Los almacenes automáticos se han convertido en una realidad para muchas empresas y en una necesidad para muchas otras. No son todos iguales. Veamos brevemente las ventajas y desventajas de los distintos tipos de almacenes automáticos:
- Multicolumna
- Carruseles verticales
- Carruseles horizontales
- Miniload
- Trasladador-elevador
- Shuttle
- Vertical Buffer o Microload
1. Multicolumna
Por multicolumna se entiende un sistema vertical con bandejas de traslación y varias columnas para el almacenamiento y la recogida a alta frecuencia de cargas ligeras. La organización de los productos dentro de las bandejas optimiza el uso del espacio en el almacén.
Las bandejas generalmente están diseñadas para poder dividirse y adaptarse a cualquier exigencia de conservación y desplazamiento y para facilitar el flujo de las mercancías en el almacén.
Ventajas
- Tiempos de ciclo reducidos y rápido acceso a los materiales
- Optimización del flujo de material
- Alto nivel de productividad
Desventajas
- Carga útil de la bandeja inferior respecto de los VLM (almacenes automáticos verticales con bandejas)
- Tiempo medio de acceso a la bandeja superior al de un VLM
2. Carruseles verticales
Los carruseles verticales son almacenes automáticos desarrollados verticalmente y basados en el concepto de «estantes giratorios«: el carrusel se compone de una serie de estantes que giran verticalmente dentro de la máquina en ambos sentidos, llevando la mercancía almacenada a la posición de recogida siguiendo el trayecto más breve.
Este tipo de almacén aprovecha al máximo el espacio vertical y garantiza un rápido acceso a los materiales almacenados. Esta estrategia reduce considerablemente el tiempo de desplazamiento necesario con los estantes de tipo tradicional.
Ventajas
- Elevada productividad de recogida
- Optimización del espacio y reducción del espacio ocupado en el almacén
- Medidas externas muy compactas, sobre todo en profundidad: a diferencia de los VLM, no se necesita un corredor central para el elevador
- Tiempos de acceso muy rápidos y posición de recogida ergonómica
- Conservación bien organizada de componentes pequeños
- Elevada densidad de almacenamiento (superior a VLM) en máquinas de altura reducida
- Ideal para ambientes con espacio vertical limitado
Desventajas
- Capacidad de carga limitada tanto de cada estante como de la estructura en su conjunto
- Cero flexibilidad de carga. Los compartimentos son de altura fija y la altura de carga no se puede cambiar fácilmente en lo sucesivo
- No adecuado para almacenar materiales voluminosos o particularmente pesados
- La altura de la máquina no se puede modificar si la máquina cambia de posición
- Un solo punto de entrada/salida
- Las operaciones de reparación de la máquina son muy complejas y peligrosas en caso de incidente grave, a causa de posibles torsiones de los dos ejes de rotación
Existen diferentes modelos que varían según la carga útil por estante, la carga útil máxima del sistema y las medidas generales.
Características técnicas
- Carga útil máxima de los estantes: 150 – 750 kg
- Carga útil máxima del sistema: 3.000 – 14.000 kg
- Ancho máximo del carrusel: 2000 – 3420 mm
- Profundidad: 1000 – 1720 mm
3. Carruseles horizontales
Los carruseles horizontales son muy similares a los verticales, salvo por el hecho de que están dispuestos horizontalmente, por lo que el eje de rotación no es vertical sino horizontal.
Este sistema está constituido por estantes giratorios que giran en ambos sentidos y entregan el material al operador siguiendo el recorrido más breve posible. A causa del desarrollo horizontal, la posición de recogida no siempre es óptima desde el punto de vista ergonómico.
Este tipo de sistema es una buena solución cuando hay limitaciones de altura, como por ejemplo un techo bajo.
Ventajas
- Es la mejor solución cuando la altura es limitada, o en caso de espacios largos y angostos (por ejemplo, pasillos)
- Alta productividad
- Los almacenes se pueden yuxtaponer para aumentar aún más la productividad
- Disponibles algunos modelos con doble carrusel
Desventajas
- Esta solución es eficiente sólo en determinadas condiciones
- El puesto de recogida no es muy ergonómico
- Sujeto a problemas de desequilibrios de peso
- No adecuado para almacenar materiales voluminosos o particularmente pesados
Características técnicas
- Diferentes niveles de capacidad de las columnas: 450 kg, 680 kg, 900 kg
- Altura útil de las columnas giratorias: 1800 – 3650 mm
- El sistema podría verse sobrecargado
4. Miniload
El Miniload es un almacén automático de altas prestaciones, con estructura de una o dos columnas, para el desplazamiento de cargas ligeras.
Este tipo de almacén está constituido por una serie de estantes paralelos entre sí y divididos por pasillos angostos, a lo largo de los cuales se desplazan las grúas del trasladador-elevador. Las unidades de carga se almacenan en las celdas presentes dentro de la estantería. Los miniload recuperan las unidades de carga y las llevan al área dedicada a la recogida, el embalaje y el envío.
Los sistemas están equipados con una o varias bahías de carga, en base a los requisitos de recogida. La principal ventaja de estas soluciones es que aseguran un sistema de recogida completamente automático que garantiza alta productividad, velocidad y seguridad.
Ventajas
- Es posible utilizar varios tipos de unidades de carga
- Carga útil posible muy alta
- Es posible almacenar unidades muy altas utilizando todo el espacio vertical disponible dentro del almacén
- Capacidad de gestionar los paquetes
- Elevado rendimiento general
Desventajas
- Productividad limitada por la presencia de un único puesto de entrada/salida por cada canal
- Bastante costoso
- Instalación larga y costosa
- Capacidad de las unidades de carga no siempre aprovechado al 100% a causa de la forma y el tamaño de los elementos almacenados
- No adecuado para almacenar materiales voluminosos o pesados
5. Trasladador-elevador
Los almacenes con trasladador-elevador son similares a los Miniload, pero a diferencia de éstos han sido diseñados para gestionar y almacenar palets y materiales generalmente pesados.
El sistema se compone de un bastidor móvil que se desplaza a lo largo de una columna vertical que a su vez se mueve horizontalmente por un pasillo delimitado por dos estantes. Este tipo de solución automatizada se utiliza en almacenes de altura superior a 12 metros.
Ventajas
- Puede gestionar varios tipos de unidades de carga: palets, contenedores, etc.
- Puede contener materiales muy pesados y voluminosos
- Puede alcanzar grandes alturas
- Sistema totalmente automatizado
Desventajas
- Generalmente bastante lento
- No adecuado para almacenar objetos pequeños
- Bastante costoso y difícil de implementar
6. Shuttle
Un sistema automatizado con shuttle está constituido por una serie de estanterías paralelas divididas por un pasillo angosto donde cada shuttle retira el material de las posiciones de almacenamiento y lo transporta al ascensor situado en un extremo del pasillo.
Una vez que los materiales llegan al ascensor, bajan hasta el punto de recogida. El proceso inverso se produce durante la fase de reabastecimiento.
Este tipo de sistema es altamente eficiente y ofrece una productividad muy elevada. Este sistema es fácil de instalar y fácilmente expansible, ya que es posible añadir estantes, shuttles y ascensores en lo sucesivo de acuerdo con las necesidades.
Generalmente se utiliza en sinergia con otros sistemas, como los Miniload, para aumentar la productividad total del almacén.
Ventajas
- Velocidad de recogida, rendimiento muy elevado
- Fácil de instalar, fácil de expandir
- Versátil, apto para gestionar varios tipos de material
- Los shuttles alivian la carga de trabajo del trasladador-elevador en su canal; éste puede ser de diferentes medidas
Desventajas
- Altura operativa limitada
- No adecuado para desplazar productos voluminosos o pesados
7. Vertical Buffer o Microload
Es un nuevo tipo de almacén automático para el almacenamiento y la recogida de pequeños componentes ligeros.
Este tipo de almacén consiste en un sistema de estanterías que mueve automáticamente las bandejas en su interior. La verdadera novedad respecto de los Vertical Lift Modules (VLM) es el puesto de recogida: los materiales se presentan al operador sobre un plano inclinado 20°, diseñado precisamente para garantizar la máxima ergonomía al operador.
El Vertical Buffer es particularmente adecuado para almacenar materiales con baja frecuencia de desplazamiento y para recoger pequeñas cantidades de materiales diferentes, con la posibilidad de recoger hasta 4 artículos diferentes en una sola operación. El procedimiento es realmente sencillo: mientras el operador recoge un artículo, la máquina prepara el segundo pedido; una vez efectuada la primera recogida, el módulo gira la bandeja 180° para poner la segunda bandeja a disposición para la recogida.
El Microload se puede definir como un VLM de última generación con la particularidad de tener un ascensor interno que gestiona no una sola bandeja a la vez sino 4 o 5 pequeñas bandejas.
Si el operador debe preparar un pedido con 4 artículos diferentes, almacenados en 4 bandejas diferentes dentro del almacén, el VLM tradicional debe gestionar 4 operaciones de recogida diferentes, mientras que el Vertical Buffer tiene un ascensor interno que recoge las 4 bandejas y las lleva al puesto de recogida en una única operación. Esto garantiza, sin lugar a dudas, una mayor eficiencia de la instalación.
Ventajas
- Mayor velocidad de recogida, hasta 4 veces superior a la del VLM
- Almacenamiento de los componentes en cajas de tamaño estándar y fácilmente identificables
- Las bandejas se entregan en el área de recogida en posición inclinada y, por lo tanto, más ergonómica
- Posibilidad de instalar el Vertical Buffer en áreas refrigeradas hasta -20°
- Peso al suelo inferior respecto de los VLM o carruseles
Desventajas
- No adecuado para almacenar materiales voluminosos o pesados
- Carga máxima por bandeja pequeña 25 kg
- Peso máximo por ascensor 125 kg
- Carga útil máxima de la máquina 40.000 kg – estructura muy ligera
8 tipos de desperdicios que los almacenes automáticos verticales Modula pueden eliminar
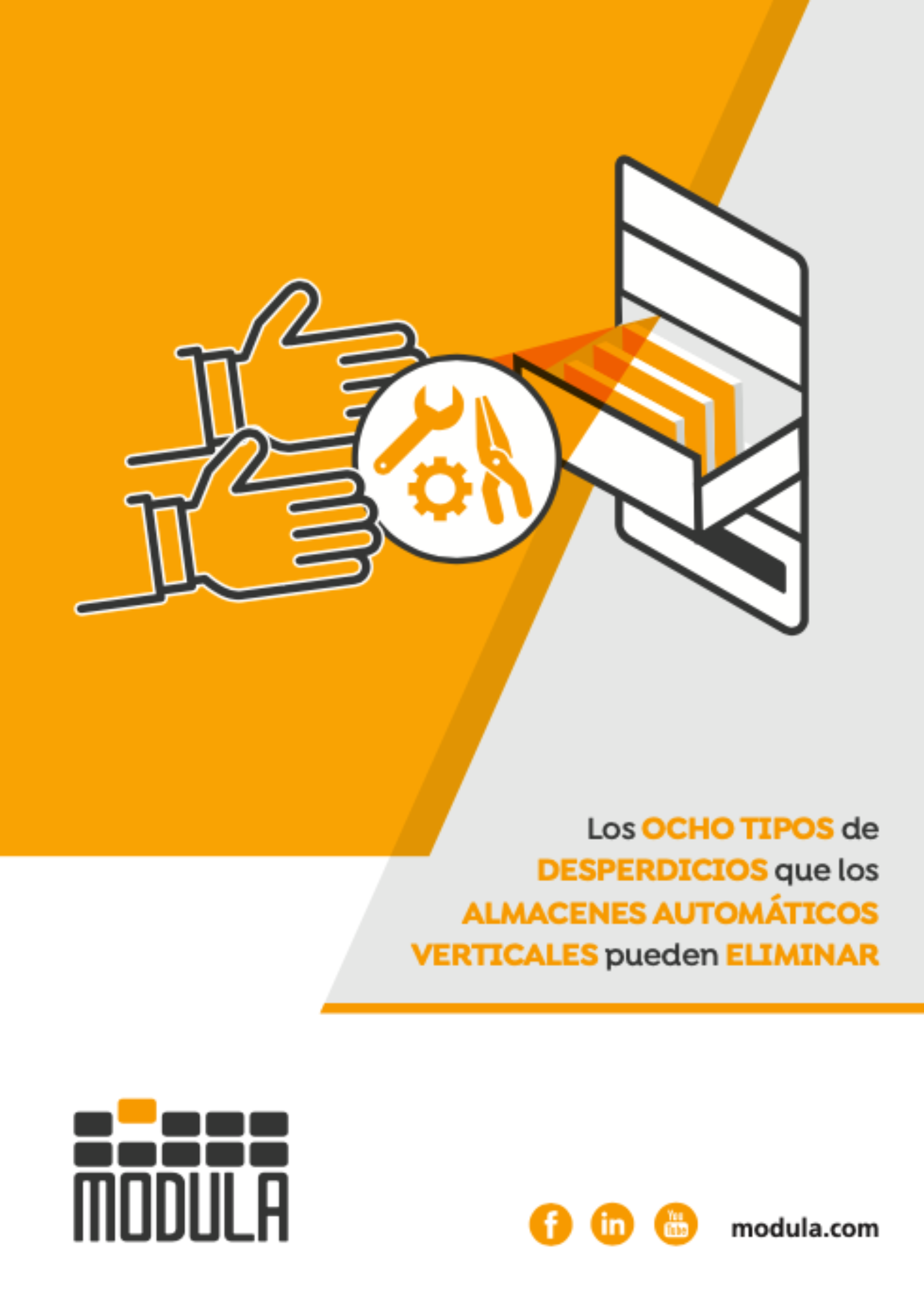