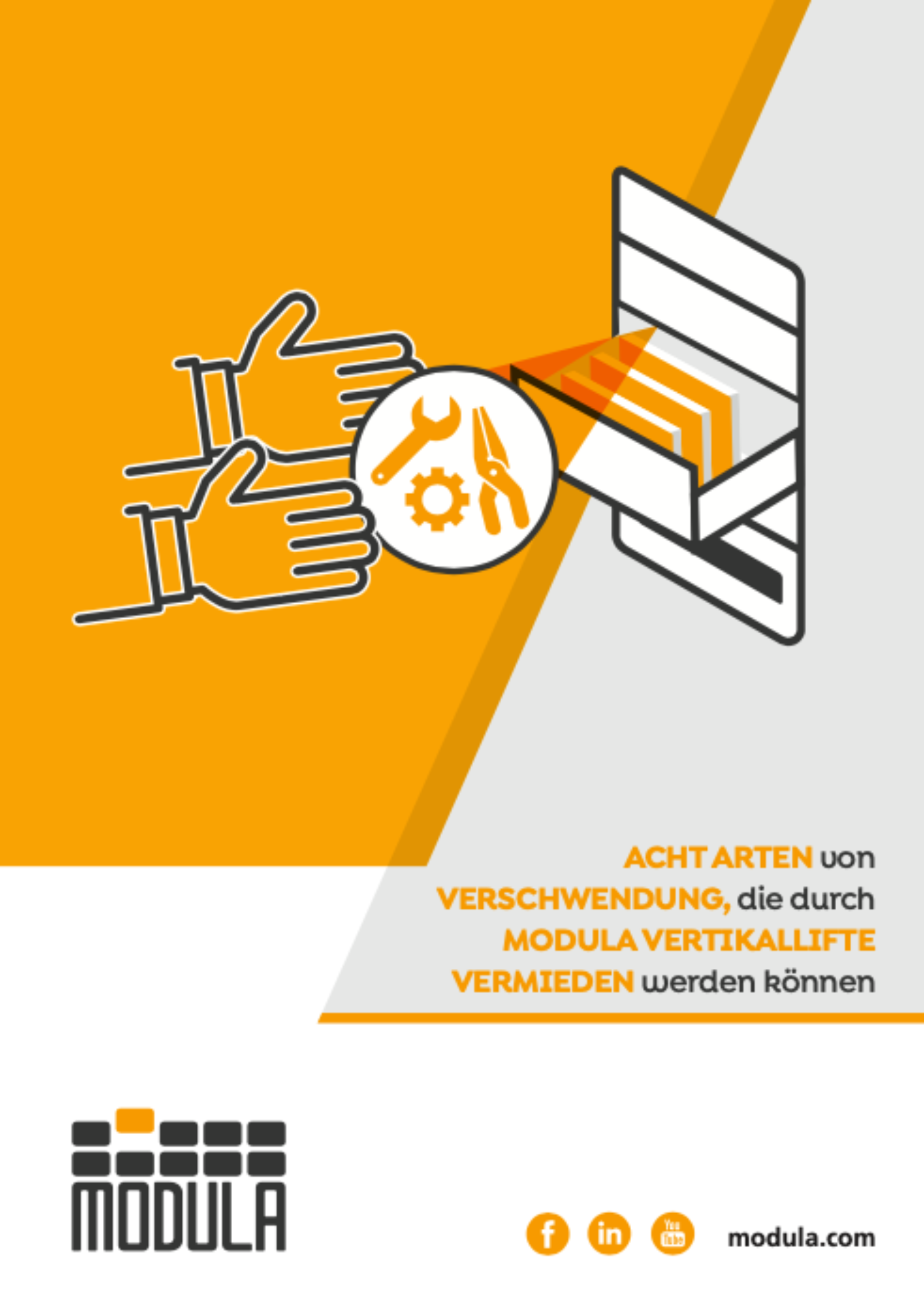