Tanto si se trata de eliminar los desperdicios mediante la supresión de procesos de almacén engorrosos como si se trata de garantizar la seguridad de los trabajadores, lean warehousing es la solución a varios retos en la gestión de almacenes.
Te explicaremos todo lo que necesita saber sobre lean warehousing, desde las ventajas y los principios hasta las mejores prácticas.
Además, te presentaremos nuestras avanzadas soluciones de almacenamiento automatizado y nuestros sistemas de gestión de inventario Modula para ayudarte a aplicar el enfoque Lean en tu almacén.
Como conseguir un enfoque lean en el almacén con la automatización.
¿Qué es lean warehousing?
El lean warehousing es un enfoque de la gestión de almacenes que elimina los procesos o las actividades que utilizan recursos pero no crean valor adicional, para reducir los desperdicios y mejorar la productividad.
Este concepto inicialmente fue desarrollado por Toyota en la industria manufacturera – en el sector del automóvil – con el objetivo de reducir los desperdicios y mejorar la eficiencia.
Tomemos como ejemplo un proceso de picking manual. La recogida manual requiere que los operarios del almacén utilicen listas de picking y naveguen manualmente por las ubicaciones de picking, lo que puede considerarse un despilfarro, ya que utiliza recursos como tiempo y mano de obra pero no añade ningún valor para el cliente.
Para resolver el despilfarro de recursos que supone el picking manual, aplicar el concepto de lean warehousing en esta situación podría significar aprovechar las soluciones de picking automatizadas.
Ventajas del Lean Warehousing
El Lean Warehousing puede ayudar a la empresa a reducir los desperdicios, eliminar procesos innecesarios y aumentar la productividad y eficacia de los operarios en el almacén.
Principales ventajas del lean warehousing.
- Mejora de la productividad. El Lean Warehousing se centra en eliminar los procesos de almacén que generan despilfarro, como la sobreproducción y el exceso de existencias. Mediante la identificación y la eliminación de las actividades sin valor añadido, se mejora la productividad.
- Aumento de la seguridad de los trabajadores. El lean warehousing da prioridad a la seguridad en el lugar de trabajo utilizando la automatización del almacén para eliminar la necesidad de llegar a lugares altos y bajos, reduciendo tanto el desorden como las prácticas de trabajo inseguras.
- Aumento de la moral de los empleados. Los principios Lean promueven la implicación y la autonomía de los trabajadores. Implicando a los empleados en iniciativas de mejora continua, se aumentan las tasas de retención y se permite que ellos se sientan valorados y motivados para contribuir al éxito del almacén.
- Reducción del tiempo de inactividad. Mejorando los procesos del almacén, se reducen los tiempos de inactividad y se garantiza que las operaciones del almacén se desarrollen sin problemas.
Reducción de la necesidad de más espacio de almacenamiento. En lugar de trasladarse a instalaciones más grandes, aplicar el enfoque Lean al almacén existente permite optimizar el inventario y reducir el exceso de existencias. Esto, a su vez, permite ahorrar en los costes asociados a la ampliación del almacén o al alquiler de instalaciones de almacenamiento adicionales.
Almacén desorganizado frente a Lean Warehousing, que se caracteriza por pasillos despejados, zonas de almacenamiento organizadas y una configuración optimizada del almacén
Los principios 5S del Lean Warehousing
Los principios de las 5S son una parte fundamental de las metodologías Lean, incluido el lean warehousing.
Estos principios pueden ayudar las empresas a crear un entorno de trabajo eficiente, organizado y seguro cuando se aplican a todos los aspectos del almacén, desde su disposición hasta la forma de recoger y embalar las mercancías.
Los principios de las 5S (y sus equivalentes japoneses) incluyen:
1. Clasificar (Seiri)
El principio de clasificación establece que cada artículo del almacén debe evaluarse minuciosamente para confirmar su valor. Los objetos obsoletos, redundantes o poco utilizados deben eliminarse.
Para aplicar el principio de clasificación, es necesario eliminar todo lo que no se utiliza con regularidad y desechar los artículos innecesarios, como herramientas y equipos inutilizados.
Las existencias de baja rotación que llevan mucho tiempo paradas deben ser guardadas en un almacén separado para liberar espacio. Esto facilita a los operarios del almacén la búsqueda de los artículos que necesitan, mejorando su eficiencia.
2. Ordenar (Seiton)
El principio de puesta en orden establece que los artículos deben almacenarse en lugares específicos en función de su frecuencia de uso, garantizando que estén accesibles cuando se necesita.
Para aplicar el principio de puesta en orden, es importante organizar el inventario de modo que sea fácil encontrarlo y acceder a él.
Por ejemplo, puede aplicarse el método de análisis ABC para clasificar las mercancías en función de su valor y volumen de negocio.
Los artículos de rotación rápida (categoría A) deben almacenarse en zonas de fácil acceso, cerca de la zona de expedición, y los de rotación lenta (categoría C) en zonas de acceso menos frecuente, como las entreplantas o la esquina trasera del almacén.
3. Limpiar (Seiso)
El principio de limpieza establece que un almacén limpio y bien mantenido es crucial para fomentar la seguridad y la eficiencia.
Para aplicar el principio de limpieza es necesario:
- Establecer una rutina de limpieza regular y actividades de organización. Programar un horario para barrer, quitar el polvo y fregar el suelo, limpiar las superficies y retirar los escombros o la basura. Asignar responsabilidades a determinados operarios del almacén o contratar servicios de limpieza profesionales.
- Utilizar estantes, estanterías y cubos. Asegurarse de que los objetos se guarden de forma organizada y fácilmente accesible. Implantar sistemas de etiquetado o escáneres de códigos de barras para garantizar la rápida identificación y recuperación de las mercancías.
Optimizar la configuración del almacén. Minimizar la congestión y permitir una circulación eficaz de las mercancías. Asegurarse de que las vías de acceso estén despejadas y de que los equipos como carretillas elevadoras o transpaletas tengan rutas preestablecidas para evitar accidentes.
4. Estandarizar (Seiketsu)
El principio de estandarización establece que deben crearse y seguirse procesos, procedimientos y directrices coherentes para mantener la eficiencia.
Para aplicar el principio de estandarización es necesario:
- Documentar los procesos y procedimientos existentes en el almacén. Esto incluye flujos de trabajo, gestión de inventarios, cumplimiento de pedidos, los procesos de recepción, preparación de pedidos, embalaje y envío. Tomar nota de cualquier variación o ineficacia en estos procesos.
- Analizar los procesos documentados e identificar áreas en las que puedan establecerse mejores prácticas. Se trata de identificar las formas más eficientes y eficaces de realizar las tareas, reducir el despilfarro y mejorar la productividad general. Comparar los resultados con las normas del sector y solicitar la opinión de los empleados que participan directamente en estos procesos.
- Crear instrucciones de trabajo claras y concisas para cada tarea o proceso. Estas instrucciones deben describir los procedimientos paso a paso, los resultados esperados, las normas de calidad y las precauciones de seguridad. Las instrucciones de trabajo estandarizadas sirven como punto de referencia para que los operarios realicen sus tareas de forma coherente.
- Ofrecer formación al personal del almacén. Formar al personal sobre las instrucciones de trabajo estandarizadas recién establecidas. Asegurarse de que los operarios comprendan los procedimientos, sigan las directrices y realicen sus tareas de acuerdo con la norma.
- Utilizar señales visuales. Usar señales, etiquetas, indicadores codificados por colores o marcas en el suelo para representar visualmente los procesos estandarizados y las directrices. Estas herramientas de gestión visual ayudan al personal a identificar fácilmente los procedimientos, las ubicaciones o los materiales correctos, reduciendo los errores y fomentando el cumplimiento de la norma.
5. Mantener (Shitsuke)
El principio de mantenimiento establece que las cuatro primeras «S» (Clasificar, Ordenar, Limpiar y Estandarizar) deben mantenerse sistemáticamente para crear una cultura de mejora continua.
Para aplicar el principio de mantenimiento es necesario:
- Realizar auditorías periódicas. Identificar las áreas que necesitan mejoras y garantizar que se mantienen los estándares.
- Impartir formación continua. Reforzar constantemente la importancia de las prácticas 5S y asegurarse de que los operarios del almacén saben cómo aplicarlas.
- Reconocer a los empleados del almacén. Recompensar al personal que mantenga altos estándares para elevar su moral y su satisfacción laboral, y animar a otros operadores a seguir su ejemplo.
Los principios 5S de Lean Warehousing
Cómo implantar el Lean Warehouse Management
Una vez definidos los pasos necesarios para lograr un enfoque Lean, el siguiente paso consiste en aplicar las mejores prácticas en las operaciones diarias del almacén.
Para integrar plenamente el enfoque de Lean Warehousing es necesario:
1.Auditar los procesos del almacén
Auditar los procesos del almacén es fundamental para identificar ineficiencias y áreas que necesitan mejoras en el almacén.
- Definir los objetivos. Por ejemplo, mejorar la eficacia, reducir costes, garantizar el cumplimiento de las normas de seguridad, mejorar el servicio al cliente o determinar las necesidades de formación. Unos objetivos claros ayudan a centrarse en la auditoría.
- Realizar una lista de comprobación para la auditoría. Elaborar una lista de las áreas que deben examinarse en función de los objetivos. Esto podría incluir la gestión de inventarios, la preparación de pedidos, el embalaje y el envío, el mantenimiento de equipos, la utilización del espacio y la formación del personal.
- Reúnir datos. Utilizar diferentes métodos para recopilar información, como inspecciones físicas, entrevistas con el personal, revisión de documentación (como registros de envíos o de seguridad) y análisis de datos (como tiempos de cumplimiento de pedidos o índices de error).
- Analizar los datos. Buscar señales que indiquen un problema. Por ejemplo, si se producen frecuentes roturas de stock de determinados artículos durante una determinada temporada, esto podría indicar un stock inadecuado de artículos de rápida rotación.
- Evaluar el rendimiento. Comparar el rendimiento del almacén con los estándares del sector y/o con el rendimiento anterior para buscar áreas que necesiten mejoras.
- Dar recomendaciones. Basándose en las conclusiones, recomendar mejoras. Esto puede incluir cambios en los procedimientos, el equipamiento, la distribución del almacén o la formación del personal.
- Presentar las conclusiones. Elaborar un informe con las conclusiones y recomendaciones y presentarlo a las partes interesadas.
2.Implantar el Just-in-Time (JIT) Inventory Management
Just-in-time (JIT) es un tipo de gestión de inventarios que requiere trabajar en estrecha colaboración con los proveedores para garantizar la disponibilidad de las materias primas para la producción.
La implantación de la gestión de inventarios JIT permite aumentar la eficiencia, eliminar el exceso de existencias y reducir los costes de almacenamiento, objetivos que están en consonancia con el Lean Manufacturing.
Para implantar la gestión de inventarios JIT en el almacén es necesario:
- Recopilar datos históricos de ventas a nivel granular (por comportamiento del consumidor o SKU, por ejemplo) para obtener un esquema detallado de las características de la demanda.
- Desarrollar relaciones sólidas con los proveedores e incluirlos en el proceso de planificación. Comunicar las previsiones de demanda a los proveedores y asegurarse de que pueden cumplir sus requisitos en términos de cantidad, calidad y plazos.
- Implementar un software de gestión de inventario que active automáticamente las órdenes de compra cuando las mercancías disminuyan, de modo que no haya el riesgo de quedarse sin existencias.
- Aplicar estrictas medidas de control de calidad en las operaciones y con los proveedores para evitar productos defectuosos.
3.Formar al personal del almacén
La implantación del lean warehousing exige cambiar los procesos y reestructurar la mentalidad del personal.
La formación de los operadores del almacén es fundamental para garantizar que todos entiendan los principios de lean manufacturing y cómo ponerlos en práctica.
Para formar al personal en prácticas de lean warehousing es necesario:
- Ofrecer un programa de orientación exhaustivo a los nuevos empleados. El programa podría incluir una introducción a los principios de lean warehousing, por ejemplo, junto con una visión general de los procesos y procedimientos específicos de la empresa y una explicación clara de las funciones y responsabilidades de los empleados dentro del almacén.
- Ofrecer sesiones de formación específicas centradas en los principios y prácticas de lean warehousing, como la metodología 5S, el mapeo del flujo de valor, las técnicas de reducción de desperdicios, la gestión visual y las herramientas de resolución de problemas para la mejora continua.
- Ofrecer oportunidades de formación práctica para aplicar los conceptos Lean, como simulaciones, ejercicios de interpretación de papeles o tareas reales.
4.Utilizar la automatización de almacenes
La automatización puede mejorar significativamente la eficiencia y la precisión del almacén, características que concuerdan con el enfoque Lean.
Las soluciones de almacenamiento automatizado incluyen almacenes automáticos, sistemas de picking robotizados y sistemas de gestión de almacenes (SGA) que pueden aumentar la precisión y la velocidad de recogida.
5.Utilizar la mejora continua (método Kaizen)
El proceso Lean no termina con la aplicación de las mejoras iniciales, sino que es un proceso continuo.
Se pueden garantizar mejoras continuas celebrando reuniones periódicas de los equipos para debatir ideas u organizando eventos kaizen formales en los que se trabaje conjuntamente para resolver un problema concreto.
Cómo implantar el Lean Warehouse Management
Las soluciones automatizadas de Modula permiten optimizar el almacenamiento
Como líder en soluciones de almacenamiento automatizado y sistemas de gestión de almacenes, Modula proporciona soluciones avanzadas que pueden mejorar la productividad, la eficiencia y la precisión de la preparación de pedidos, objetivos que se alinean con el enfoque de lean warehousing.
Nuestras soluciones automatizadas incluyen:
Almacenes automáticos verticales Modula
Los almacenes automáticos verticales maximizan el espacio existente en el almacén utilizando la altura de techo disponible, aumentando la eficiencia y la capacidad.
Los almacenes automáticos verticales Modula incluyen:
- Modula Lift: Perfecto para almacenar piezas industriales y de repuesto; disponible en una amplia variedad de capacidades y tamaños.
- Modula Slim: Ideal para almacenes con espacio limitado gracias a su diseño compacto.
- Modula OnePick: Ideal para almacenes sin intervención humana, ya que está totalmente automatizado.
Nuestros almacenes automáticos verticales permiten:
- Ahorrar hasta un 90% de espacio aprovechando la altura de techo disponible
- Acelerar el procesamiento de pedidos con un rendimiento de 140 bandejas por hora
- Aumentar la velocidad de recogida a más de 300 líneas por hora
- Mejorar la seguridad de los operadores al eliminar la necesidad de alcanzar zonas altas y bajas
- Proteger las mercancías gracias a un sistema seguro y cerrado.
Carrusel Horizontal Modula HC
El Carrusel Horizontal Modula (HC) es la solución de almacenamiento automático horizontal ideal para instalaciones en las que la altura del techo es limitada.
Nuestros HC permiten:
- Modificar el espacio entre las estanterías para almacenar diferentes mercancías
- Aumentar la velocidad de recogida hasta 550 líneas por hora y operario
- Conseguir una visibilidad completa de los niveles de existencias y los pedidos
- Supervisar las operaciones de recogida en tiempo real
- Conseguir una precisión de picking casi perfecta, alcanzando el 99% con nuestros sistemas Put to Light y lectores de códigos de barras.
Soluciones de picking Modula
Las soluciones de picking de Modula reducen el tiempo de búsqueda necesario y aumentan la precisión de picking al manipular pedidos grandes o individuales.
Nuestras soluciones de picking permiten:
- Mejorar la precisión y la velocidad de preparación de pedidos mediante dispositivos luminosos que guían a los operarios hasta la ubicación correcta
- Mejorar la gestión del inventario con una visión completa de las existencias actuales y previstas
- Impulsar aún más la precisión y la eficacia cuando se combinan con nuestras avanzadas soluciones de almacenamiento automatizado.
Sistema de gestión de almacenes Modula
El Warehouse Management System (WMS) de Modula permite supervisar la ubicación y los movimientos de las existencias, ofreciendo una visión completa del inventario.
Nuestros WMS garantizan:
- Visibilidad total de las existencias
- Supervisión y seguimiento de los niveles y movimientos de las existencias
- Mejora de la precisión cuando se combinan con los almacenes automáticos Modula
Las soluciones avanzadas de almacenamiento y el sistema de gestión de almacenes de Modula permiten aplicar un enfoque Lean a las operaciones del almacén para optimizar el espacio de almacenamiento, mejorar la precisión de recogida, aumentar la productividad y eficiencia del personal.
¿Quieres saber más sobre los almacenes verticales?
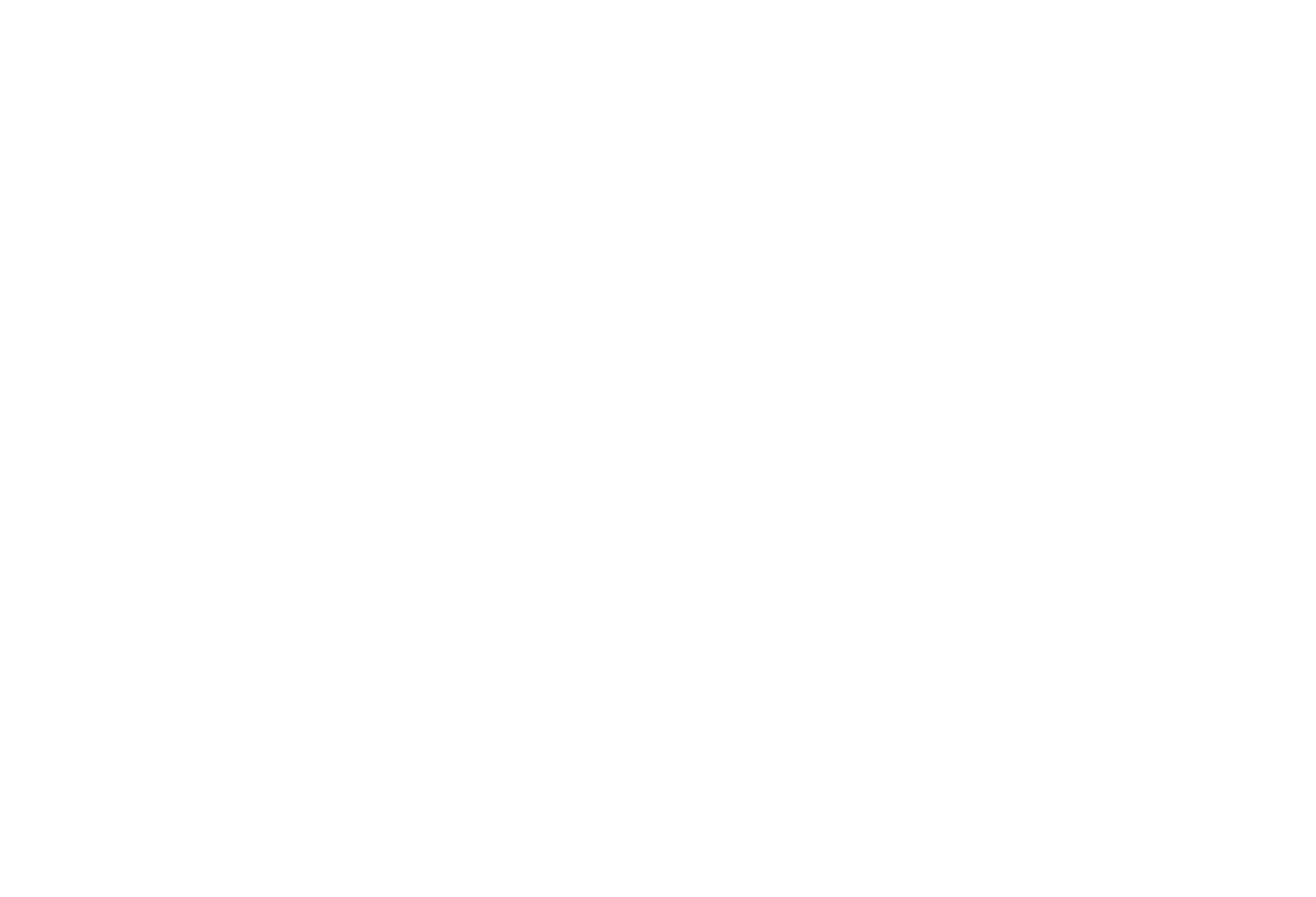