La logística del frío (en inglés cold supply chain) se refiere a una cadena de suministro a temperatura controlada que comprende las instalaciones de:
- Producción
- Almacenamiento
- Distribución
Cada una de estas instalaciones debe disponer de equipos que mantengan una temperatura constante dentro del rango requerido para que los materiales o los productos procesados y distribuidos no se contaminen ni deterioren.
La cadena de frío es, por tanto, uno de los procesos de gestión logística más complejos -y, por tanto, también más costosos- y se utiliza en sectores sensibles a la temperatura, como el alimentario, el farmacéutico, el electrónico, el de la floricultura y el del cuero.
Debido a la naturaleza de los productos, la gestión de la logística del frío presenta problemas peculiares que la diferencian de la gestión de la cadena de suministro tradicional. Un ejemplo serían las vacunas, ya que requieren una temperatura casi exacta en toda la cadena de suministro, desde la producción hasta el uso. No mantener el rango exacto, incluso durante un corto periodo de tiempo a lo largo de la cadena, significa comprometer la seguridad y la eficiencia y, por lo tanto, hacer que la vacuna sea inutilizable.
Los 3 principales problemas de la cadena de frío
Los principales problemas de la cadena de frío surgen de la necesidad de mantener una temperatura constante durante las actividades de preparación, almacenamiento y transporte para garantizar la calidad y la seguridad de los productos perecederos y sensibles a la temperatura. Estas son los 3 principales que se derivan del factor temperatura y que tienen un impacto económico.
1) Costes elevados para el control de la temperatura
Algunos sectores en los que se utiliza la logística del frío tienen un impacto directo en la salud de las personas (pensemos en la industria agroalimentaria y farmacéutica) y por ello las exigencias de control de la temperatura son estrictas y están reguladas para todas las etapas de la cadena de frío.
La referencia en Europa es el Reglamento CE 37/2005, que obliga a medir y registrar la temperatura a intervalos regulares tanto en los medios de transporte como en los lugares de almacenamiento. Esto significa que tanto los medios de transporte como los almacenes deben contar con instrumentos adecuados para garantizar la temperatura segura del producto y medirla a lo largo del tiempo.
Algunos ejemplos de estas herramientas específicas y de las importantes inversiones necesarias para la logística del frío -hasta cinco veces más elevadas que las requeridas para el transporte y almacenamiento de productos secos- son las cámaras frigoríficas, el aislamiento de los edificios, los sensores de control de temperatura y el transporte en frigoríficos. También hay que tener en cuenta los costes de electricidad para el funcionamiento del sistema de refrigeración.
2) Riesgo de contaminación y deterioro
La contaminación o el deterioro de los productos que requieren control de la temperatura tiene enormes implicaciones económicas para una empresa. Un ejemplo puede ser el sector alimentario, en el que, debido a la difusión masiva de la gran distribución y el comercio electrónico, se utiliza cada vez más la cadena de frío. Los productos alimentarios son altamente perecederos y son susceptibles de propagación de hongos, bacterias y crecimiento microbiano si no se manipulan y gestionan adecuadamente. Las normas dictadas por el sistema HACCP también deben respetarse en la logística.
Los costes relacionados con el deterioro del material son tanto directos como indirectos y pueden producirse a lo largo de toda la cadena de suministro, pero conllevan mayores costes si se producen en la fase de almacenamiento, el único eslabón de la cadena logística en el que se reduce la temperatura.
En caso de que los productos se contaminen o perezcan, supondrían:
- Costes relacionados con la eliminación de productos inutilizables
- Costes de revisión de la calidad
- Costes de reposición
Los costes indirectos pueden ser:
- Pérdida de reputación y confianza
- Pérdida de cuota de mercado
- Posibles litigios por daños causados por las mercancías
Para reducir el riesgo de contaminación y degradación del producto -y evitar así los costes relacionados- es muy importante aplicar todas las medidas de control de la temperatura y utilizar soluciones tecnológicas que apoyen la cadena de frío.
3) Tiempos de picking
Estrechamente relacionado con el riesgo de seguridad del punto anterior, los tiempos de picking en la logística del frío deben reducirse al mínimo para garantizar la integridad de los productos manipulados. El picking es, de hecho, un momento crítico, ya que el producto o la mercancía se detiene fuera del entorno climatizado y este lapso de tiempo debe reducirse para garantizar la seguridad y la integridad.
Cuando se diseña un sistema de gestión de almacenes con productos perecederos, no se puede evitar aplicar estrategias de picking y utilizar herramientas de automatización que minimicen el tiempo de permanencia fuera del entorno refrigerado.
Soluciones para limitar los costes de la cadena de frío
Aunque los costes asociados a la logística de la cadena de frío, así como su gestión incorrecta, son muy elevados, también es cierto que es posible que una empresa haga uso de procesos y soluciones tecnológicas para limitar significativamente los costes, optimizar la organización y reducir los riesgos asociados.
Estas soluciones pueden utilizarse en estas etapas de la cadena de suministro:
- Producción
- Almacenamiento
- Carga de mercancía
- Transporte
- Descarga en el CeDi o en los puntos de venta
La recogida, el almacenamiento y el transporte hasta el consumidor final quedan fuera del control de la empresa, a menos que se trate de comercio electrónico.
Automatización de la fase de picking
Además de ser una etapa crítica para la seguridad, el picking es también un momento en el que no siempre es posible la participación de los operarios (pensemos en los almacenes de productos congelados, donde las temperaturas pueden llegar a ser de hasta -30 grados).
Tanto para evitar los choques de temperatura de los productos como para agilizar los tiempos y evitar el deterioro, los modernos centros de logística del frío utilizan robots antropomórficos para automatizar el picking. La lógica aplicada es, pues, la de la mercancía al hombre, aprovechando también la reciente tecnología de voice picking que permite al operador dar órdenes y recibirlas en un auricular.
El ahorro de costes se debe a una recogida más rápida y a la capacidad de los robots antropomórficos de detectar automáticamente el estado de los productos, detectando criticidades.
Utilización de almacenes automáticos y verticales de temperatura controlada
La refrigeración de un almacén cuesta dinero, sobre todo en términos de energía. Por ello, es conveniente aprovechar al máximo la superficie disponible para reducir los costes energéticos.
La solución a este problema son los almacenes verticales que permiten ahorrar hasta el 90% del espacio de almacenamiento disponible. Los almacenes automáticos Modula Lift Climate Control también permiten controlar la temperatura en un rango de +2 a +25 grados, combinando las ventajas del almacenamiento vertical con una ingeniería que garantiza la temperatura y la humedad para un almacenamiento seguro.
Un almacén automático también reduce los costes de dispersión de la temperatura al automatizar la recogida y el almacenamiento.
Soluciones de manipulación automatizada en cámaras frigoríficas
En los almacenes de temperatura controlada, donde las temperaturas de almacenamiento son bajas, se utilizan cada vez más sistemas automáticos de manipulación de mercancías, que reducen el tiempo que los operarios pasan en estas zonas. Un ejemplo son los transelevadores de palés y las lanzaderas de palés, que se guían por un software remoto y realizan el almacenamiento automáticamente. El resultado es una mayor eficacia y rapidez operativa.
Los vehículos AMR, los robots y todos los sistemas de manipulación que operan en almacenes de temperatura controlada o en cámaras frigoríficas tienen diferentes características en su diseño. Las condiciones particulares de temperatura y humedad pueden afectar al funcionamiento y combinarse de tal manera que pueden ser incluso peligrosas.
Los menores costes, en este caso, están siempre relacionados con una menor pérdida de energía, una menor exposición de los productos almacenados a posibles contaminantes y la protección de la salud de los operarios.
Monitorización de la cadena de frío con sensores y soluciones IoT
Todas las soluciones citadas se basan en los más modernos sistemas de sensores para detectar la temperatura, la posición y el tamaño, así como en soluciones IoT para analizar y evaluar los datos detectados. El Internet de las Cosas y los sensores ayudan así a garantizar una temperatura constante a lo largo de la cadena de frío y a evitar el derroche de energía.
Así, al crecer de la demanda de este tipo de servicios en el mercado, es posible aprovechar al máximo estas oportunidades tecnológicas para mantener la cadena de frío y mejorar su gestión. Pensemos en el sector del e-grocery o en el farmacéutico, donde la demanda de productos que requieren temperaturas controladas aumenta año tras año.
Por lo tanto, las empresas que operan en estos sectores deben reorganizar sus almacenes, tanto paracumplir con los nuevos requisitos para la correcta manipulación de las mercancías como para reducir los costes y mejorar la eficacia de su sistema logístico.
8 tipos de desperdicios que los almacenes automáticos verticales Modula pueden eliminar
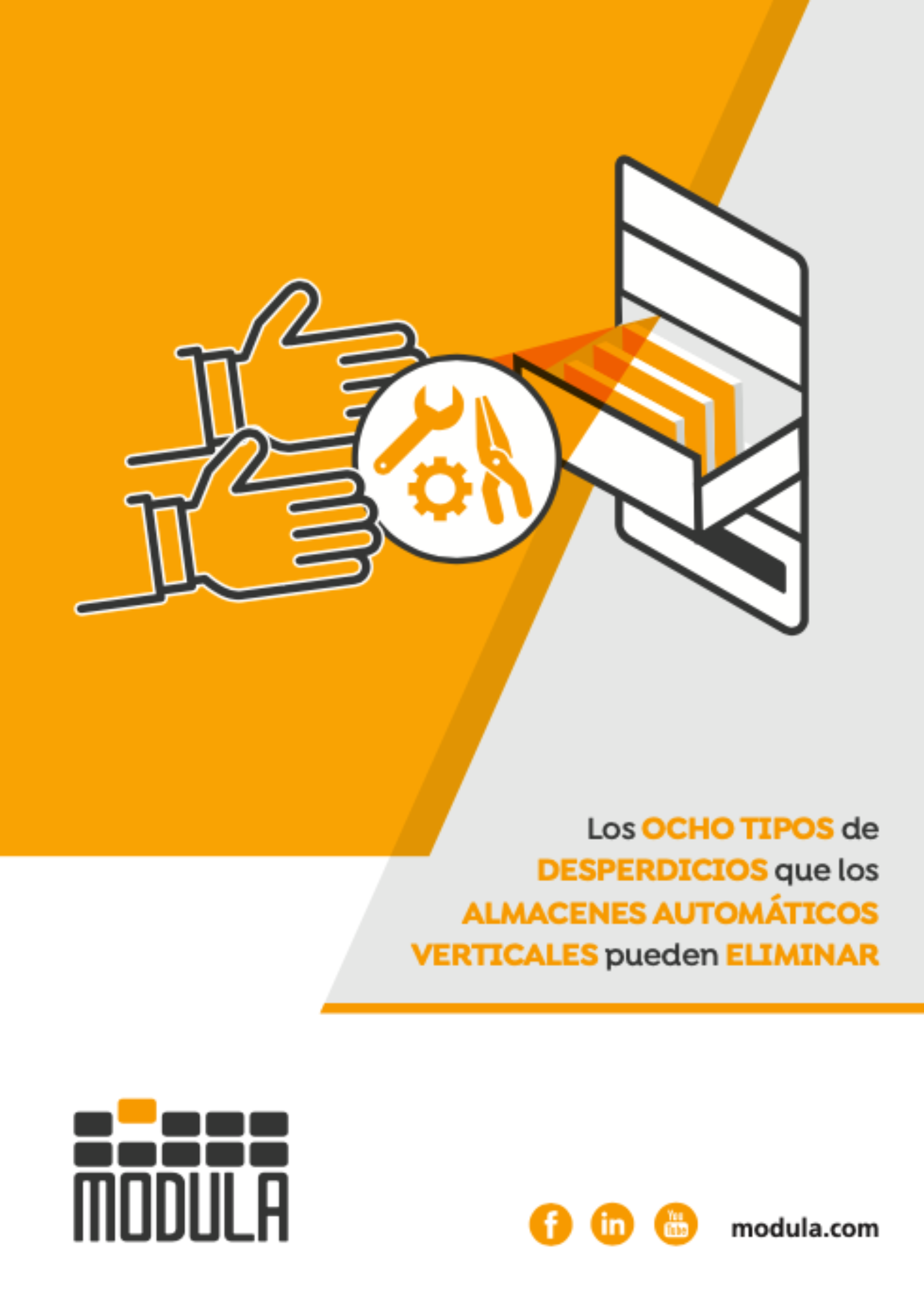