Das Lager spielt in Unternehmen eine Schlüsselrolle. Es kann nicht nur als physische Einheit interpretiert werden, sondern ist ein wichtiger Teil der Produktionskette und muss dahher als solche durch strategische Geschäftsabläufe gesteuert werden.
Die Lager haben sich im Laufe der Jahre verändert. Jetzt können sie aus verschiedenen Gründen, die vom Outsourcing bis zur Fortsetzung der Liefer- und Produktionspolitik reichen, auch nach außen expandieren.
Es kann daher vorkommen, dass ein Lager komplett neu gestaltet werden muss, um die Leistung zu maximieren und kostspielige Probleme wie Platzmangel und verschwendete Zeit bei der Suche nach Artikeln in einer extrem großen und unorganisierten Umgebung wie dem Lager zu vermeiden.
Aber wie kann man ein Lager neu gestalten, die Leistung maximieren und dabei das Budget nicht überbelasten? Welche Schritte sind zu befolgen?
Zunächst können Maßnahmen zur kontinuierlichen Verbesserung eingeleitet werden, um kleine alltägliche Probleme zu beseitigen (Direktlieferungen von Lieferanten, Neugestaltung der Verpackung, um Platz zu sparen, Verbesserung der Prognosemethoden). Anschließend sollte die Unternehmensleitung in die Neugestaltung des Lagers investieren und sich dabei auf den Rat von Experten aus dem Logistiksektor stützen.
Nachfolgend werden die verschiedenen Phasen zur Gestaltung eines automatischen Lagers im Detail vorgestellt:
1. Gantt-Diagramm und Investitionsschätzung für ein automatisches Lager
Um die Investition abzuschätzen, müssen notwendige Analysen durchgeführt werden, die die Angemessenheit der Intervention im Hinblick auf die festgelegten Ziele belegen. Es ist sehr wichtig Schätzungen über die Dauer der Maßnahme und die Planung der operativen Ziele vorzunehmen, auch unter Berücksichtigung der Tatsache, dass man bei der Ausführung möglicherweise nicht innerhalb der Fristen liegt.
Dabei sollte man sich von Experten mit Erfahrung auf diesem Gebiet unterstützen lassen. Auf diese Weise wird es einfacher sein, analoge Schätzungen vorzunehmen, d. h. solche, die auf früheren Maßnahmen basieren oder parametrische Schätzungen der bereits durchgeführten Arbeiten.
Aber wird sich die Neugestaltung des gesamten Lagers auszahlen? Innerhalb welchen Zeitraums?
Der Bau eines neuen Lagers oder die Nutzung neuer Technologien verursacht Kosten, die oft mit Hilfe einer Gantt-Analyse quantifiziert und über die Zeit verteilt werden müssen.
Mit einem Gantt-Diagramm werden Maßnahmen auf einer Zeitachse zur Projektplanung und -kontrolle dargestellt und es zeigt an, wann eine Maßnahme beginnen und wann sie enden muss. Auf der X-Achse haben wir die Zeitskala vom Anfang bis zum Ende des Projekts und auf der Y-Achse die Dinge, die Sie tun müssen, um das Projekt abzuschließen. Tragen Sie alle geschätzten Maßnahmen ein und Sie erhalten einen vollständigen Überblick über das Projekt. Auf einen Blick sehen Sie, was Sie priorisieren müssen, wie viel Zeit bis zum Fristende bleibt, welche Maßnahmen Sie gleichzeitig ausführen müssen um Zeit zu sparen oder welche von anderen abhängen.
Das Diagramm wird verwendet, um die rechtzeitige Ausführung einer Reihe von Maßnahmen zu überwachen. Es kann von einer Reihe von Informationen begleitet werden: Wer die Aufgabe zu erfüllen hat, ob derjenige Vollzeit oder Teilzeit arbeitet, wie viel von der Arbeit geleistet wurde und wie viel noch zu tun ist.
2. Audit und Machbarkeitsstudie
Wichtig ist zunächst, die Stärken und Schwächen zu analysieren und die Maßnahmen entsprechend dem Zweck und dem Ziel, die Sie erreichen wollen, zu definieren. Es muss mit einer Überprüfung der Lagerleistung begonnen werden, um kritische Punkte zu identifizieren und zu beseitigen: Das ist das Audit.
Im Mittelpunkt sollten die Leistungsindikatoren, Prozesse, Instrumente, Technologien und eingesetzten Kosten und nicht zuletzt die beteiligten Mitarbeiter stehen.
Mit einer Machbarkeitsstudie lassen sich Probleme lösen und die operativen Ergebnisse verbessern. Bei der Analyse der Daten identifizieren werden die Alternativen in Bezug auf Organisation, Lagerung und Logistik verglichen, um dann die mit dem besten Kosten-Nutzen-Verhältnis auszuwählen.
Die alternativen Lösungen berücksichtigen verschiedene Aspekte wie den Masterplan des Standorts, das Layout des Lagers, die betrieblichen und logistischen Kriterien, die eingesetzten Personal- und Kostenressourcen sowie den Zeitplan. Auf der Grundlage aller gewonnenen Informationen kann die Unternehmensleitung die bestmögliche Alternative für das weitere Vorgehen wählen.
Für weitere Informationen lesen Sie den Artikel über die Vorbereitung eines Audits und die Machbarkeitsstudie.
3. Slotting: die Vorbereitung von Produkten
Um die niedrigsten Kosten für die Lagerverwaltung und weniger Bewegungen zu erreichen, sollten die Produkte im Pickingbereich besser platziert werden. Durch die Erfassung und Analyse der Historie der Lageraktivitäten kann nachvollzogen werden, wo die Produkte im automatischen Lager und welche Artikel in der Nähe platziert werden sollten.
Die Slotting-Analyse ermöglicht es Ihnen zu verstehen, wo Sie die Produkte im Lager platzieren und wie Sie sie klassifizieren können, um Zeit zu sparen und Ressourcen zu optimieren.
Für weitere Informationen lesen Sie bitte den Artikel über Slotting Optimierung.
4. Detailliertes Projekt
Wenn festgestellt wurde, dass es sinnvoll ist die Investition zu tätigen, ist es notwendig, eine detaillierte Analyse des Projekts vorzunehmen. Dies bedeutet, auf die funktionalen, technischen, betriebswirtschaftlichen und systemischen Aspekte einzugehen, die in der Machbarkeitsstudie erwähnt wurden.
Durch Vertiefung und Analyse der Projektdaten wird ein endgültiges Layout mit Zeichnungen, Plänen, Abschnitten und Details festgelegt.
Das Logistikprojekt muss auch Gebäudeaspekte (z. B. ist es mit automatischen Lagern möglich, diese extern einzusetzen und zu berücksichtigen, dass diese isoliert werden müssen oder manchmal auch erdbebensichere Lösungen benötigen) und den Anlagenbau (z. B. Sprinkleranlagen, Heizung, Kühlung, Beleuchtung und Druckluft) berücksichtigen.
Anschließend werden die Betriebsabläufe definiert und ein detailliertes Gantt-Diagramm erstellt.
5. Dynamische Simulation
Die dynamische Simulation versucht das Verhalten eines Systems oder Gebäudes vorherzusagen, wenn alternative Szenarien vorgeschlagen werden. Ausgehend von einer Abbildung der logistischen Prozesse des Unternehmens und dem Vergleich verschiedener Szenarien identifiziert sie Risiken und Engpässe und steuert die Leistungsfähigkeit des Systems.
Sie beginnt bei der Datenerfassung und Validierung des konzeptionellen Modells, das darauf abzielt, dass das gesamte Projektteam die zu testenden Szenarien, die Hypothese und die getroffenen Annahmen teilt. Weiter geht es mit der Definition der zu testenden Szenarien und des zu erwarteten Vertrauensgrades für den Vergleich der Ergebnisse. Die numerischen Daten werden in Projektlösungen umgesetzt und die Ergebnisse aufgezeigt, um dem Kunden bei der Entscheidungsfindung zu helfen.
Für weitere Informationen lesen Sie den Artikel über dynamische Simulationen zur Risikominimierung in der Logistik.
6. Baummaßnahme
Die dynamische Analyse ist von unschätzbarem Wert, wenn es um die Baumaßnahme geht. Nach der Projektdefinition und der Festlegung der Lieferanten erfolgt eine kritische Überprüfung der Bauzeichnungen und der verschiedenen Dokumente zur Automatisierung.
Ausgehend von dem Gantt-Diagramm, das das Unternehmen erstellt hat, wird die Aktualisierung auf der Grundlage der getroffenen Entscheidungen und der Baumaßnahme durchgeführt, die sich sicherlich auch auf die Abläufe und Termine auswirken.
Der nächste Schritt ist die Abnahme des FAT (Factory Acceptance Test) mit einer von allen Lieferanten erstellten Dokumentation. Dies ist die Prüfung von Geräten und Komponenten vor der Auslieferung oder Endkontrolle.
Die Sicherstellung der hohen Qualität der Komponenten gewährleistet auch die Integrität innerhalb des Werks. Durch einen konventionellen Funktionstest oder eine Simulation wird festgestellt, ob die Anlage die Spezifikationen und vertraglichen Verpflichtungen erfüllt. Dabei werden Dokumente wie Handbücher und alle Arten von Anweisungen, Konstruktionen, Zeichnungen, Leitungsplänen und Instrumenten geprüft.
Dies gilt auch für automatische vertikale Lagersysteme, die z. B. über eine Bedienungsanleitung, eine Wartungsanleitung, eine Konformitätserklärung und weitere Dokumente verfügen, z. B. bei Garantien oder TÜV-Zertifikaten.
Diese Dokumente sind z. B. bei regelmäßigen Inspektionen sowohl auf der Baustelle als auch danach unerlässlich.
Es ist sehr wichtig, einen Projektleiter zu haben, der alle Phasen der Projektumsetzung verfolgt, denn die Überwachung der Arbeit der Lieferanten und die Überwachung der Inbetriebnahme ist von grundlegender Bedeutung. Gar bis hin zur Phase der Abnahmeprüfung SAT (Site Acceptance Test), in der das System gemäß Testplänen und technischen Spezifikationen getestet wird. Es soll zeigen, dass das System korrekt installiert ist und es Schnittstellen zu anderen Systemen und Peripheriegeräten innerhalb seiner Arbeitsumgebung aufweist.
Im Falle des automatischen Lagers endet diese Phase mit der Installations- und Testphase der WMS-Software und deren möglicher Anbindung an das ERP des Unternehmens.
Diese Phase endet mit dem Übergabedokument.
Ideen für die Umstrukturierung des Lagers
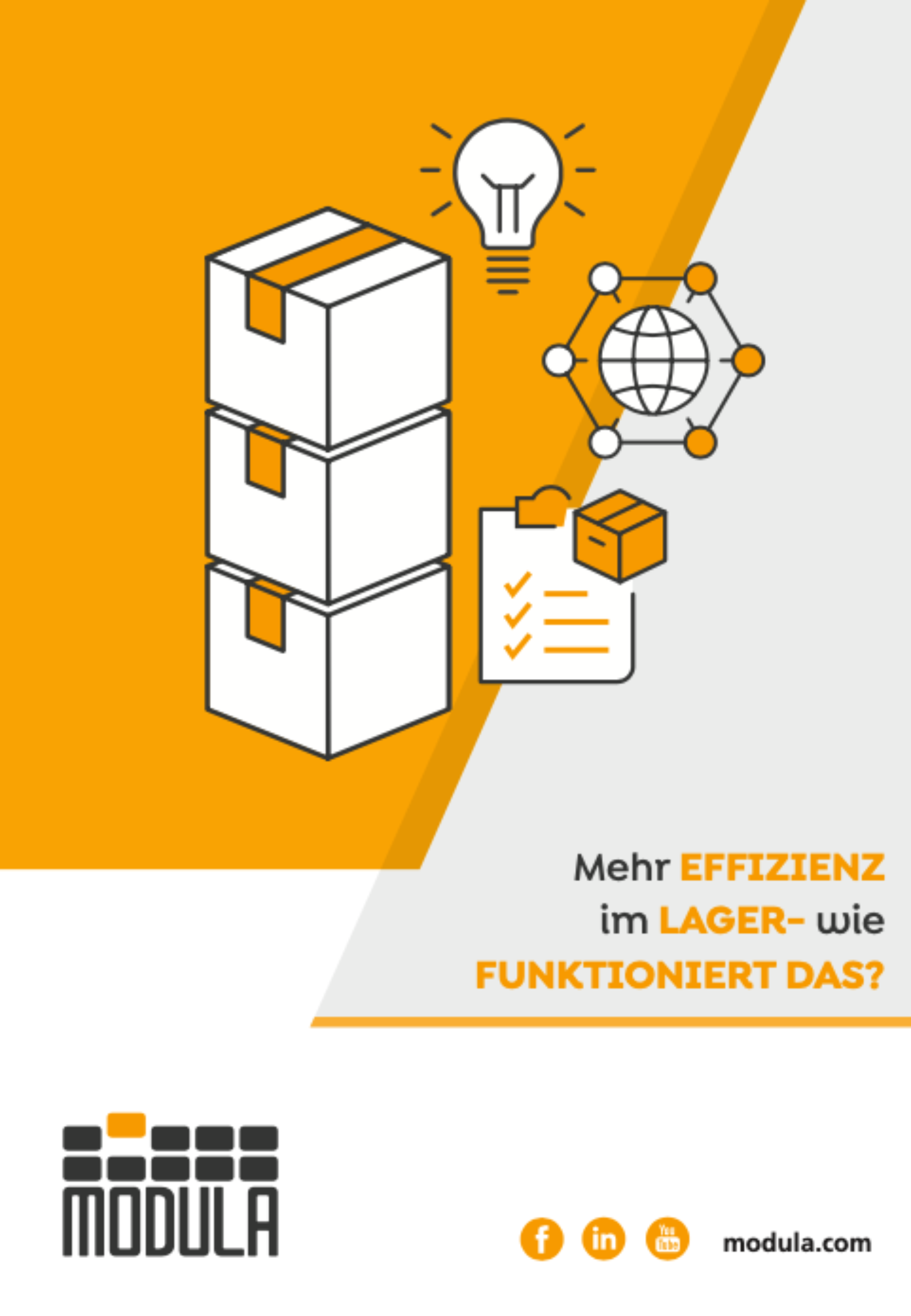