« Celui qui cesse de s’améliorer, cesse de bien faire. »
« C’est comme ça qu’on a toujours fait » n’est plus à la mode. Parce que si vous continuez à faire ce que vous avez toujours fait, vous obtiendrez toujours les mêmes résultats.
La vraie question à se poser pour rester efficace et performant est la suivante : « Qu’est-ce qui peut être amélioré ? »
C’est ainsi que Federica Mosto, Kaizen Manager chez Modula, aborde son travail au quotidien.
Le mot « Kaizen » est la fusion de deux termes japonais, KAI (changement) et ZEN (bon, meilleur), et signifie changement pour le mieux, amélioration continue. Ce terme fait donc référence à l’importance pour une organisation d’introduire des améliorations progressives et continues dans ses processus, produits et services. Le terme a été inventé par Masaaki Imai en 1986 pour décrire la philosophie d’entreprise qui a été à la base des succès de l’industrie japonaise dans les années 1980, avec une référence particulière à Toyota, dont Modula s’est également souvent inspiré pour l’approche Lean utilisée dans l’entreprise.
« Allez au Gemba [place réelle] et regardez ! ». Federica passe la plupart de son temps dans les départements de production de Modula et observe ce qui se passe.
Elle recueille les avis et les commentaires de ceux qui travaillent à plein temps dans le processus. Si quelque chose ne va pas dans les activités quotidiennes ou les éventuels gaspillages détectés (muda, en japonais, qui sont considérés comme de véritables déshonneurs) et elle adopte des mesures d’urgence, discute du problème avec les responsables, s’assure qu’il y a un environnement de travail sûr et prend soin d’éliminer tous les obstacles que les employés rencontrent dans les opérations quotidiennes.
« Il faut analyser en détail le problème en appliquant la règle des « 5 pourquoi » pour aller à la racine. Ensuite, une première étape d’amélioration est convenue et la solution est mise en œuvre (qui n’est pas nécessairement permanente ; l’important est qu’elle apporte un bénéfice initial). Il faut toutefois veiller à fixer des normes pour éviter que l’anomalie ne se reproduise dans un court laps de temps.
Cependant, le travail ne s’arrête pas là, car chaque amélioration en déclenche une autre et ainsi de suite. »
« Il est facile d’avoir une idée compliquée. Ce qui est vraiment, vraiment compliqué, c’est d’avoir une idée simple. »
Les processus peuvent, voire doivent, progresser par le biais d’évolutions modestes mais continues. La technique utilisée est le célèbre la roue de Deming ou cycle PDCA : Plan >> Do >> Check >> Act, en français Planifier >> Déployer >> Contrôler >> Agir.
« Les meilleures suggestions sont celles recueillies dans les départements, les idées et propositions émises par ceux qui travaillent directement dans le processus tous les jours et apportent de la valeur. »
Amélioration des processus d’entreprise : première phase de planification
La première phase consiste à définir les OBJECTIFS et à planifier les améliorations. Sous notre loupe ont toujours été les processus de production, le cœur de notre système. Réduire les gaspillages et les erreurs, accélérer les temps de production, minimiser les temps d’arrêt, améliorer la qualité du produit fini et gérer les coûts. Pour cela, il faut regarder de près mais aussi savoir clairement où l’on veut aller, suggère Federica Mosto.
Les projets d’amélioration peuvent concerner le produit, le processus, l’informatisation et la chaîne d’approvisionnement.
Une activité importante que nous avons décidé d’analyser est l’optimisation des processus de production et d’approvisionnement : un coût considérable pour notre entreprise, qui doit traiter quotidiennement avec plusieurs fournisseurs. Le fait de disposer de méthodes claires et définies de livraison et de collecte des matériaux nous permet de nous concentrer sur le développement de notre activité principale et nous donne un avantage concurrentiel considérable en optimisant le flux de travail dans l’entrepôt et en assurant un contrôle à 360° de la logistique tierce partie.
Comment agir pour résoudre le problème : deuxième phase de déploiement
Le DO [DÉPLOIEMENT] est la phase la plus factuelle du projet. Une fois le problème défini, il faut le comprendre et l’analyser dans toutes ses composantes pour savoir comment agir. Chez Modula, suite à une analyse de l’existant, nous avons, par exemple, identifié certaines inefficacités liées aux coûts élevés de transport de la production. Nous avons ensuite cherché à savoir plus en détail quelle était la raison et à quel moment du processus il fallait agir.
Dans ce cas précis, nous nous sommes rendu compte que pour certains voyages aller-retour récurrents qui étaient organisés entre nous et deux fournisseurs différents il y avait une bonne marge d’amélioration et que, dans une perspective de partenariat, le changement pouvait garantir un avantage pour les trois acteurs impliqués. Une triangulation des déplacements a donc été envisagée, testée pendant une période, et les résultats ont été multiples : en plus de simplifier le processus, et de nous garantir une économie non négligeable (-185 k€ par an), il a été possible de mettre en œuvre un pas vers la durabilité, en réduisant la consommation et la pollution.
Je dirais que c’est une grande réussite pour l’une des innombrables possibilités d’amélioration auxquelles le Kaizen manager est confronté.
Vérifier le succès des changements : troisième et quatrième phase de contrôle et d’action
La phase de DÉPLOIEMENT est suivie de la phase de CONTRÔLE pour vérifier le succès, qui dépend de l’achèvement du processus d’amélioration et du maintien des actions entreprises.
Il est crucial pour le Kaizen manager de s’assurer que les nouveaux processus sont correctement établis. Il est donc nécessaire de mesurer régulièrement les performances, tant en termes de processus que d’action, afin de documenter les améliorations obtenues à moyen et long terme. (ACTION)
« L’amélioration continue est préférable à la perfection retardée. »
« L’année où le rôle a été lancé dans l’entreprise, il y avait 36 projets ouverts où des optimisations pouvaient être mises en œuvre. Aujourd’hui, il y a 407 projets d’amélioration chez Modula, dont 156 sont terminés, 103 sont en cours, 102 sont en attente/refusés (parce que les idées ne sont pas toutes initiées ; l’important est de fournir un retour et une motivation. Certaines activités peuvent être mises en veilleuse en attendant que le moment soit suffisamment « mûr » pour lancer le projet de manière rentable) et 41 sont à initier », confirme aujourd’hui Federica avec une grande satisfaction.
Vous voulez rendre votre entrepôt plus efficace ?
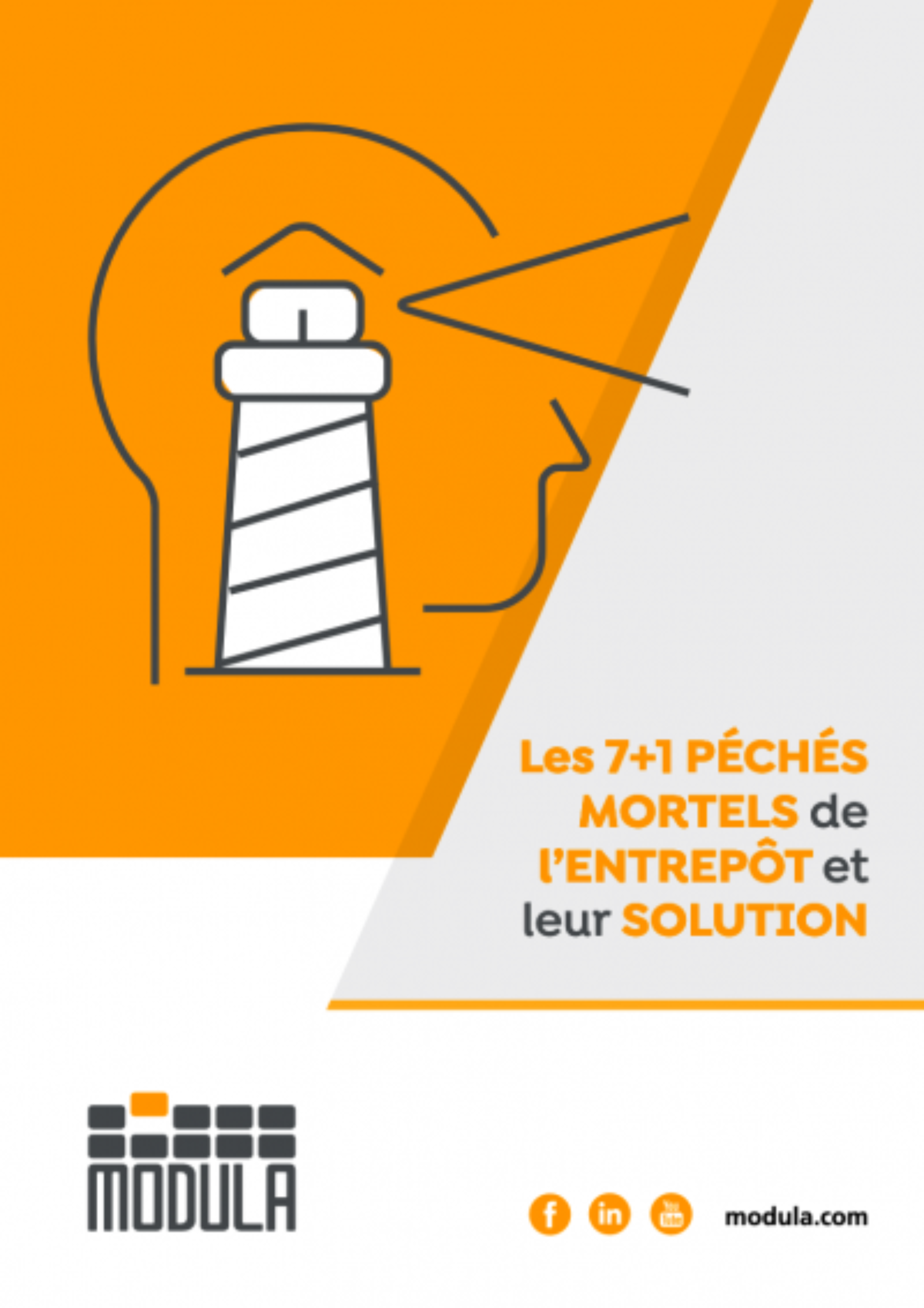