Che si tratti di eliminare gli sprechi di tempo – rimuovendo processi di magazzino macchinosi – o di garantire la sicurezza dei dipendenti, il lean warehousing rappresenta la soluzione ideale a diverse sfide legate alla gestione del magazzino.
Il Lean Warehousing è un approccio alla gestione del magazzino che elimina i processi o le attività di magazzino che non contribuiscono alla creazione di valore aggiunto, riducendo gli sprechi e migliorando la produttività.
Originario dell’industria manifatturiera, in particolare nel settore automobilistico con Toyota, il Lean Warehousing mira a massimizzare l’efficienza.
Per esemplificare consideriamo un processo di picking manuale:
In questo caso, gli addetti, devono utilizzare elenchi di prelievo e muoversi frequentemente tra le posizioni di picking. Queste fasi, se non ottimizzate, rappresentano uno spreco poiché richiedono risorse preziose ma non aggiungono valore concreto per il cliente finale.
Il Lean Warehousing interviene per semplificare e ottimizzare tali processi, eliminando gli sprechi e garantendo una maggiore produttività complessiva.
Per affrontare efficacemente lo spreco di risorse associato al picking manuale, l’adozione del lean warehousing richiede l’implementazione di soluzioni di picking automatizzate.
Questo significa introdurre processi ottimizzati e snelli che migliorano la produttività e riducono gli sprechi.
Quindi, il lean warehousing si traduce in:
- Migliorare la produttività: concentrandosi sull’eliminazione dei processi di magazzino che generano sprechi, come la sovrapproduzione o scorte in eccesso.
- Aumentare la sicurezza degli operatori: lean è sinonimo di sicurezza sul posto di lavoro; infatti aumentando l’automazione del magazzino con soluzioni di stoccaggio verticali automatiche si riducono gli spostamenti tra gli scaffali e, di conseguenza, il rischio di infortunio.
- Migliorare la corresponsabilizzazione dei dipendenti: I principi Lean promuovono la partecipazione e la responsabilizzazione dei dipendenti che, coinvolti nelle iniziative di miglioramento continuo, si sentono più importanti, apprezzati e motivati a contribuire al successo del magazzino.
- Ridurre i tempi morti: Migliorando i processi in tutto il magazzino, è possibile ridurre i tempi di inattività e garantire che le operazioni di magazzino si svolgano senza intoppi.
- Ridurre la necessità di spazio di stoccaggio: Invece di trasferire le attività in una struttura più grande, l’implementazione dell’approccio lean nel magazzino consente di risparmiare sui costi associati all’espansione del magazzino o all’affitto di ulteriori strutture di stoccaggio.
I principi delle 5S del Lean Warehousing
I principi delle 5S sono una componente fondamentale di tutte le metodologie lean, compreso il lean warehousing.
Questi principi, derivanti da cinque termini giapponesi, comprendono:
1. Ordinamento (Seiri)
Il principio dell’ordinamento stabilisce che ogni articolo presente in magazzino deve essere valutato accuratamente per poterne identificare e quantificare il valore. Tutti gli articoli obsoleti, ridondanti o usati raramente devono essere eliminati.
Per applicare questo principio, è necessario identificare ed eliminare tutto ciò che non viene utilizzato regolarmente, a partire dagli articoli non necessari come gli strumenti e le attrezzature obsolete.
In caso di un sistema inventariale statico – o fermo per un lungo periodo di tempo – potrebbe essere utile immagazzinare questi articoli in un’area di stoccaggio separata, liberando così spazio nel magazzino. In questo modo gli operatori di troveranno più facilmente gli articoli più movimentati e richiesti, migliorando l’efficienza.
2. Ordine (Seiton)
Il principio del mettere in ordine stabilisce che gli articoli devono essere conservati in posizioni specifiche in base alla loro frequenza d’uso, garantendo un facile accesso al momento del prelievo.
Per attuare questo principio è possibile applicare il metodo di analisi ABC per classificare i beni in base al loro valore e al loro fatturato.
Seguendo questa logica, gli articoli a rotazione rapida (categoria A) saranno stoccati in aree di facile accesso, possibilmente vicino all’area di spedizione. Al contempo, gli articoli a rotazione lenta (categoria C) verranno posizionati in aree meno frequentate, come i mezzanini o l’angolo posteriore del magazzino.
3. Lucentezza (Seiso)
Il principio della lucentezza sostiene che un magazzino pulito e ben tenuto è fondamentale per promuovere la sicurezza e l’efficienza.
Per generare lucentezza è importante seguire alcune linee guida:
- Stabilire una routine per le regolari attività di pulizia e organizzazione: creare un vero e proprio calendario per spazzare, pulire le superfici e rimuovere i detriti o sporcizia.
- Regolamentare e assegnare queste responsabilità a specifici addetti del magazzino o a servizi di pulizia professionali.
- Sfruttare scaffali, rastrelliere e cestini: avere cura di immagazzinare gli articoli in modo organizzato e facilmente accessibile. In questi casi si possono ottimizzare o implementare sistemi di etichettatura o scanner di codici a barre per facilitare l’identificazione e il recupero delle merci. Modula realizza diverse soluzioni di automazione ideali per questo scopo.
- Ottimizzare il layout del magazzino: ridurre al minimo il traffico per favorire una movimentazione efficiente delle merci. Definire dei percorsi che siano liberi da ingombri e riservare delle corsie predefinite per attrezzature e macchinari come i carrelli elevatori o transpallet.
4. Standardizzare (Seiketsu)
Il principio di standardizzazione sottolinea l’importanza di stabilire e seguire processi, procedure e linee guida coerenti, al fine di mantenere l’efficienza.
Per implementare questo principio è fondamentale:
- Documentare i processi e le procedure esistenti all’interno del magazzino. Dai flussi di lavoro, alla gestione dell’inventario, dalla ricezione degli ordini, prelievo e imballaggio fino ai processi di spedizione. Inoltre, è importante prendere nota di eventuali variazioni o inefficienze riscontrate durante questi processi.
- Effettuare un’analisi dei processi documentati e identificare le aree in cui è possibile mettere in atto delle best practice. Si tratta di individuare i modi più efficienti ed efficaci per svolgere le attività, ridurre gli sprechi e migliorare la produttività complessiva. Sicuramente, è utile identificare un benchmark rispetto agli standard del settore e confrontarsi con gli operatori direttamente coinvolti nei processi.
- Fornire istruzioni di lavoro chiare e concise per ogni attività o processo. Queste istruzioni servono a definire le procedure, i risultati attesi, gli standard di qualità e le precauzioni di sicurezza da adottare.
Queste indicazioni di lavoro standardizzate sono un punto di riferimento per i dipendenti che devono eseguire i loro compiti in modo coerente. - Formare adeguatamente il personale di magazzino in merito alle procedure di lavoro standardizzate. È fondamentale che i dipendenti comprendano i processi, seguano le linee guida e siano in grado di svolgere i loro compiti secondo gli standard del settore.
- Utilizzare indicazioni visive come cartelli, etichette, indicatori colorati o segnaletica per rappresentare visivamente i processi e le istruzioni standardizzate. Questi strumenti di gestione visiva aiutano i dipendenti a identificare facilmente le procedure, i luoghi o i materiali corretti, riducendo gli errori e promuovendo anche il rispetto degli standard di sicurezza.
5. Sostenere (Shitsuke)
Il principio di sostenibilità afferma che le prime quattro S (ordinamento, ordine,lucentezza e standardizzare) devono essere mantenute in modo costante, al fine di creare una cultura del miglioramento continuo.
Per applicare e sostenere questo principio occorre:
- Pianificare controlli regolari per identificare le aree che necessitano di miglioramenti e garantire il mantenimento degli standard.
- Fornire una formazione continua. Ribadire e ricordare costantemente l’importanza delle pratiche 5S e assicurarsi che gli operatori di magazzino sappiano come applicarle.
- Riconoscere il valore dei dipendenti del magazzino. Premiare il personale che mantiene standard elevati è fondamentale per aumentare il morale e la soddisfazione professionale, incoraggiando anche altri operatori a seguire il loro esempio
Come implementare l’approccio lean del magazzino
Una volta definiti gli step strategici, occorre mettere in pratica le best practice più adatte alle operazioni quotidiane di magazzino.
Per implementare al meglio l’approccio lean nella propria quotidianità:
1. Verificare continuamente i processi di magazzino
L’audit dei processi di magazzino è fondamentale per identificare le inefficienze e le aree da migliorare.
- Definire gli obiettivi: questi potrebbero includere il miglioramento dell’efficienza, la riduzione dei costi, la garanzia di conformità alla sicurezza, il miglioramento del servizio clienti o l’identificazione delle esigenze di formazione.
- Stilare una lista di controllo per l’audit: redigere un elenco di aree da esaminare in base agli obiettivi. Ad esempio, la gestione dell’inventario, il prelievo degli ordini, l’imballaggio e la spedizione, la manutenzione delle attrezzature, l’utilizzo degli spazi e la formazione dei dipendenti.
- Raccogliere dati: raccogliere informazioni mediante diverse strategie, come ispezioni fisiche, interviste al personale, revisione della documentazione (come i registri di spedizione o i registri di sicurezza) e dei dati di sistema (come i tempi di evasione degli ordini o i tassi di errore).
- Analizzare i dati: identificare pattern o schemi che permettano di identificare uno o più problemi. Ad esempio, se in una certa stagione si verificano frequenti esaurimenti di scorte di specifici articoli, ciò potrebbe indicare l’inadeguatezza delle scorte di articoli a rapida rotazione.
- Creare un benchmark delle prestazioni: è sempre importante confrontare le proprie prestazioni con gli standard del settore e/o con le prestazioni storicizzate per individuare le aree da migliorare.
- Fornire delle aspettative: sulla base dei risultati ottenuti, raccomandare/richiedere dei miglioramenti. Questo contribuirebbe al continuo miglioramento di procedure, attrezzature, strutture o know how dei dipendenti.
- Presentare i risultati: è importante preparare e presentare una relazione che illustri i risultati e aspettative alle parti interessate.
2. Implementare la gestione delle scorte Just-in-Time (JIT)
Il Just-in-time (JIT) è una tipologia di gestione delle scorte che richiede una stretta collaborazione con i fornitori per garantire un efficiente e stabile flusso di approvvigionamento.
Gestire il materiale stoccato seguendo la logica JIT consente di aumentare l’efficienza, eliminare le scorte in eccesso e ridurre i costi di immagazzinamento, tutti obiettivi perfettamente in linea con l’approccio lean.
Per poter tradurre in azione questa metodologia di gestione delle scorte, è fondamentale:
- Raccogliere i dati storici delle vendite in modo dettagliato (per esempio, creando dei cluster in base al comportamento dei consumatori o per tipologia di SKU) per avere un quadro preciso dei modelli di domanda.
- Sviluppare relazioni solide con i fornitori e coinvolgerli nel processo di pianificazione, comunicando le previsioni della domanda e assicurandovi che queste possano essere soddisfatte in termini di quantità, qualità e tempistica.
- Implementare un software di gestione, come Modula WMS, delle scorte che esegua automaticamente gli ordini di acquisto quando le merci raggiungono determinati livelli. L’obiettivo principale è non rischiare di rimanere a corto di materiale in scorta.
- Implementare misure rigorose di controllo della qualità nelle operazioni interne e con i fornitori.
3. Formare i dipendenti del magazzino
Per poter contare su un magazzino lean, è necessario intervenire non solo sui processi, ma anche sulla mentalità dei dipendenti.
La formazione dei dipendenti del magazzino è fondamentale per garantire un’estesa comprensione dei principi della produzione lean e, soprattutto, di come attuarli.
Per avvicinare gli addetti a queste logiche e procedure occorre:
- Fornire un programma di orientamento completo per i nuovi dipendenti. Questo potrebbe includere un’introduzione generale ai principi del lean warehousing, unita a una panoramica dei processi e delle procedure specifiche dell’azienda. Inoltre, è di vitale importanza spiegare ruoli e responsabilità di ciascun addetto all’interno del magazzino.
- Offrire sessioni di formazione specifiche incentrate sui principi e sulle pratiche del magazzino snello, come la metodologia delle 5S, la mappatura del flusso del valore, le tecniche di riduzione degli sprechi, la gestione visiva e gli strumenti di risoluzione dei problemi per il miglioramento continuo.
- Fornire ai dipendenti opportunità di formazione pratica, come simulazioni, esercizi guidati o incarichi di lavoro reali.
4. Utilizzare l’automazione del magazzino
L’automazione può migliorare significativamente l’efficienza e l’accuratezza del magazzino, obiettivi che si allineano perfettamente all’approccio lean.
Le soluzioni di magazzino automatizzate comprendono sistemi di stoccaggio e prelievo automatizzati (ASRS), sistemi di prelievo robotizzati e sistemi di gestione del magazzino.
Modula in qualità di leader nelle soluzioni di stoccaggio automatizzato e nei sistemi di gestione del magazzino, offre soluzioni avanzate in grado di migliorare la produttività, l’efficienza e l’accuratezza del picking.
Le soluzioni proposte dall’azienda comprendono:
Magazzini automatici verticali come:
Software di gestione (WMS) che permette:
- Monitorare e tenere traccia dei livelli di scorte e dei movimenti di magazzino
- Migliorare l’accuratezza e la velocità di prelievo se abbinato con specifici sistemi Modula
Soluzioni di picking per:
- Migliorare l’accuratezza e la velocità di prelievo grazie a dispositivi luminosi che guidano gli operatori di magazzino nella giusta posizione
- Migliorare la gestione dell’inventario con una visione completa delle scorte attuali e previste
5. Utilizzare il miglioramento continuo (Kaizen)
Il processo per rendere lean la propria attività non termina una volta implementati i miglioramenti iniziali, si tratta di un percorso continuo.
È possibile garantire l’efficienza di quest’ultimo organizzando riunioni e momenti di confronto regolari per discutere, confrontarsi e lavorare in team per risolvere un problema particolare.
Negli ultimi anni, sempre nell’ottica di uno snellimento dei processi, anche Modula ha deciso di dotarsi di un Kaizen manager per monitorare e migliorare i processi aziendali.
Le soluzioni avanzate di stoccaggio e il sistema di gestione del magazzino di Modula sono pensate e strutturate per sostenere e promuovere un approccio lean verso le operazioni di magazzino, migliorando le attività e aumentando la produttività e l’efficienza dei dipendenti.
Ottimizzare la logistica con soluzioni tecnologiche innovative
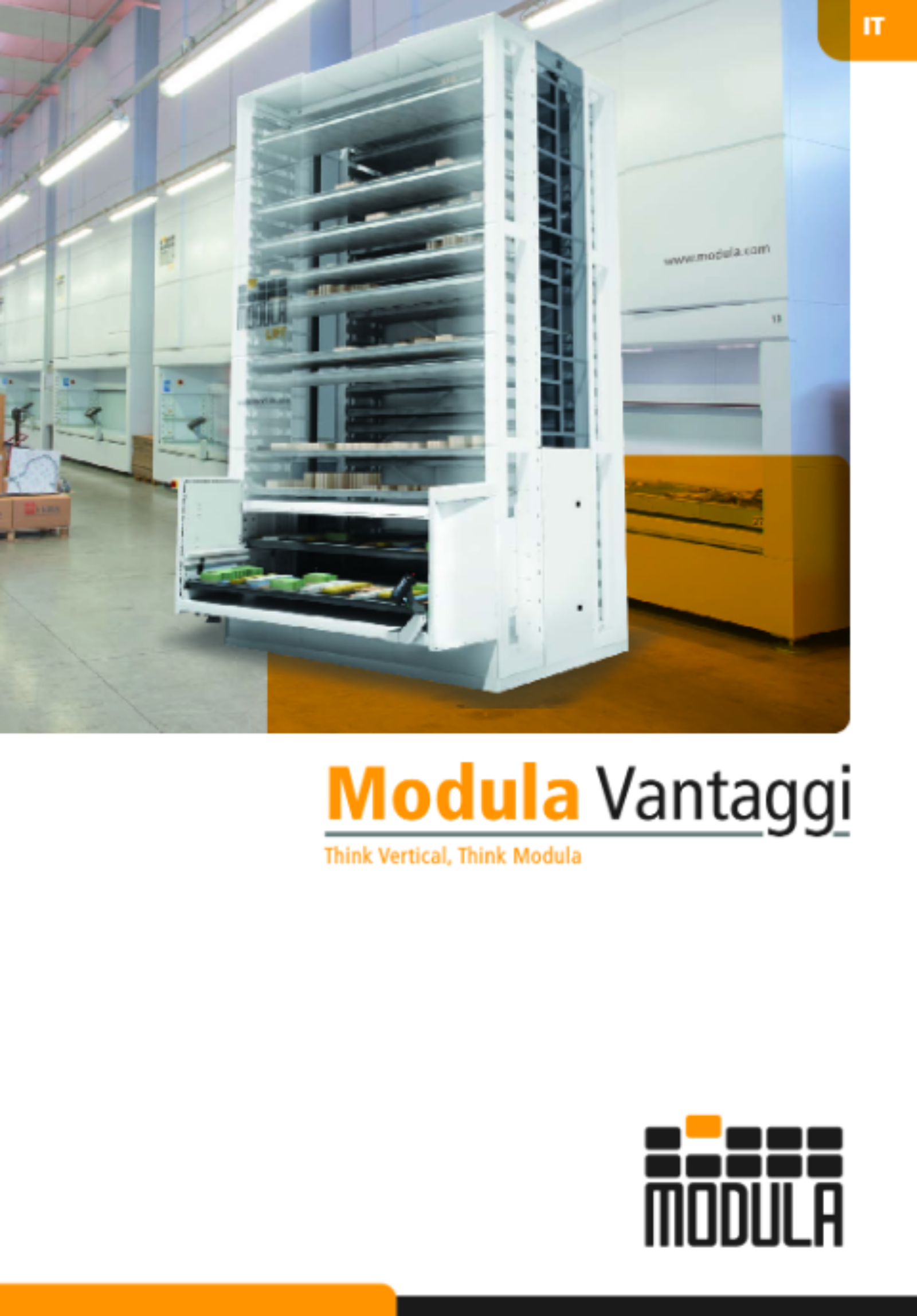