Una cadena de suministro eficaz y eficiente necesita una planificación minuciosa y atenta desde el principio. Al tratarse de un proceso muy complejo que incluye una gran variedad de recursos que hay que organizar, cualquier cambio puede traer consigo situaciones críticas que comprometan el éxito de todo el proceso de la cadena de distribución.
Los cambios globales como el que hemos vivido a principios de año no pueden no tener consecuencias sobre la gestión de la cadena de suministro de una empresa. Este periodo, así como otros en el pasado, ha cambiado los hábitos de los consumidores finales, y se exige a las empresas que sean capaces de adaptarse a las novedades con la suficiente rapidez como para no perder la confianza de estos últimos y de todos los trabajadores.
Ante un cambio radical, ¿cómo pueden las empresas no solo sobrevivir, sino incluso dirigir el cambio y obtener oportunidades de mejora?
El factor clave del éxito es la capacidad de la empresa para pasar de una estrategia exclusivamente lean a una estrategia agile: rediseñar la cadena de suministro siguiendo nuevas lógicas que minimicen los riesgos, aprovechando todos los enfoques innovadores que el sector de la logística ha venido proponiendo en los últimos años.
Palabra clave: rediseñar la cadena de suministro de una forma flexible y resiliente.
La estrategia agile: cómo gestionar el riesgo de una forma más rápida y flexible
Partimos de la premisa de que la empresa ya tiene procesos bien definidos y que está dispuesta a remodelarlos para satisfacer las necesidades surgidas de los problemas detectados sobre el terreno (factores internos) o de las crisis económicas y/o sociales (factores externos).
Uno de los primeros pasos que se deberá dar será la comunicación transparente con todos los participantes de la cadena, requisito fundamental para la planificación estratégica de toda la producción. Precisamente porque la cadena de suministro la componen diversos participantes, para hacer frente a cualquier cambio repentino es fundamental comunicarse rápidamente con todos ellos a fin de reprogramar los procesos en el menor tiempo posible. Y esto únicamente es posible si hay un intercambio claro de información a lo largo de toda la cadena.
En segundo lugar, se deberá cambiar la estrategia y pasar de la clásica caracterizada por la máxima eficiencia a la moderna basada en la maleabilidad. Esto será posible acercándose a los pilares de la Industria 4.0 como el Internet de las cosas (IoT, Internet of Things) y los Big Data.
Gracias a la aplicación del Internet de las cosas, una empresa puede disponer fácilmente de información sobre la trazabilidad de los productos y procesar en tiempo real información sobre la distribución, la venta o el ajuste de los precios de las materias primas. Conectar las máquinas y las instalaciones industriales con el Internet de las cosas es un reto que logrará modificar completamente todo el proceso productivo a medio plazo. Un hipotético funcionamiento de la estrategia basado en el IoT de una empresa totalmente automatizada (es decir, equipada, por ejemplo, con máquinas de transferencia, robots inteligentes, almacenes automáticos verticales) y que utiliza el principio logístico del sistema DIO (Direct Input/Output System), podrá conectar entre sí todas las zonas principales: oficinas, producción, almacenes automáticos y la zona destinada al público.
En este caso, las tecnologías verticales serán el eje central de todo el sistema: a través del software de gestión del almacén, se ocuparán de la relación de los distintos bloques, gestionando los movimientos de las personas y mercancías. Todo esto conducirá a una mejora considerable de la cadena si todos los socios y proveedores que forman parte de ella participan de una manera orgánica e integrada.
El Big Data, por su parte, ayuda a identificar, localizar y monitorizar las tendencias al alza y a la baja de la demanda. Solo la interconexión y el intercambio de datos permite tener acceso a estos datos y a estos recursos, en beneficio de todos, lo que es contrario al principio de posesión de la información, que siempre se ha considerado una fuente de poder.
La vuelta a las existencias proactivas para una logística resiliente
La gestión eficiente del inventario y del abastecimiento de la mercancía ayuda a reducir los costes, mejorar la satisfacción de cliente y aumentar la productividad de cada realidad industrial.
La cosa verdaderamente importante es transformar los datos obtenidos de los estudios en una respuesta rápida y eficaz para mejorar la intralogística. Hacer pronósticos fiables es difícil incluso para las empresas mejor gestionadas. La alternativa real es la de asignar un mínimo de existencias de tal forma que se pueda hacer frente a la incertidumbre de las previsiones incluso en caso de bloqueo por parte de algunos proveedores.
¿Cuáles son los pasos para diseñar una cadena de suministro resiliente?
- Comprender y analizar vuestra intralogística
- Mapear los procesos con los proveedores y los clientes
- Localizar los riesgos
- Gestionar los riesgos
- Adoptar una estrategia agile y no solo lean
- Automatizar
¿Qué hacer exactamente para cambiar la estrategia?
En primer lugar, hay que pasar de una relación de confrontación a una relación de colaboración con los clientes y los proveedores. Para ello, la visibilidad y la transparencia son fundamentales: nunca se debe mentir sobre la disponibilidad de un determinado producto o confirmar envíos que nunca se podrán respetar, solo para evitar que el cliente cambie de proveedor.
Pero, por encima de todo, es importante adoptar sistemas de automatización 4.0 capaces de proteger a las personas que trabajan para nosotros y compran con nosotros, así como el entorno en el que vivimos y trabajamos.
La automatización juega y jugará cada vez más un papel estratégico a la hora de afrontar las situaciones de emergencia, pero también en la gestión cotidiana.
Por ejemplo, en el caso de los almacenes automáticos verticales, el operador podrá permanecer en una ubicación fija y realizar el picking sin tener que desplazarse o interactuar con otros compañeros. La distancia social estará asegurada, ya que la anchura mínima de una bandeja es de 1,3 metros.
Las ventajas de la automatización: los almacenes automáticos verticales
No es casualidad que en los últimos 10 años la automatización haya sido una tendencia al alza. Concretamente en el almacén, gracias a la automatización se está pasando del concepto «hombre a la mercancía» al de «mercancía al hombre», dejando patentes desde el principio numerosas ventajas. Son muchas las soluciones automatizadas disponibles para el almacenamiento y la recogida automática en el almacén, pero las que se adaptan mejor a cualquier realidad productiva son los almacenes automáticos verticales.
Sus ventajas más evidentes son:
- Aumento de la productividad y de la eficiencia
- Disminución de los errores en la fase de picking
- Disminución de los costes de producción
Al incorporar a los almacenes automáticos los sistemas de ayuda al picking, estos guiarán a los operadores en la selección de los productos correctos reduciendo considerablemente los márgenes de error y los tiempos de preparación de los pedidos. El doble muelle también está diseñado para mejorar la eficiencia: mientras una bandeja está en el muelle para el picking, el elevador está preparando otro para el siguiente. Esto garantizará un aumento de la productividad y una eficiencia cada vez mayor en el interior del almacén.
El picking automatizado, el aliado perfecto para una logística agile
La transparencia y la comunicación deben ayudar a los encargados de la cadena de suministro a optimizar todos los procesos de la logística, especialmente la gestión del almacén y todas las actividades relacionadas.
El picking, en concreto, es el corazón del almacén y precisamente por eso una de las prioridades cuando se hay que optimizar los procesos. Se trata de la actividad del almacén encargada de recoger la mercancía de las estanterías, de los palés o simplemente de las zonas destinadas al almacenamiento del material.
Robots antropomorfos, robots móviles autónomos y cobots: son todos sistemas capaces de mejorar y automatizar la fase de picking. Sin embargo, los beneficios más grandes se obtienen cuando se instalan de manera combinada, por ejemplo, con los almacenes automáticos verticales, porque hacen que todo el proceso sea agile: la recogida y depósito de los productos y el desplazamiento en el interior del almacén.
Un picking automático logra unos niveles de velocidad y eficiencia que el picking manual nunca podrá igualar. Es cierto que existen formas de mejorar el picking manual, pero los sistemas automáticos tienen un rendimiento mejor, sobre todo en situaciones en las que gestionan muchos códigos y es necesario trabajar con rapidez y sin cometer errores (especialmente cuando los pedidos se concentran en franjas horarias muy concretas).
8 tipos de desperdicios que los almacenes automáticos verticales Modula pueden eliminar
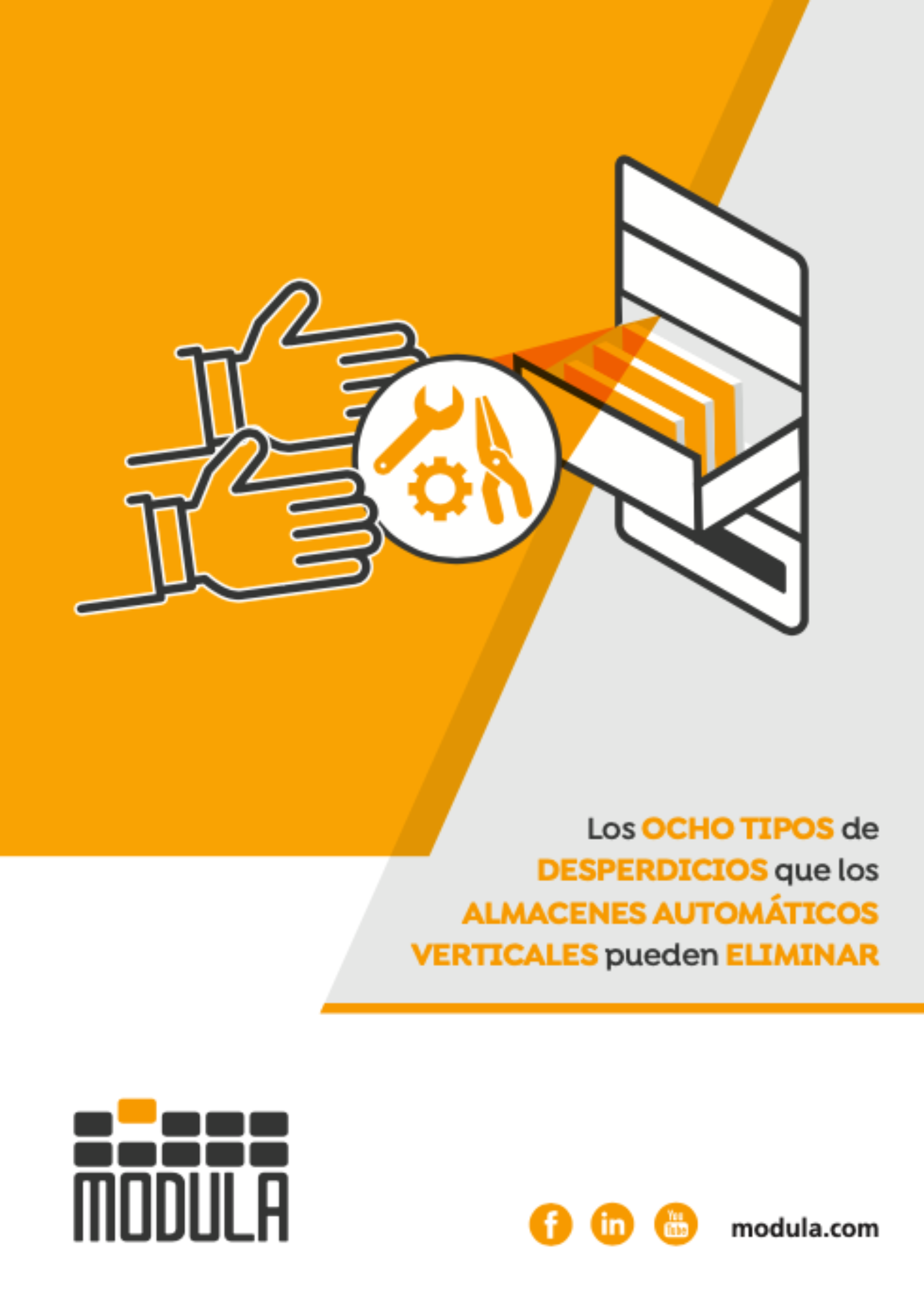