Le système MRP (Material Requirements Planning) est un système de planification du besoin en matériaux qui convient à la gestion de composants nécessaires à la production de produits finis.
C’est une technique bien connue, utilisée pour planifier la production et les commandes, en tenant compte de la demande du marché, de la nomenclature et des délais de production.
Si pensons à un gestionnaire de stock qui gère « ses matériaux » en utilisant les modèles traditionnels (Wilson et ses variantes), nous pouvons facilement imaginer que l’un de ses principaux problèmes est l’estimation correcte de la demande de ces matériaux. En fait, les modèles traditionnels supposent généralement que la demande future est la même que la demande passée (demande historique moyenne).
Tout cela est correct tant que la question est « régulière », mais que se passe-t-il si elle ne l’est pas ?
Que se passe-t-il si la demande se concentre dans certaines périodes (lorsque le produit fini de référence est mis en production), après quoi elle disparaît ? L’erreur est à la base : la demande de ces matériaux ne doit pas être estimée, mais elle doit être calculée en fonction de la demande du produit fini. La planification de la production doit fixer les quantités de produits finis qui devront être produites et, à partir de ces quantités, on peut remonter jusqu’au besoin réel en matériaux y relatif.
Les entrées du système MRP sont 3 :
Le plan de production (MPS)
Le plan de production (MPS) indique les quantités de chaque référence à produire dans un intervalle de temps donné. En général, l’horizon temporel auquel se réfère le plan de production est à court terme. Pour définir les quantités à produire, il faut tenir compte des estimations de la demande pour un produit donné, des commandes en cours déjà reçues et de toutes les contraintes découlant du système de production. Il faut également tenter de définir les quantités à produire de manière assez régulière.
La nomenclature
La nomenclature est le document qui définit la structure d’un produit, car elle spécifie de quels éléments (matières premières, composants, produits intermédiaires, sous-ensembles, matériel auxiliaire) un produit fini donné est composé et combien d’éléments il contient.
La nomenclature d’un produit est composée de plusieurs niveaux (généralement le produit fini constitue le « niveau zéro », ses composants le « niveau 1 », les composants des composants le « niveau 2 », etc.).
Grâce à la nomenclature, nous pouvons passer des plans de production des produits finis à ceux de leurs composants. L’opération par laquelle un ensemble est transformé en la nomenclature de ses composants est appelée « éclatement ».
État des stocks
L’état des stocks est l’archive constamment mise à jour des matériaux et composants en stock.
Mais comment fonctionne le système MRP ? Des calculs, beaucoup de calculs…
Nous pouvons résumer le fonctionnement du système MRP en définissant les calculs à effectuer. Les voici rassemblés en 5 étapes :
Calcul du besoin brut
Le besoin brut en composants de premier niveau est calculé à partir des commandes à émettre (ou à lancer) pour les produits finis qu’ils constituent. Ce calcul est répété « en cascade » jusqu’à épuisement de la nomenclature : les commandes à émettre des composants de premier niveau fournissent le besoin brut en composants de deuxième niveau et ainsi de suite.
Calcul du besoin net
Il est nécessaire de calculer le besoin net de chaque produit fini, composant, ensemble, sous-ensemble, en tenant compte de la quantité de stock dont nous disposons pour chacun d’eux. Le besoin net est obtenu en soustrayant du besoin brut le stock en main à la fin de la période précédente. Le besoin brut et le besoin net doivent être placés dans le temps avec précision: la date à laquelle les produits finis doivent être disponibles résulte du plan de production, tandis que les dates des composants doivent être calculées à rebours en tenant compte des délais respectifs de production ou d’approvisionnement.
Calcul des commandes à recevoir
À partir du besoin net de chaque produit fini, composant, ensemble, sous-ensemble, nous pouvons déterminer les commandes à recevoir, c’est-à-dire calculer les quantités que nous recevrons effectivement pour chacun d’eux en tenant compte des lots minimums préétabli (production ou approvisionnement). S’il n’y a pas de contraintes sur la quantité à commander ou à produire, les commandes à recevoir coïncident avec le besoin net.
Calcul des ordres à émettre
Les commandes à émettre sont les quantités à commander (ou à produire) pour chaque produit fini, composant, ensemble, sous-ensemble. Les quantités coïncident avec les commandes à recevoir mais les délais sont anticipés.
Calcul des stocks en main à la fin de la période
La dernière étape consiste à déterminer les stocks en main à la fin de la période. Cette valeur résulte des stocks disponibles au début de la période auxquels les commandes à recevoir sont ajoutées et le besoin net pour la même période est soustrait. Il va sans dire que ce calcul doit être répété pour chaque produit.
Avantages et limites du système MRP
Le système MRP est préférable aux systèmes basés sur le point de commande ou sur l’intervalle fixe si la gestion concerne des matériaux destinés à la production, surtout si le produit final est complexe (avec une nomenclature à plusieurs niveaux).
Pour ces produits, nous pouvons souligner les avantages par rapport aux systèmes traditionnels :
- Les niveaux de stock sont plus bas.
- Pas besoin d’estimations précises (et nécessairement basées sur les données historiques) car le système est tourné vers l’avenir et, par conséquent, gère mieux les articles dont la demande est extrêmement variable.
- C’est un outil de planification valable, capable de mettre en évidence les commandes en retard et de signaler si elles entraînent ou non le report du plan de production.
En ce qui concerne les limites, il faut toutefois préciser que l’objectif principal d’un système MRP, c’est-à-dire la minimisation des coûts de stockage des matériaux, n’est atteint que s’il n’y a pas d’obstacles particuliers. Les problèmes du système MRP sont essentiellement liés aux difficultés de collecte et de mise à jour continue des informations nécessaires.
Cela pourrait nous faire penser qu’il est préférable de stocker les composants de faible valeur et à forte consommation ou ceux dont les délais de livraison sont particulièrement longs et donc probablement variables avec des méthodes traditionnelles (par exemple, apparemment il ne vaudrait pas la peine de calculer soigneusement et d’actualiser en permanence le besoin en « vis »).
En réalité, si nous décidons d’adopter un magasin automatique vertical équipé de WMS, tous ces problèmes sont complètement contournés.
Avec un système WMS connecté à un magasin automatique vertical, tous les composants codés qui sont stockés dans le magasin sont suivis, de sorte qu’il est toujours possible de contrôler le stock des différents codes et de passer des commandes à partir des informations ainsi obtenues.
Dans la planification de la production, qui peut être hebdomadaire, mensuelle, annuelle ou d’une périodicité définie, normalement l’on interroge le système ERP de l’entreprise pour lancer les prélèvements. Or, le système ERP ne permet d’obtenir l’état exact des stocks que si chaque opération de prélèvement, de stockage et d’utilisation a été correctement cartographiée et tracée.
Si les matériaux sont stockés dans un magasin automatique équipé d’un WMS (Warehouse Management System), chaque opération de picking, qu’il s’agisse de prélèvement ou de stockage, est enregistrée, codée et envoyée automatiquement au système ERP par le biais de protocoles d’échange de données.
Pour ceux qui sont impliqués dans la planification de la production, il sera presque impossible de faire des erreurs ou de lancer la production d’une pièce dont des composants font défaut précisément parce que le stock est mis à jour en temps réel.
Une fois le système ERP interrogé, seuls les quantités nécessaires sont planifiées et effectivement prélevées. Une fois le prélèvement effectué, le système WMS communique automatiquement la quantité mise à jour au système ERP, ce qui virtuellement disponible un inventaire juste à temps.
Le risque d’erreur pratiquement disparaît et il n’est plus nécessaire de procéder à un inventaire physique et/ou manuel. La gestion des stocks par le système MRP est donc la pratique idéale pour un processus de production conforme aux principes les plus modernes de la production allégée.
40 KPI de magasin pour contrôler et mesurer les performances
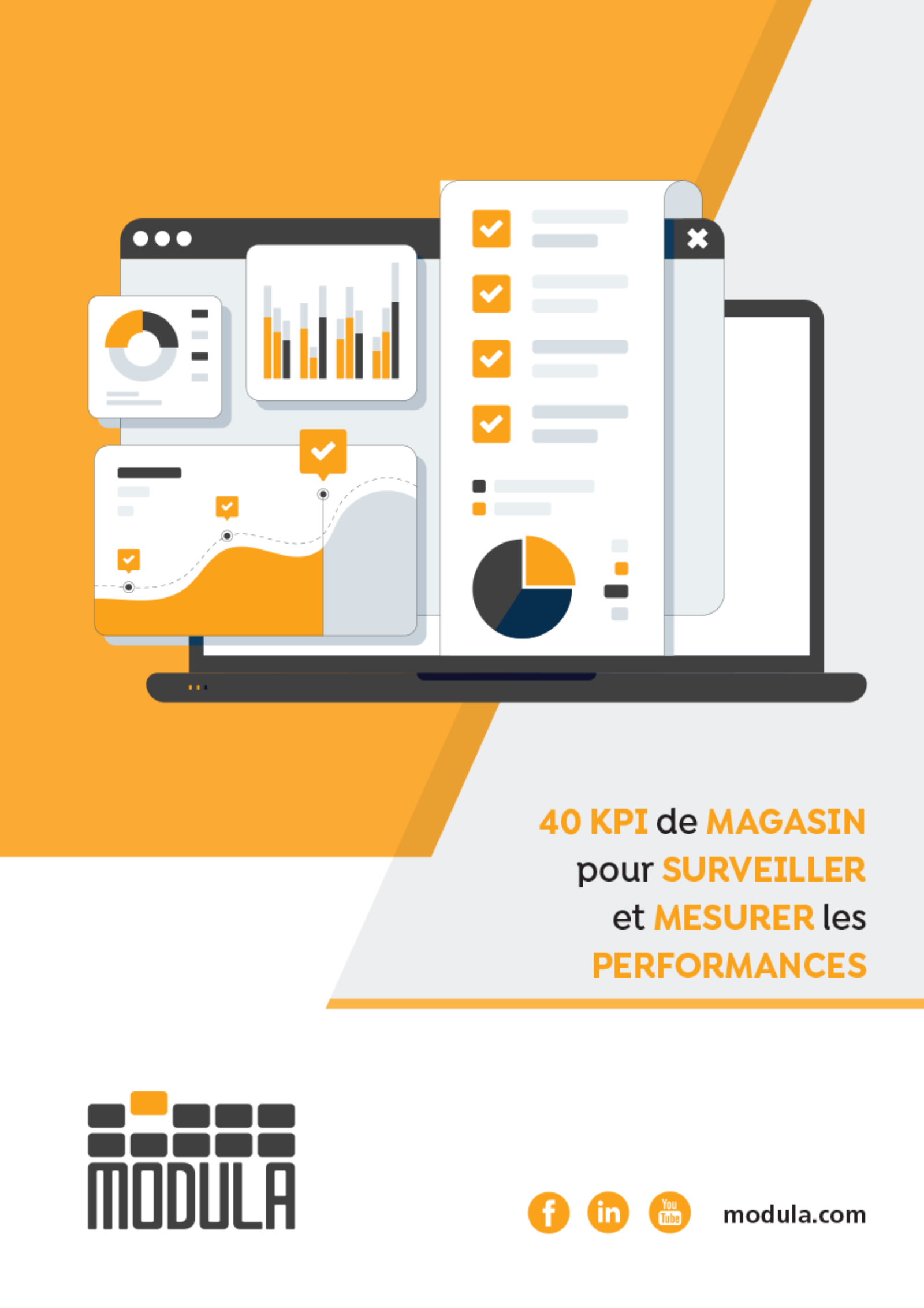