Una buena organización del almacén es fundamental para el éxito de la estrategia de la empresa y puede constituir una ventaja competitiva a largo plazo. El objetivo de la gestión es optimizar principalmente tres aspectos para garantizar la máxima accesibilidad a cada artículo y reducir los costes administrativos:
- Uso del espacio
- Uso de los equipos
- Gestión de los recursos humanos
Una organización eficaz del almacén permitirá a cada operador conseguir inmediatamente el artículo deseado y proceder a la preparación del pedido rápidamente y sin errores, aumentando de esta manera la satisfacción de los clientes y optimizando los plazos de preparación y entrega de los pedidos.
El modelo de asignación y el sistema de identificación de las mercancías determinan el resultado organizativo.
1. ¿Cómo se optimiza el espacio del almacén?
El espacio dedicado al almacén es parte integrante de los procesos de producción y venta, por lo que tiene un valor económico ligado a las infraestructuras, a los recursos dedicados y al capital invertido, por lo tanto es necesario gestionarlo lo mejor posible para limitar los costes.
El reto principal es la optimización del stock. Directamente relacionada con la complejidad de la cadena de suministro y la fluctuación de la demanda, comprende todas las actividades que apuntan a maximizar el retorno financiero de las existencias para la empresa y tiene como punto de partida el inventario de la mercancía en almacén. El primer paso para una organización eficaz y eficiente del almacén en términos de espacio, y que tiene efectos en todo el sistema organizativo, es saber todo lo que se debe almacenar. Mediante la confrontación del inventario y el estudio de las características de la demanda y de los volúmenes de movimiento de las mercancías, es posible determinar los niveles totales de producto almacenado y su posición en el almacén.
Generalmente la gestión de almacén actual se complementa con un software de gestión de almacén que facilita la optimización con una representación electrónica del espacio utilizado, construido sobre la base de datos de la mercancía. El software permite acciones de picking muy veloces porque reduce a cero las búsquedas tradicionales por parte de los operadores. Para mantener totalmente bajo control la gestión de las existencias se recomienda el seguimiento de todas las operaciones, que asegurará la mayor precisión posible de los datos.
Para facilitar la introducción en la base de datos de toda la mercancía y simplificar su gestión, es necesario determinar el código SKU de cada unidad a almacenar. Se trata de un identificador unívoco de producto, un código que generalmente identifica diferentes versiones del mismo producto. A partir de los SKU, de los volúmenes totales, del estudio de los ciclos de carga/descarga, se determinan los criterios con los cuales almacenar la mercancía en función del espacio disponible, siguiendo el modelo más adecuado para la empresa, para las tecnologías existentes y para los sistemas de desplazamiento utilizados, aumentando el rendimiento superficial (informe que indica la superficie de almacén ocupada por la mercancía en relación con la superficie total a disposición).
2. ¿Cuáles son los modelos de gestión tradicional del almacén?
Según las unidades de carga a almacenar, ya sean palets o piezas pequeñas, las infraestructuras más utilizadas en la organización de la mercancía suelen ser seis. Para optimizar efectivamente los espacios, cada tipo de almacén se debe analizar teniendo en cuenta el tipo de mercancía que se debe guardar (obsolescencia, rotación, etc.).
Almacén apilado
Es el tipo de almacén más sencillo, prevé el apilado de la mercancía. Las unidades de carga se apilan dejando un espacio adecuado para el desplazamiento de los palets mediante horquillas o carretillas.
Si la mercancía no es perecedera y no es necesaria la ventilación de los palets, este modelo permite optimizar la superficie utilizada y garantizar un alto nivel de saturación del almacén.
Almacén con estanterías convencionales
Adecuado para productos no apilables, permite depositar las unidades de carga sobre estantes que permiten la máxima selectividad. La altura de los estantes depende directamente de la altura de la infraestructura, mientras que la disposición varía según el medio utilizado para el desplazamiento de la mercancía; de acuerdo con esto se establece el ancho de los pasillos de acceso que delimitan el rendimiento superficial. Es un modelo que por su naturaleza no permite optimizar los espacios y los tiempos.
Almacén drive in y drive through
El sistema prevé el uso de estructuras constituidas por repisas donde se apoyan los palets que permiten a las carretillas entrar en la estructura. Adecuados para mercancías no apilables, con un número limitado de referencias de producto pero con un alto número de palets por cada referencia. El método drive through permite tener un lado para el almacenamiento y otro para el picking. Es necesario evaluar si el espacio a disposición lo permite, si las acciones de almacenamiento y picking deben ser simultáneas, y qué lógica elegir entre LIFO (Last In First Out) y FIFO (First In First Out).
Almacén con cantilever
Adecuado para almacenar mercancías voluminosas y de formas no estándar, permite el almacenamiento en altura, con consiguiente ahorro de superficie.
Almacén compacto
A diferencia de los anteriores, el almacén compacto elimina los pasillos maximizando el índice volumétrico y el rendimiento superficial, solo si se logra organizar las mercancías según la frecuencia y el orden de picking; en caso contrario, se pierde mucho tiempo para la apertura de los pasillos.
Estanterías convencionales y cajoneras para piezas pequeñas
Cuando se necesita almacenar unidades de carga de tamaño pequeño, los métodos tradicionales de organización prevén el uso de estanterías o cajoneras para almacenaje y un encargado del picking. Para aprovechar al máximo el espacio disponible, los productos se almacenan según el orden de picking y el tamaño, para utilizar todas las cajoneras o estanterías tradicionales y evitar huecos vacíos.
Si desea más información: Las desventajas de los almacenes tradicionales: por qué no elegirlos.
3. Modelos de gestión automatizada del almacén
La automatización del almacén es un tema candente cuando se habla de logística y optimización del espacio; es un error considerarla la única solución para muchos problemas de la empresa. La adopción de sistemas avanzados de gestión automática de almacén puede indudablemente aportar muchos beneficios, pero no sin un cambio organizativo para integrar las nuevas sinergias hombre-máquina.
Almacenes automáticos con dispositivos elevadores y trasladadores
Se trata de almacenes automáticos para palets y volquetes, compuestos por estanterías con espacios intermedios suficientemente anchos para hacer pasar los dispositivos elevadores y trasladadores que se desplazan a lo largo de los pasillos del almacén. El sistema es gestionado mediante un software central que guía sobre rieles el dispositivo elevador y trasladador, el cual efectúa la acción de picking incluso a alturas muy elevadas.
Para el almacenamiento de piezas pequeñas, accesorios, productos de tamaño pequeño y mediano, el dispositivo elevador y trasladador se identifica más precisamente con el término Miniload; en este caso las UdC (unidades de carga) suelen ser bandejas.
¿Cómo funciona el almacén automático con dispositivo elevador y trasladador?
El ordenador conectado registra el pedido y localiza automáticamente la posición del producto, que es recogido por el elevador, siguiendo una lógica de picking «mercancía a hombre».
Este tipo de almacén permite reducir los tiempos de gestión, gracias al picking automática, y también el espacio, porque los dispositivos elevadores y trasladadores se adaptan a pasillos muy estrechos entre las estanterías. El operador no necesita buscar el producto ni recogerlo con la carretilla elevadora, acción que requeriría mucho más tiempo y un espacio de movimiento superior entre las estanterías, en comparación con el sistema automático.
Cada vez que se decide la disposición de las mercancías dentro del almacén, lo primero que hay que hacer es definir la unidad de carga, incluso si se ha optado por un almacén automático. En este tipo de almacén, la mercancía se guarda y se retira por unidad de carga entera (palet o bandeja). Si se requiere un retiro de tipo uno a uno, el almacén automático más eficaz para ahorrar tiempo y espacio será el siguiente.
Almacén automático vertical con bandejas
El Vertical Lift Module (VLM) está constituido por un único bloque vertical y bandejas que se trasladan en su interior. Es la solución ideal cuando se necesita almacenar mucha mercancía pero el espacio disponible es más vertical que horizontal. Este tipo de almacén es adecuado para almacenar todo tipo de material, a granel o empaquetado, y de diferentes tamaños, ya que permite una gestión dinámica de las alturas de carga. Para un ahorro aún más eficaz se recomienda aprovechar bien las bandejas depositando mercancías de tamaño similar, con el fin de reducir al mínimo el desperdicio de espacio.
Las dos variables principales a la hora de decidir si comprar o no un almacén automático vertical con bandejas son las siguientes:
- El tamaño: es posible almacenar mercancías voluminosas, pero si el objetivo es ahorrar espacio, la disposición del material debe ser muy precisa
- El peso: averiguar previamente la capacidad de cada bandeja
La optimización no necesariamente se logra adquiriendo nuevos espacios o aumentando los recursos dedicados sino aprovechando al máximo todo el capital (físico o no) a disposición y haciendo un balance de las necesidades, el tipo de operaciones a desarrollar en el almacén y las previsiones de demanda.
Si desea más información: ¿Cuál es la mejor gestión de los almacenes? ¡La automatización!
4. Diferencias entre los modelos de gestión automatizada
Existen distintas soluciones de gestión automatizada del almacén; además de las ya citadas, recordamos los carruseles (horizontales y verticales) y los almacenes multicolumna. Son todos sistemas que permiten gestionar el almacén de manera más eficiente y ahorrar espacio respecto de las soluciones tradicionales.
Un determinado tipo de almacén automático puede no servir para todos los casos. Analicemos los diferentes tipos según las siguientes variables: velocidad de picking, ahorro de espacio, número máximo de SKU.
- Velocidad de picking: los carruseles y almacenes verticales con bandejas (VLM) son los dos tipos de almacén automático que optimizan los tiempos de elaboración. Para acortar todavía más los tiempos es posible colocar varias máquinas cercanas entre sí de modo que el operador no se vea obligado a trabajar sólo con un almacén y pueda agilizar aún más la acción de picking. Por otra parte, los miniload y los sistemas de stacker crane ofrecen una capacidad inferior, ya que el dispositivo elevador y trasladador constituye un cuello de botella.
- Footprint: relación entre el espacio utilizado y la cantidad total de material almacenado. Los factores que influyen en el resultado son la altura máxima operativa del sistema y la densidad de almacenamiento. Los VLM ofrecen las mejores prestaciones porque las bandejas se pueden desplazar dentro de la máquina y esto reduce al mínimo el espacio utilizado. Los carruseles horizontales y los CarryPick son los tipos menos indicados si se desea ahorrar todo el espacio posible, dada su baja altura operativa.
- Número máximo de SKU: el número máximo de SKU gestionados depende en gran medida del criterio anterior. Para todos los sistemas con límites estructurales de expansión, como carruseles, VLM, multicolumna y módulos verticales, existe un límite.
- Flexibilidad: si se busca la máxima flexibilidad de almacenamiento, la solución ideal son los almacenes automáticos verticales con bandejas (VLM), gracias a la organización automática de las bandejas dentro del almacén en base a los productos almacenados.
- Ergonomía: para la ergonomía se deben considerar la distancia que el operador debe recorrer y la facilidad y comodidad de las operaciones de recogida. Todos los sistemas analizados tienen niveles de ergonomía similares, con solo dos excepciones. Por un lado, los carruseles horizontales son los menos ergonómicos, porque no todas las unidades de almacenamiento son fáciles de alcanzar para el operador. Por otro lado, el diseño del módulo vertical Bu er ha sido desarrollado expresamente por su ergonomía y es la mejor solución basada en este criterio.
Si desea más información: Comparación entre los almacenes automáticos: diferencias, ventajas y desventajas.
Las ventajas de un sistema de almacenamiento vertical automático Modula
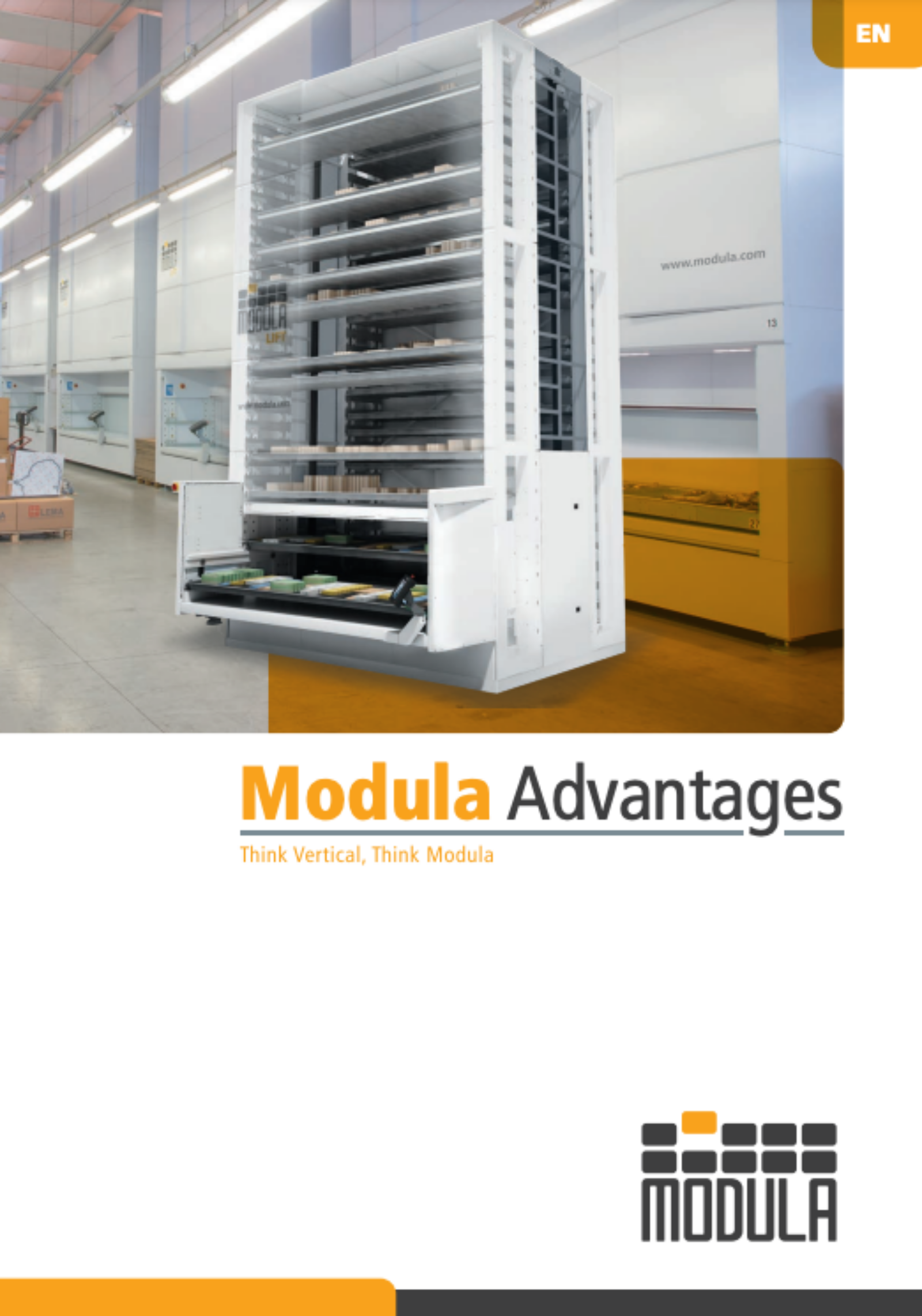