Il sistema MRP (Material Requirement Planning) è un sistema di pianificazione dei fabbisogni di materiali adatto alla gestione di componenti che servono per la produzione di prodotti finiti. È una tecnica ormai nota, utilizzata per pianificare gli ordini di produzione e di acquisto, tenendo conto della domanda del mercato, della distinta base, dei lead time di produzione.
Se pensiamo ad un gestore delle scorte che gestisce i “suoi materiali” utilizzando i modelli tradizionali (Wilson e sue varianti), possiamo immaginare come uno dei suoi problemi principali possa essere quello di stimare la domanda corretta di questi materiali. Infatti i modelli tradizionali assumono generalmente che la domanda futura si presenti in modo analogo a quella passata (domanda storica media).
Tutto ciò è corretto finché la domanda è “regolare”, ma cosa succede in caso contrario?
Se la domanda si concentra in alcuni periodi (quando viene messo in produzione il prodotto finito di riferimento) e poi si azzera? L’errore sta alla base: la domanda di questi materiali non va prevista ma calcolata sulla base della domanda del prodotto finito. La programmazione della produzione deve fissare le quantità dei prodotti finiti che sarà necessario produrre e da tali quantità si può risalire al reale fabbisogno dei materiali che li compongono.
Gli input del sistema MRP sono 3:
Il programma di produzione (Master Production Schedule, MPS)
Il programma di produzione (MPS) riporta le quantità da produrre di ogni referenza in un dato intervallo temporale. Generalmente l’orizzonte temporale a cui si riferisce il programma di produzione è di breve periodo.
Per definire le quantità da produrre si deve tener conto delle previsioni della domanda di un dato prodotto, degli ordini in mano già ricevuti e di tutti i vincoli derivanti dal sistema produttivo. Si deve inoltre cercare di definire dei quantitativi da produrre abbastanza regolari.
La distinta base
La distinta base è il documento che definisce la struttura di un prodotto, in quanto precisa di quali e quanti elementi (materie prime, componenti, prodotti intermedi, sub assemblati, materiale ausiliario) è composto un dato prodotto finito.
La distinta base di un prodotto si compone di più livelli (generalmente il prodotto finito costituisce il “livello zero”, i suoi componenti il “livello 1”, i componenti dei componenti il “livello 2”, ecc.).
Tramite la distinta base si passa dai programmi di produzione dei prodotti finiti a quelli dei loro componenti. L’operazione mediante la quale un assemblato viene trasformato nella lista dei suoi componenti viene detta “esplosione”.
Lo stato delle scorte
Lo stato delle scorte è l’archivio costantemente aggiornato di quello che sono i materiali e le componenti di scorta che giacciono in magazzino.
Ma come funziona il sistema MRP? Calcoli, tanti calcoli…
Possiamo sintetizzare il funzionamento del sistema MRP definendo i calcoli da effettuare. Eccoli radunati in 5 fasi:
Calcolo dei fabbisogni lordi
I fabbisogni lordi dei componenti di primo livello si deducono dagli ordini da emettere (o lanciare) dei prodotti finiti che essi compongono. Questo calcolo si ripete “a cascata” fino ad esaurimento della distinta base: dagli ordini da emettere dei componenti di primo livello si deducono i fabbisogni lordi dei componenti di secondo livello e così via.
Calcolo dei fabbisogni netti
Occorre calcolare i fabbisogni netti di ogni prodotto finito, componente, assemblato, sub-assemblato, tenendo conto di quanta scorta si ha per ognuno di essi. Il fabbisogno netto si ottiene, infatti, sottraendo dal fabbisogno lordo la scorta in mano a fine periodo precedente. Fabbisogni lordi e netti devono essere collocati nel tempo con esattezza: la data alla quale devono essere disponibili i prodotti finiti risulta dal piano di produzione, mentre le date dei componenti vanno calcolate a ritroso tenendo conto dei rispettivi lead time di produzione o di acquisto.
Calcolo degli ordini da ricevere
Conoscendo i fabbisogni netti di ogni prodotto finito, componente, assemblato, sub-assemblato, è possibile determinare gli ordini da ricevere ossia calcolare le quantità che effettivamente per ognuno di essi si riceveranno tendo conto dei lotti minimi prefissati (di produzione o di acquisto). Se non vi sono vincoli sulla quantità da ordinare o da produrre gli ordini da ricevere coincidono con i fabbisogni netti.
Calcolo degli ordini da emettere
Gli ordini da emettere sono le quantità da ordinare (o da produrre) per ogni prodotto finito, componente, assemblato, sub-assemblato. Le quantità coincidono con gli ordini da ricevere ma sono anticipate nel tempo del lead time.
Calcolo della scorta in mano a fine periodo
L’ultima fase consiste nel determinare la scorta a fine periodo. Essa risulta dalla scorta disponibile a inizio periodo aggiungendo gli ordini da ricevere e sottraendo i fabbisogni netti relativi al periodo stesso. Tale calcolo chiaramente va ripetuto per ogni prodotto.
Vantaggi e limiti del sistema MRP
Il sistema MRP è preferibile rispetto ai sistemi a punto d’ordine o a intervallo fisso se la gestione riguarda materiali destinati alla produzione, soprattutto se il prodotto finale è complesso (con una distinta base a più livelli).
Per questi prodotti è possibile evidenziare i seguenti vantaggi rispetto ai sistemi tradizionali:
- Comporta livelli di scorta più bassi.
- Non ha bisogno di previsioni accurate (e necessariamente basate sui dati del passato) poiché guarda al futuro e dunque gestisce meglio anche gli articoli con domanda estremamente variabile.
- È un valido strumento di programmazione in grado di mettere in evidenza gli ordini in ritardo e di segnalare se questi facciano o meno slittare il piano di produzione.
Per quanto riguarda i limiti, invece, va detto che l’obiettivo principale di un sistema MRP di ridurre al minimo i costi di giacenza dei materiali è conseguito solamente se non vi sono intoppi particolari. I problemi del sistema MRP sono connessi sostanzialmente alle difficoltà di raccolta e di aggiornamento continuo delle informazioni necessarie.
Questo farebbe pensare che fosse preferibile gestire a scorta con metodi tradizionali i componenti a basso valore e di largo consumo (ad esempio non vale la pena calcolare accuratamente e aggiornare continuamente il fabbisogno di “viti”) o quelli che presentano lead time di acquisto particolarmente lunghi e quindi probabilmente variabili.
In realtà se si decide di adottare un magazzino automatico verticale dotato di WMS, anche queste problematiche vengono completamente bypassate.
Con un sistema di WMS collegato a un magazzino automatico verticale, tutti i componenti codificati che vengono versati a magazzino vengono tracciati, quindi è sempre possibile avere sotto controllo lo stock dei codici e fare i riordini sulla base di questo.
Nella programmazione della produzione, che può essere settimanale, mensile, annuale o di una periodicità definita si interroga tendenzialmente il gestionale aziendale (ERP) per lanciare i prelievi. Dal gestionale è possibile ricavare l’esatto stato delle giacenze solo se ogni operazione di prelievo, versamento e utilizzo è stata correttamente mappata e tracciata.
Nel caso il materiale sia depositato in un magazzino automatico, dotato appunto di Warehouse Management System, è facile comprendere che ogni movimento di picking, sia esso prelievo o deposito è registrato e codificato e automaticamente inviato al gestionale tramite protocolli di interscambio dati.
Per chi si occupa di programmazione della produzione sarà quasi impossibile sbagliare riordini o mandare in produzione qualche pezzo con componenti mancanti proprio perché le giacenze sono aggiornate in tempo reale.
Una volta interrogato il gestionale, esso lancia i prelievi solo nella quantità necessarie e queste azioni si trasformano in prelievi per il magazzino. Una volta eseguito il prelievo, il WMS automaticamente comunica al gestionale la quantità aggiornata, rendendo praticamente disponibile un inventario just in time.
Il rischio di errore praticamente scompare e non occorre più un inventario fisico e/o manuale, la gestione a magazzino della tecnica MRP è quindi la pratica ideale per un processo produttivo in linea con i più moderni principi della lean production.
40 KPI di magazzino per monitorare e misurare le prestazioni
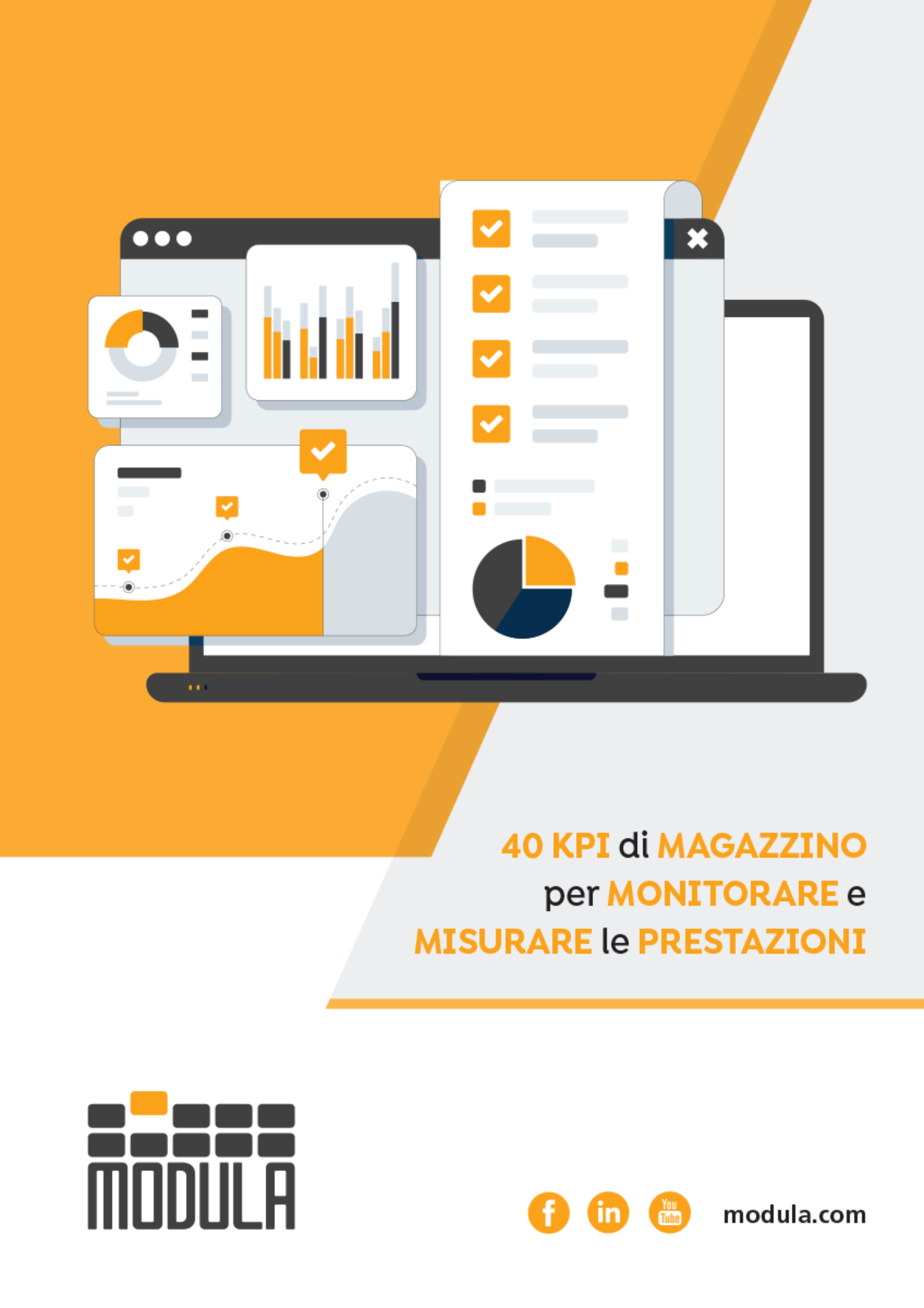